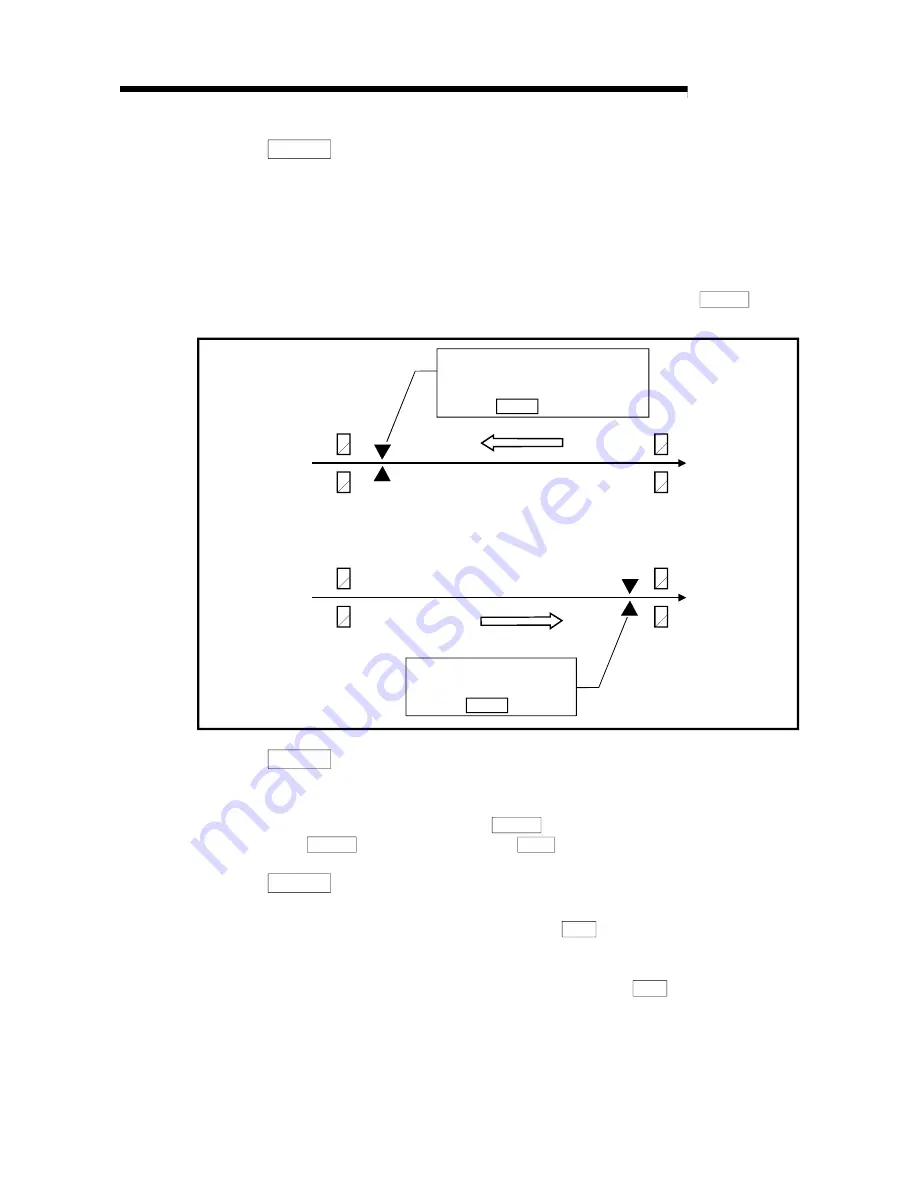
4 - 17 4 - 17
MELSEC-Q
4 DATA USED FOR POSITIONING CONTROL
OPR. 2
OPR direction
Set the direction to start movement when starting machine OPR control.
0: Forward direction
Moves in the direction that the address increments. (Arrow 2))
1: Reverse direction
Moves in the direction that the address decrements. (Arrow 1))
Normally, the OP is set near the lower limit or the upper limit, so "OPR. 2 OPR
direction" is set as shown below.
Lower limit
Address increment
direction
Address decremwnt
direction
Upper limit
When the zero point is set at r\the lower
limit side, the OPR directiion is in the
direction of arrow 1).
Set "1" for OPR. 2
OP
1)
2)
OP
Address decremwnt
direction
Address increment
direction
Upper limit
Lower limit
When th eOP is set st the upper
limit side, th eOPR diredtion
is in direction of arrow 2).
Set "0" for OPR. 2
OPR. 3
OP address
Set the address used as the reference point for position control (ABS system).
(When the machine OPR control is completed, the stop position address is
changed to the address set in " OPR. 3
OP address". At the same time, the
"OPR. 3
OP address" is stored in "Md. 1
Current feed value".)
OPR. 4
OPR speed
Set the speed for OPR control.
Note)
•
Set the "OPR speed" to less than " Pr. 5
Speed limit value". If the "speed
If the "speed limit value" is exceeded, the "Setting range outside OPR
speed" error (error code: 913) will occur.
•
Set the "OPR speed" to a value not less than " Pr. 6
Bias speed at start".
If it is less than the "bias speed at start", the "Setting range outside OPR
speed" error (error code: 913) will occur.
Summary of Contents for GX Configurator-PT
Page 13: ...MEMO SECTION 1...
Page 127: ...7 20 7 20 MELSEC Q 7 SEQUENCE PROGRAM USED FOR POSITIONING CONTROL MEMO...
Page 129: ...MEMO SECTION 2...
Page 221: ...Index 5 Index 5 MEMO...