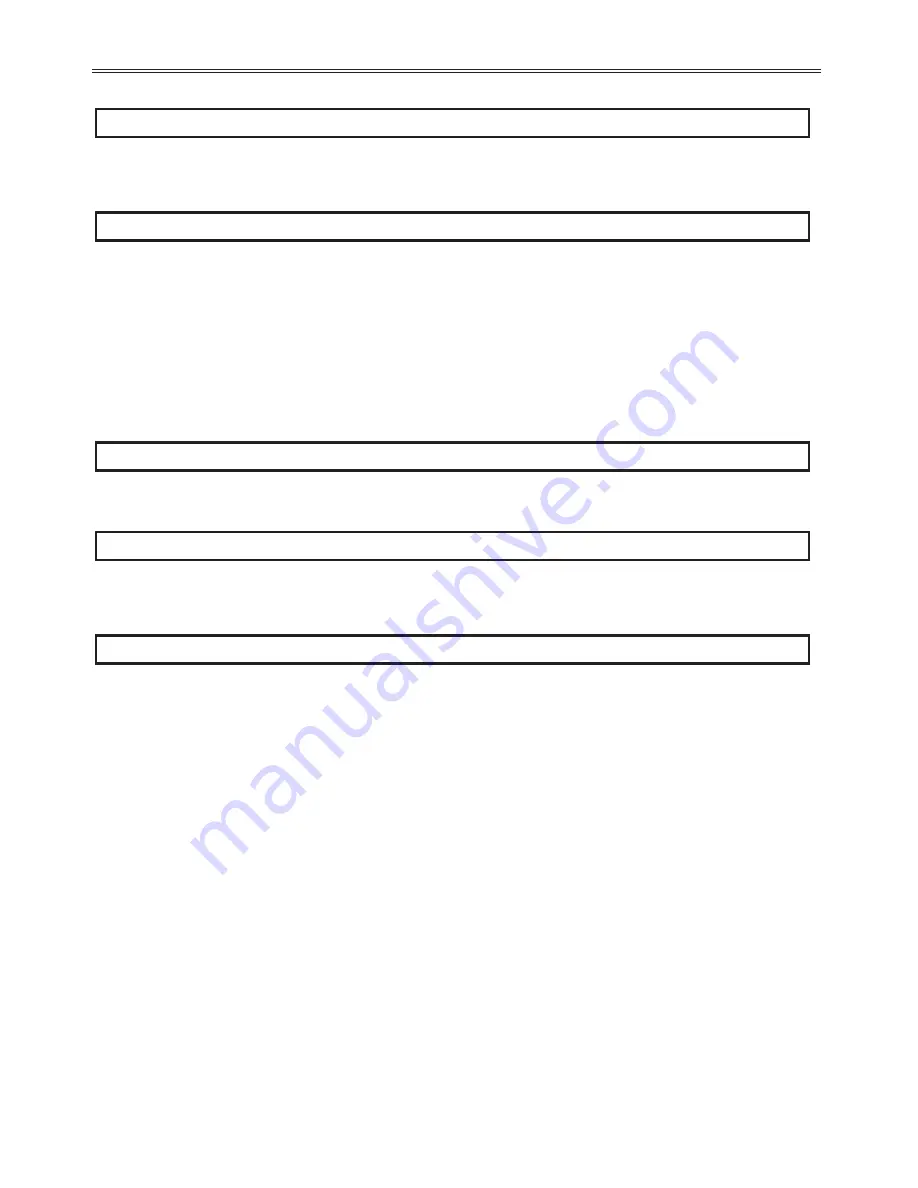
Jump Code
4.6
Jump Code
At the beginning of each parameter group, there is a Jump Code parameter. By changing the value of this parameter and pressing
[ENTER], you can jump directly to any parameter within that group.
Restoring Factory Parameter Settings
4.7
Restoring Factory Parameter Settings
Go to the FUN group by pressing [MENU]. Scroll through to Miscellaneous Commands (FUN 22) and press [ENTER]. Now set to
"Factory Rst" and press [ENTER]. The display will return to "None" but the parameters will be reset to the factory defaults.
z
NOTE:
If a factory reset is performed, the following minimum parameters will need to be programmed so a F47 - "Stack Overtemp"
does not occur:
FUN05 - Rated RMS Voltage (set to specified equipment rating)
FUN03 - CT Ratio
I/O01 - 08 - Digital Inputs
I/O10 - 15 - Relay Outputs
z
NOTE: You must consult the wiring schematic for other digital inputs and relay output configuration.
Resetting a Fault
4.8
Resetting a Fault
To reset from a fault condition, press [RESET].
Emergency Overload Reset
4.9
Emergency Overload Reset
To perform an emergency overload reset, press [RESET] and [DOWN] pushbuttons together. This sets the motor thermal overload
content to "0".
LED Display
4.10
LED Display
The card mounted LED display can be used to access most of the parameters when the standard remote mounted display is not
connected. The LED parameter numbers (Pxx) are shown in the parameter table, see Chapter 5.
48
4 - KEYPAD OPERATION
Summary of Contents for RediStart EXEXMVRMX3 Series
Page 2: ......
Page 10: ......
Page 11: ...1 Introduction 1...
Page 17: ...2 Technical Specifications 7...
Page 27: ...3 Installation 17...
Page 48: ......
Page 49: ...4 Keypad Operation 39...
Page 59: ...5 Parameter Groups 49...
Page 67: ...6 Parameter Description 57...
Page 122: ...NOTES 112 6 PARAMETER DESCRIPTION...
Page 123: ...7 Theory of Operation 113...
Page 155: ...NOTES 145 7 THEORY OF OPERATION...
Page 156: ...146 7 THEORY OF OPERATION...
Page 157: ...8 Troubleshooting Maintenance 147...
Page 185: ...NOTES 175 8 TROUBLESHOOTING MAINTENANCE...
Page 186: ......
Page 187: ...Appendices 177...
Page 213: ...203 APPENDIX H 3 YEAR WARRANTY...
Page 221: ...Publication History Revision Date ECO 00 12 15 06 Initial Release...