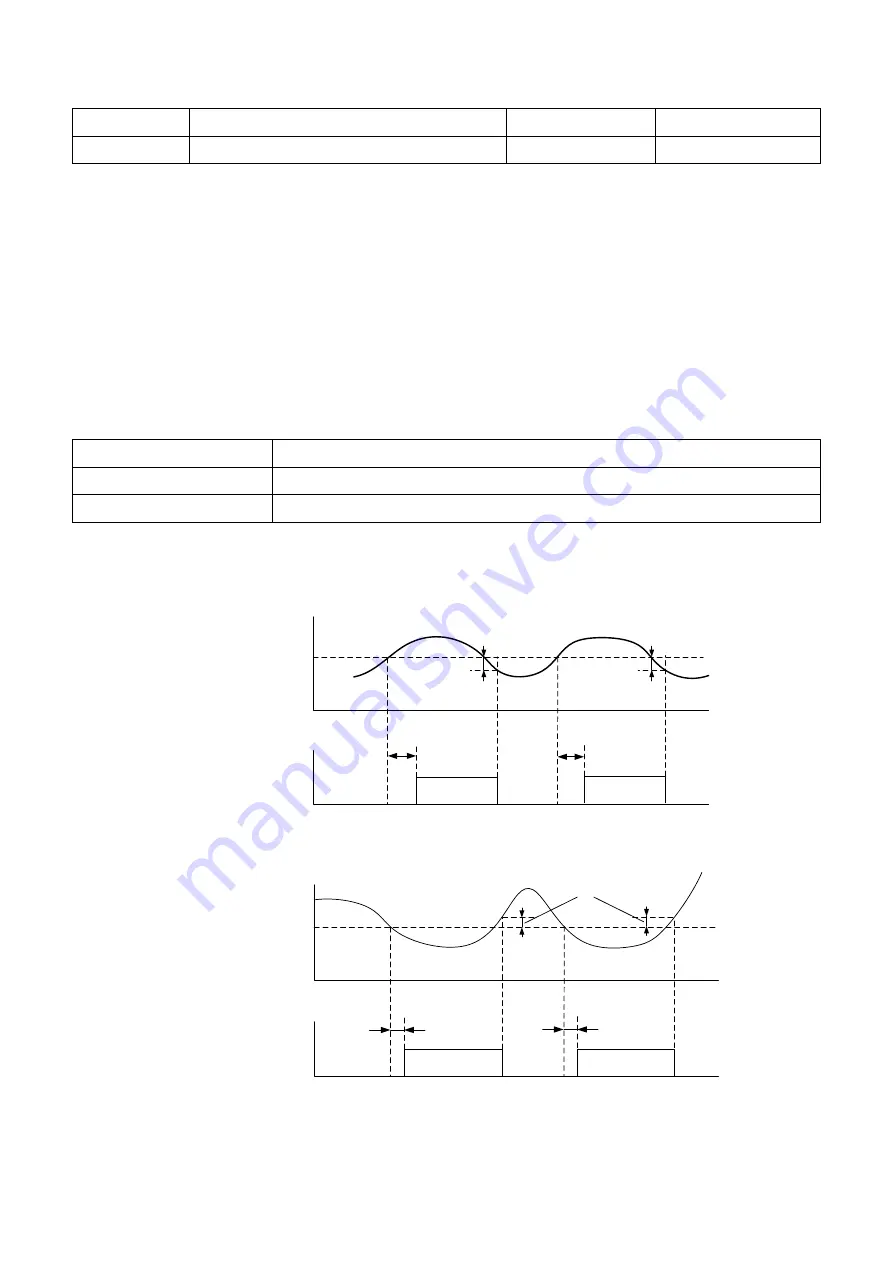
184
No.
Name
Setting Range
Default
P5-02
Fault Restart Interval Time
0.5 to 600.0 s
10.0 s
P6
Overtorque/ Undertorque Detection
When the load is too heavy (overload) or suddenly drops ( undertorque), the drive will output a
torque detection signal to the multi-function output terminal ( Relay 1, Relay 2, D1-DC or
D2-DC). The torque detection function is set by P6 parameters.
CAUTION
! When overtorque occurs, the drive may trigger the fault to stop the motor. To prevent the drive from
stopping, use torque detection to indicate an overload situation before the fault is triggered. Simimar situations
also apply to undertorque. Use undertorque detection to find out application problems such as torn belte, a pump
shutting off and etc.
E2-00 to E2-03 Setting
Name
18
Overvoltage/ Undervoltage Detection 1 (normal open)
20
Overvoltage/ Undervoltage Detection 2 (normal open)
Overtorque and undertorque operations are illustrated in Figure 6.84 and Figure 6.85.
Torque detection 1
or 2
Motor current/
torque
ON
Hysteresis
( 10% )
ON
P6-01 or P6-04
Hysteresis
( 10% )
P6-02 or P6-
05
P6-02 or P6-
05
Figure 6.84 Overtorque Detection Operation
Torque detection 1 or
2
Motor current/
torque
ON
ON
P6-01 or P6-04
Hysteresis
( 10% )
P6-02 or P6-
05
P6-02 or P6-
05
Figure 6.85 Undertorque Detection Operation
Summary of Contents for EVO 6800 Series
Page 1: ...MANUAL Compact Vector Drive EVO 6800 Series...
Page 33: ...33 34 2 36 0 2 8 93 0...
Page 35: ...35 4 2 Main Circuit...
Page 41: ...41 4 3 Control Circuit...