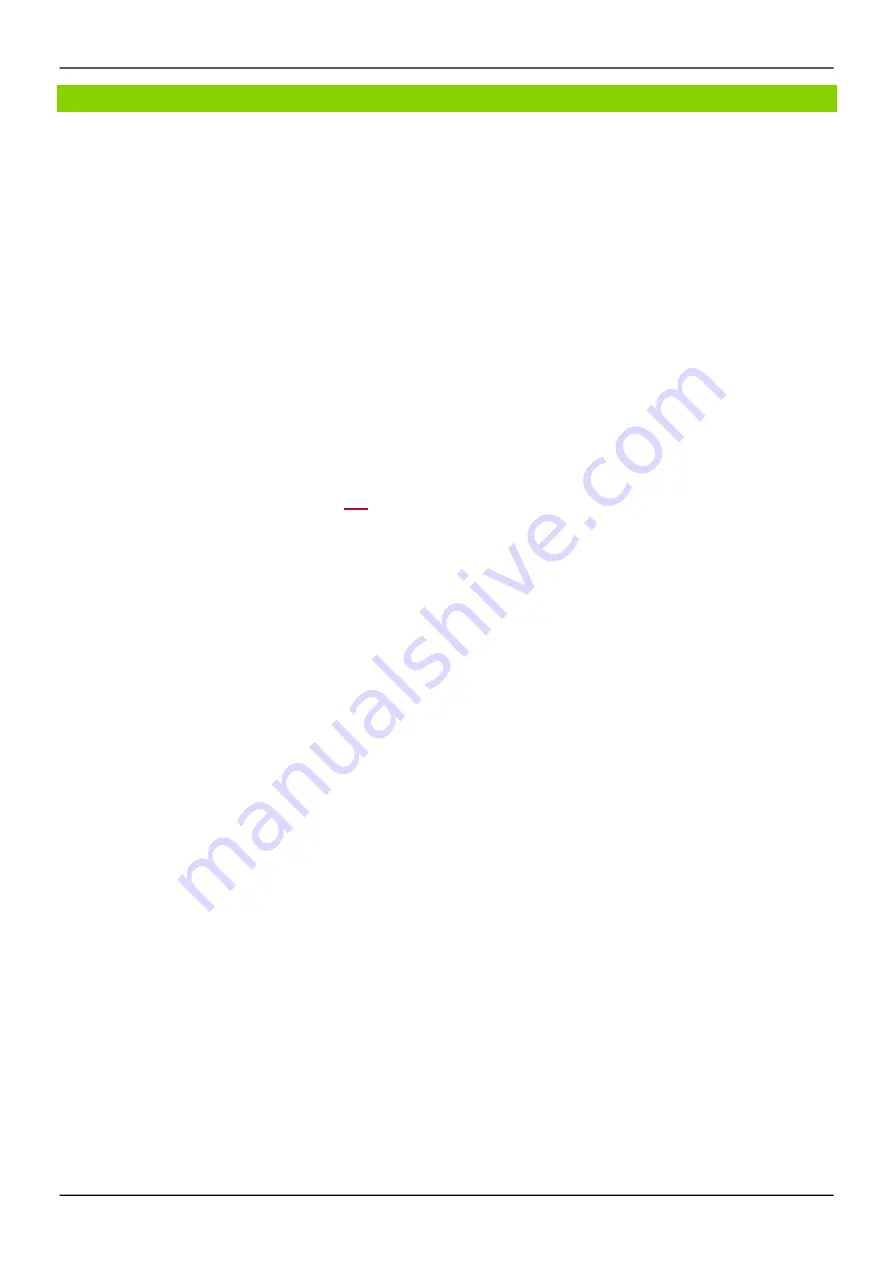
Configuration Mode (ConF)
208
"Manual - Automatic" Operation with PID
This function com bines the PID regulator, the preset s peeds and a m anual reference. Depending on the state
of the logic input, the s peed reference is given by the pres et s peeds or by a m anual reference input via the
PID function.
