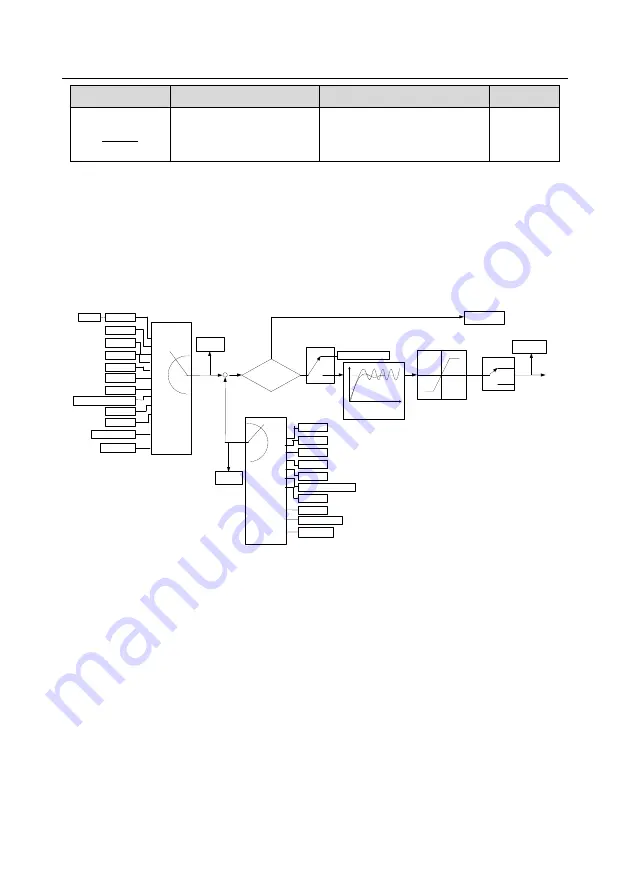
GD350A series high-performance multifunction VFD
-119-
Function code
Name
Description
Default
Simple PLC and present
stage number of multi-step
speed
Displays the present stage of
the simple PLC function.
0
5.5.15 PID control
PID control, a common mode for process control, is mainly used to adjust the VFD output frequency
or output voltage through performing scale-division, integral and differential operations on the
difference between feedback signal of controlled variables and signal of the target, thus forming a
negative feedback system to keep the controlled variables above the target. It is suitable for flow
control, pressure control, temperature control, etc. Diagram of basic principles for output frequency
regulation is shown in the figure below.
+
-
Reference-
feedback<P09.08
?
P09.10
(lower limit value of PID
output)
P09.09
(
upper limit value of PID
output
)
0
1
P09.03
(PID output characteristics)
PID output
P17.00
P17.23
P09.08 (Limit of PID control
deviation)
P09.02
(PID feedback source)
P09.00
(PID reference source)
P17.24
PID feedback
value
PID reference
value
Set frequency
0
1
2
3
4
5
6
7
8
9
Keypad
AI1
PROFIBUS\CANopen
MODBUS
Multi-step
speed
HDIA
AI3
AI2
Ethernet
HDIB
0
1
2
3
4
5
6
7
AI1
PROFIBUS\CANopen
MODBUS
HDIA
AI3
AI2
Ethernet
Y
N
PID stops
adjustment
Pre-set PID reference of
keypad
Keep current frequency
Terminal function 25
PID control pause
Valid
Invalid
Kp P09.04 (proportional gain)
Ti P09.05 (integral time)
Td P09.06 (differential time)
P09.01
EtherCat/Profinet
PLC card
10
11
HDIB
EtherCat/Profinet
PLC card
8
9
10
Introduction to the working principles and control methods for PID control
Proportional control (Kp): When the feedback deviates from the reference, the output will be
proportional to the deviation, if such deviation is constant, the regulating variable will also be constant.
Proportional control can respond to feedback changes rapidly, however, it cannot eliminate the error
by itself. The larger the proportional gain, the faster the regulating speed, but too large gain will result
in oscillation. To solve this problem, first, set the integral time to a large value and the derivative time
to 0, and run the system by proportional control, and then change the reference to observe the
deviation between feedback signal and the reference (static difference), if the static difference is (e.g.,
increase the reference, and the feedback variable is always less than the reference after system
stabilizes), continue increasing the proportional gain, otherwise, decrease the proportional gain; repeat
such process until the static error becomes small.
Integral time (Ti): When feedback deviates from reference, the output regulating variable accumulates
continuously, if the deviation persists, the regulating variable will increase continuously until deviation