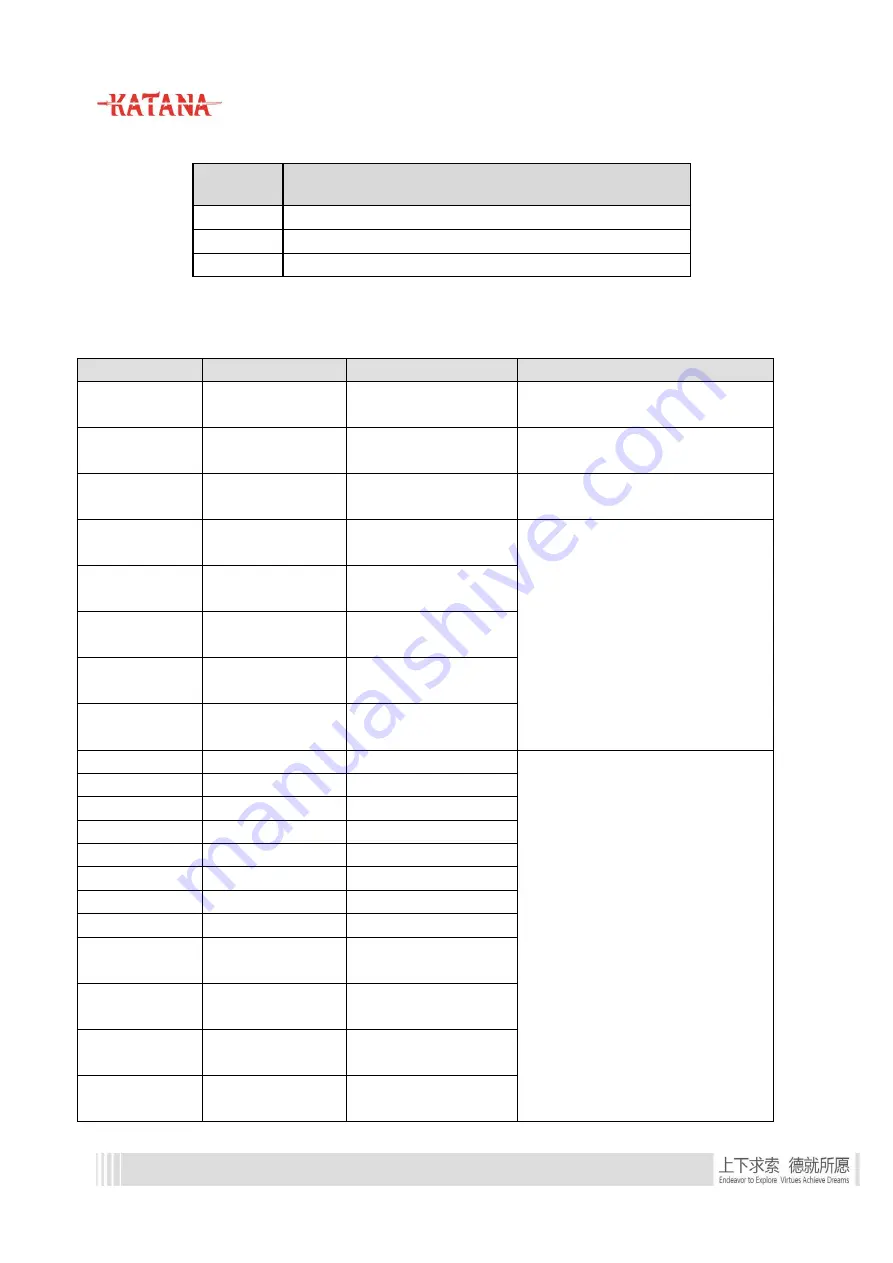
95
KATANA S610M Inverter Specialized for Elevator Manual
Terminal
symbol
Meaning
A-
Encoder differential frequency dividing output A-
B-
Encoder differential frequency dividing output B-
GND
Common port of frequency dividing output
7.2.2 Parameters setting
General function code setting of terminal multi-speed operation mode is shown below as table 7-2.
Table 7-2 Common function code of terminal multi-speed operation setting table
Function Code
Name
Recommend set value
Remarks
F00.01
Control mode
selection
Set according to
actual situation
F00.04
Elevator rated
speed
Set according to
actual situation
F00.07
Maximum output
frequency
Set according to
actual situation
F01.00
Motor rated power
Set according to
actual situation
Motor nameplate parameters
F01.01
Motor rated voltage
Set according to
actual situation
F01.02
Motor rated current
Set according to
actual situation
F01.03
Motor rated
frequency
Set according to
actual situation
F01.04
Motor rated speed
Set according to
actual situation
F06.00
zero-speed start P
200
Adjusting according to the actual
operational aspect, normally use
factory settings.
F06.01
zero-speed start I
100
F06.02
ASR1-P
20.0
F06.03
ASR1-I
0.200
F06.04
ASR1 output filter
0
F06.05
ASR2-P
20.0
F06.06
ASR2-I
0.200
F06.07
ASR2 output filter
0
F06.08
ASR1/2 switching
frequency
10%
F06.09
None-zero speed
torque limit value
180%
F06.10
Zero-speed torque
limit value
180%
F06.11
ACR-P(No-start
current loop P)
1000