Manual reference
[Manual reference]
(
PIM
)
:
•
Analog inputs AI1 to AI3
•
Puls e input
Predictive speed reference
[Speed ref. assign.]
(
FPI
)
:
•
[AI1]
(AI1)
: Analog input
•
[AI2]
(AI2)
: Analog input
•
[AI3]
(AI3)
: Analog input
•
[RP]
(PI)
: Puls e input
•
[HMI]
(LCC)
:
Graphic dis play term inal or rem ote dis play term inal
•
[Modbus]
(Mdb)
: Integrated Modbus
•
[CANopen]
(CAn)
: Integrated CANopen®
•
[Com. card]
(nEt)
: Com m unication card (if ins erted)
Setting up the PID regulator
1. Configuration in PID mode.
See the diagram on page
206
.
2. Perform a test in factory settings mode.
To optim ize the drive, adjus t
[PID prop. gain]
(rPG)
or
[PID integral gain]
(rIG)
gradually and
independently, and obs erve the effect on the PID feedback in relation to the reference.
3. If the factory settings are unstable or the reference is incorrect.
•
Perform a tes t with a s peed reference in Manual m ode (without PID regulator) and with the drive on load
for the s peed range of the s ys tem :
- In s teady s tate, the s peed m ust be stable and comply with the reference, and the PID feedback signal
m us t be s table.
- In trans ient s tate, the s peed m us t follow the ram p and s tabilize quickly, and the PID feedback m us t
follow the s peed. If this is not the cas e, s ee the settings for the drive and/or s ensor s ignal and wiring.
•
Switch to PID m ode.
•
Set
[Dec ramp adapt.]
(brA)
to
[No]
(nO)
(no auto-adaptation of the ram p).
•
Set
[PID ramp]
(PrP)
to the m inim um perm itted by the m echanism without triggering an
[Overbraking]
(ObF)
.
•
Set the integral gain
[PID integral gain]
(rIG)
to m inim um.
•
Leave the derivative gain
[PID derivative gain]
(rdG)
at 0.
•
Obs erve the PID feedback and the reference.
•
Switch the drive ON/OFF a num ber of tim es or vary the load or reference rapidly a num ber of tim es .
•
Set the proportional gain
[PID prop. gain]
(rPG)
in order to as certain the com prom is e between res pons e
tim e and s tability in trans ient phas es (s light overs hoot and 1 to 2 os cillations before s tabilizing).
•
If the reference varies from the pres et value in s teady s tate, gradually increas e the integral gain
[PID integral gain]
(rIG)
, reduce the proportional gain
[PID prop. gain]
(rPG)
in the event of ins tability
(pum p applications), find a com prom ise between response tim e and s tatic precision (s ee diagram).
•
Las tly, the derivative gain m ay perm it the overs hoot to be reduced and the res ponse tim e to be im proved,
although this will be m ore difficult to obtain a com prom ise in term s of s tability, as it depends on 3 gains .
•
Perform in-production tes ts over the whole reference range.
Parameters described in this page can be accessed by:
DRI- > CONF > FULL > FUN- > PID-
Summary of Contents for ER24 Series
Page 6: ...6 Table of Contents ...
Page 14: ...16 ...
Page 34: ...Overview 36 ...
Page 40: ...42 ...
Page 74: ...Monitoring Mode MOn 76 ...
Page 241: ......
Page 278: ...Configuration Mode ConF 278 Access Level See Access Level LAC page 280 ...
Page 294: ...Interface ItF 294 ...
Page 298: ...298 Open Save as trA ...
Page 302: ...Multipoint Screen 302 ...
Page 304: ...304 ...
Page 306: ...Maintenance 306 ...
Page 316: ...Diagnostics and Troubleshooting 316 ...
Page 318: ...318 ...
Page 340: ...Index of Parameter Codes 340 ...
Page 343: ......
Page 344: ...Index of Parameter Codes 342 ER24_Programming_Manual_EN_01 2017 ...