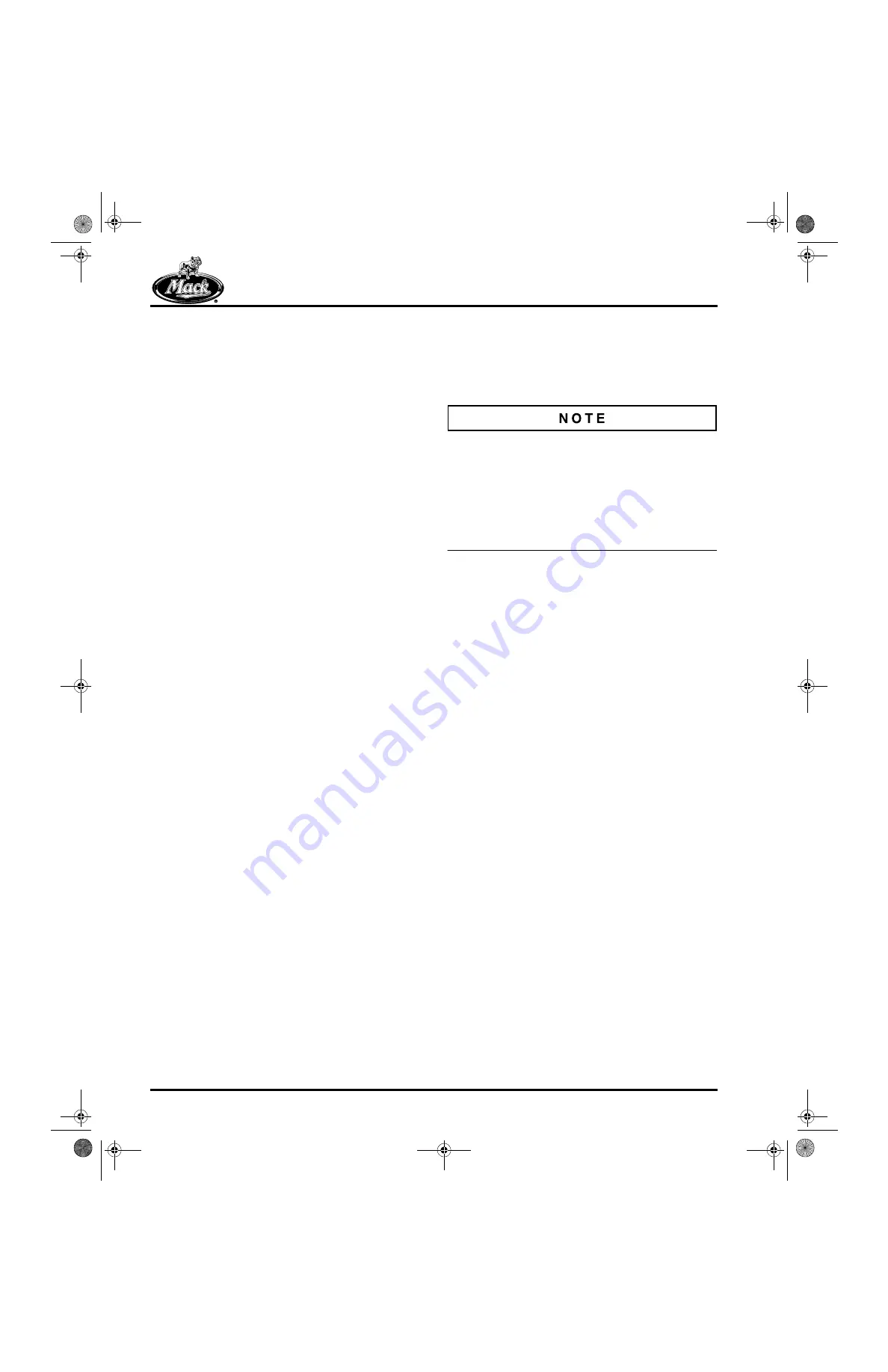
Page 328
SPECIFICATIONS
SPECIFICATION FOOTNOTES
NOTE 1 — AUXILIARY SHAFT GEAR
RETAINING NUT INSTALLATION
r
A new nut has pre-applied thread locker. No
degreasing of a new nut is recommended.
However, degrease shaft threads thoroughly
with Loctite
®
Primer-T, or equivalent, prior to
nut installation.
r
It is acceptable to reuse an auxiliary drive
gear retaining nut. If reusing a nut, the nut
threads, as well as the shaft threads, must
also be thoroughly cleaned with Loctite
®
Primer-T, or equivalent, and Loctite
®
277
used on the nut and shaft threads.
NOTE 2 — MAIN BEARING CAP
INSTALLATION
Main bearing cap assembly shall be performed in
the following steps:
1. Buttress screws installed finger-tight in order
to align the hole in the block and the hole in
the main bearing cap.
2. Main bearing capscrews torqued.
3. Buttress screws torqued.
NOTE 3 — CYLINDER HEAD TORQUING
Cylinder head assembly and torquing is to be
performed as follows:
1. Oil all cylinder head capscrew bosses,
capscrew threads and washers with engine
oil prior to assembly. Do not oil threads in
cylinder block. Using torque wrench
J 24407, or equivalent, tighten capscrews to
specification in three stages on any one
head in the proper sequence, as shown in
the Engine Reassembly procedures section.
a.
Initially, torque all capscrews in
sequence to 50 lb-ft (68 N•m).
b.
Tighten all capscrews in sequence to
125 lb-ft (170 N•m).
c.
Tighten all capscrews in sequence to
the final torque value of 205 lb-ft
(278 N•m).
2. After run-in procedure, in sequence, back off
each capscrew individually until free. Then
retorque same capscrew to 205 lb-ft
(278 N•m).
NOTE 4 — EXHAUST MANIFOLD TORQUING
Torque exhaust manifold nuts to 35 lb-ft (47 N•m)
in a top-to-bottom sequence. Retorque to 80 lb-ft
(109 N•m) following the same top-to-bottom
sequence.
On some E-Tech™ engines, the exhaust
manifold-to-cylinder head stud hole may be
drilled deep enough to allow the stud to enter the
push rod bore. In these instances, the 20 lb-ft
(27 N•m) torque may not be reached until the
stud contacts the push rod. In all cases, a stud
protrusion of 1.75 inch (44.45 mm) must be
maintained.
NOTE 5 — VALVE YOKE SETTING
1. Push down on the slipper face of yoke. Turn
down yoke adjusting screw until it contacts
outboard valve stem tip, as sensed by light
drag on adjusting screw.
2. Turn adjusting screw an additional
60 degrees (1/6 turn) clockwise.
3. Holding yoke adjusting screw in this
position, lock jam nut.
NOTE 6 — HOSE CLAMP INSTALLATION
POSITIONING INFORMATION
The band of any hose clamp in all installations
should be a minimum of 0.090 inch (2.3 mm) from
the end of the hose and must be clear of tube
bead.
NOTE 7 — PIPE PLUG SEALING
All pipe plugs must be sealed using Loctite
®
PST
pipe thread sealant with Teflon
®
, or equivalent.
NOTE 8 — CYLINDER SLEEVE ID
Cylinder sleeve ID may be 4.872 inch
(123.749 mm) minimum at top of sleeve due to
close-in from press fit.
NOTE 9 — REAR SEAL BORE RADIAL
RUNOUT
Runout is to be checked with an alignment bar
installed through the cylinder block main bearing
bores.
5_106_00.bk Page 328 Friday, August 4, 2000 11:17 AM
BDC for engine manuals and specs