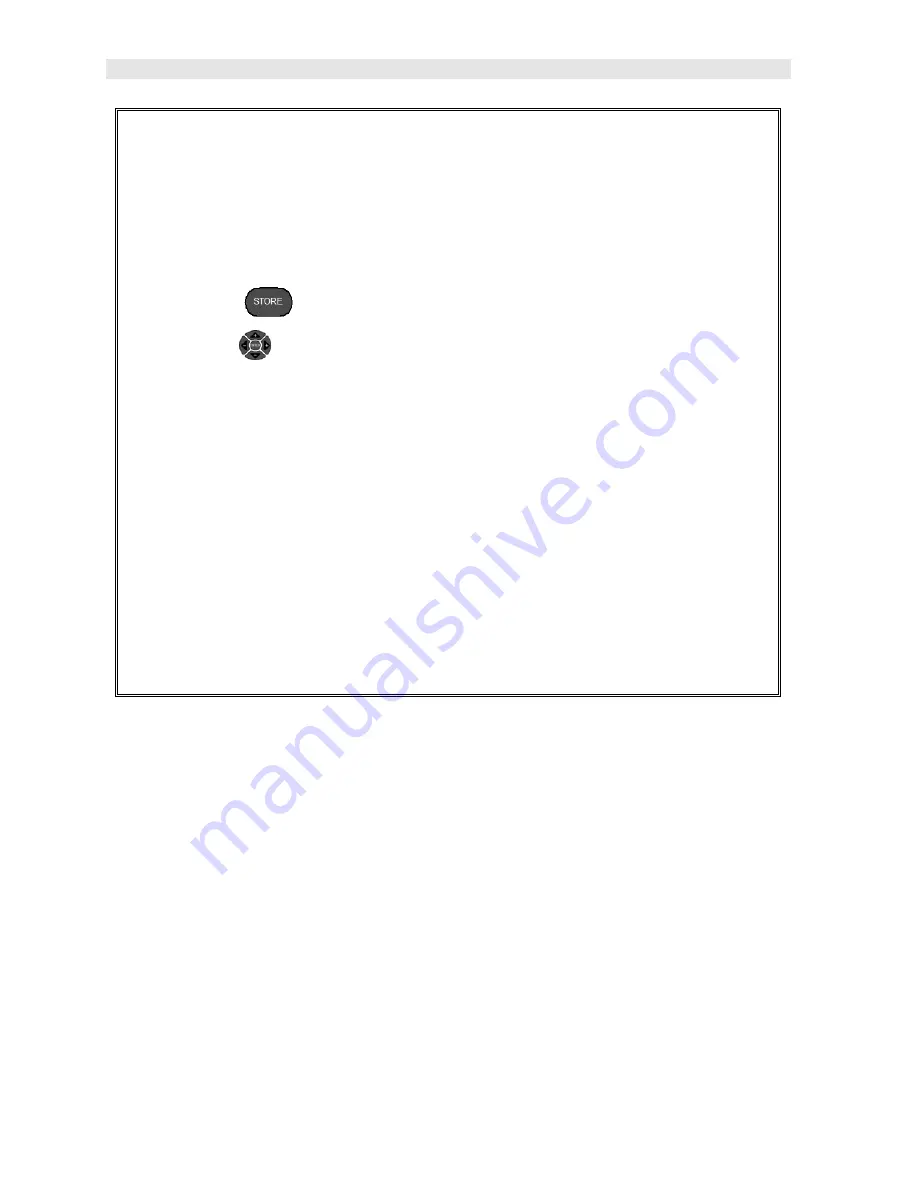
Dakota Ultrasonics
62
29) Press the
OK
key to return to the
MATL
menu, or
ESC
to cancel entering
the
VELOCITY
.
30) Repeat steps
32 – 37
to enter the
TEMP COEF
.
31) Repeat steps
32 – 37
to enter the
STRESS FACTOR to 1.000”
.
32) Press the
key to display the
CAL DATA
group.
33) Press the
UP, DOWN, LEFT, & RIGHT
arrow keys using the left button
wheel to scroll the target cell cursor to the desired storage location.
Note:
The first
column A
must be used to store reference lengths.
34) Press the
ENTER
key to save the current reading in the highlighted cell
location.
35) Abort the
Grid View Box
by pressing the
MEAS
key at any time.
36) The zero calibration is complete and documented.
37) Finally, press the
MEAS
key to return to the measurement screen, set up a
new bolt group, and begin taking measurements.
8.5 Using a Standard Bolt
Using any fastener that provides a good ultrasonic echo with both ends ground and
polished can make a simple and effective calibration standard. The primary objective
is to verify a zero value prior to measuring to avoid measurement errors if the
MAX II
,
transducer, or cable is replaced. While this sounds like an economic way to go, the
user must keep in mind that certified calibration standards are usually inclusive of an
ultrasonic length, velocity, and temperature coefficient that is certified according to a
specific set of standards. The following procedures outline how to use a standard
bolt as follows:
Now that a group has been created to store our probe zero data, the material type of
the standard zero/cal bolt must be selected. This will load the appropriate values for
velocity and the temperature coefficient into memory.
Summary of Contents for MAX II
Page 2: ......
Page 7: ......
Page 8: ......
Page 54: ...Dakota Ultrasonics 46 Figure 6 Reflection in a bending bolt ...
Page 215: ......