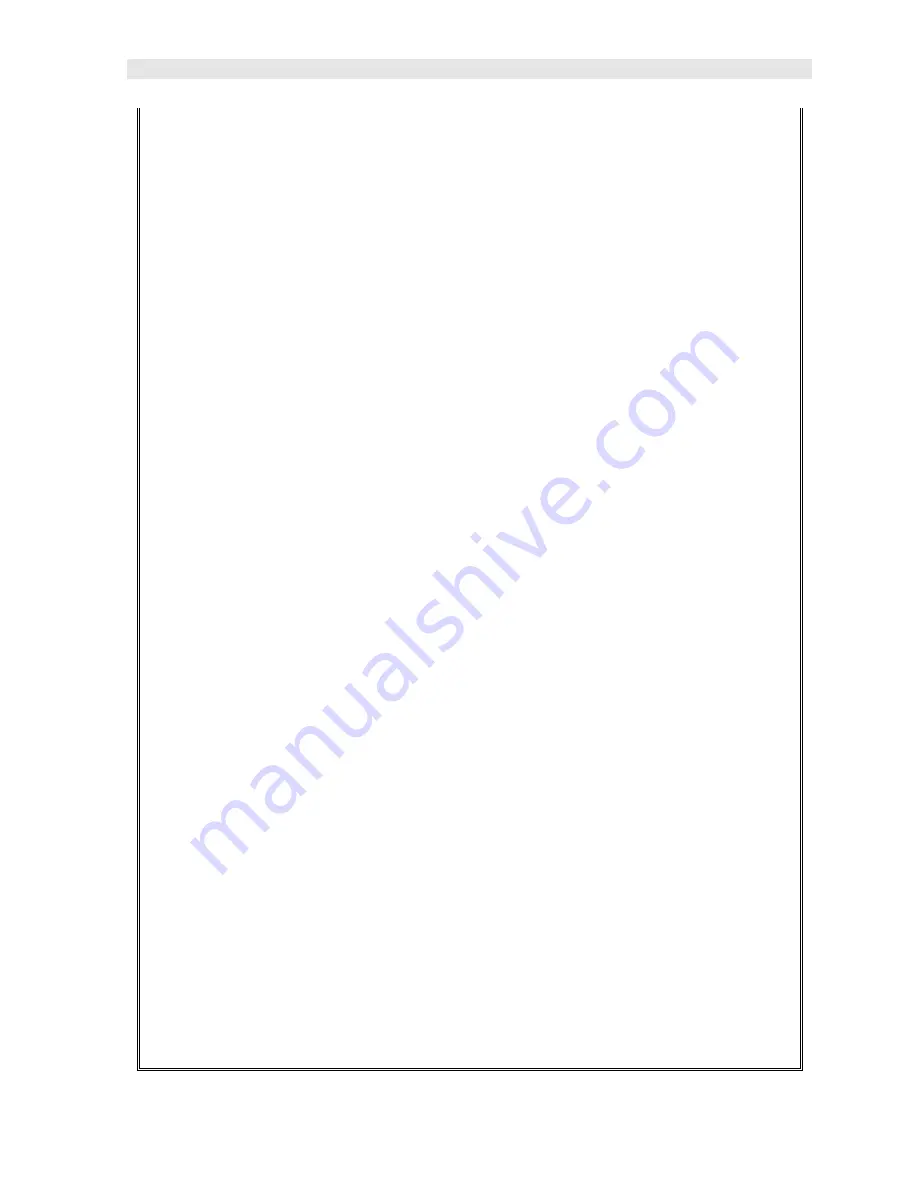
MAX II
Bolt Tension Monitor
105
working conditions.
Using the mechanical measuring device, measure and
record the Mechanical Length at Load 1 “L
M1
” for the current sample bolt.
6) Apply a drop of couplant to the bolt or transducer, and attach it to one end of
the bolt. Rotate the transducer clockwise and counter clockwise applying a
small amount of pressure to eliminate any excess couplant between the
transducer and bolt
.
Measure and record the Ultrasonic Length at Load 1
“L
U1
”for the current sample bolt.
7)
Increase the applied load to approximately 2/3 of the maximum load, which
is to be placed on the bolt under actual working conditions.
Using the
mechanical measuring device, measure and record the Mechanical Length
at Load 2 “L
M2
” for the current sample bolt.
8) Apply a drop of couplant to the bolt or transducer, and attach it to one end of
the bolt. Rotate the transducer clockwise and counter clockwise applying a
small amount of pressure to eliminate any excess couplant between the
transducer and bolt
.
Measure and record the Ultrasonic Length at Load 2
“L
U2
”for the current sample bolt.
9)
Increase the applied load to approximately the maximum load, which is to be
placed on the bolt under actual working conditions.
Using the mechanical
measuring device, measure and record the Mechanical Length at Load 3
“L
M3
” for the current sample bolt.
10) Apply a drop of couplant to the bolt or transducer, and attach it to one end
of the bolt. Rotate the transducer clockwise and counter clockwise applying
a small amount of pressure to eliminate any excess couplant between the
transducer and bolt
.
Measure and record the Ultrasonic Length at Load 3
“L
U3
” (Maximum) for the current sample bolt.
11)
Repeat Steps
5 – 10
for the remaining bolts.
Summary of Contents for MAX II
Page 2: ......
Page 7: ......
Page 8: ......
Page 54: ...Dakota Ultrasonics 46 Figure 6 Reflection in a bending bolt ...
Page 215: ......