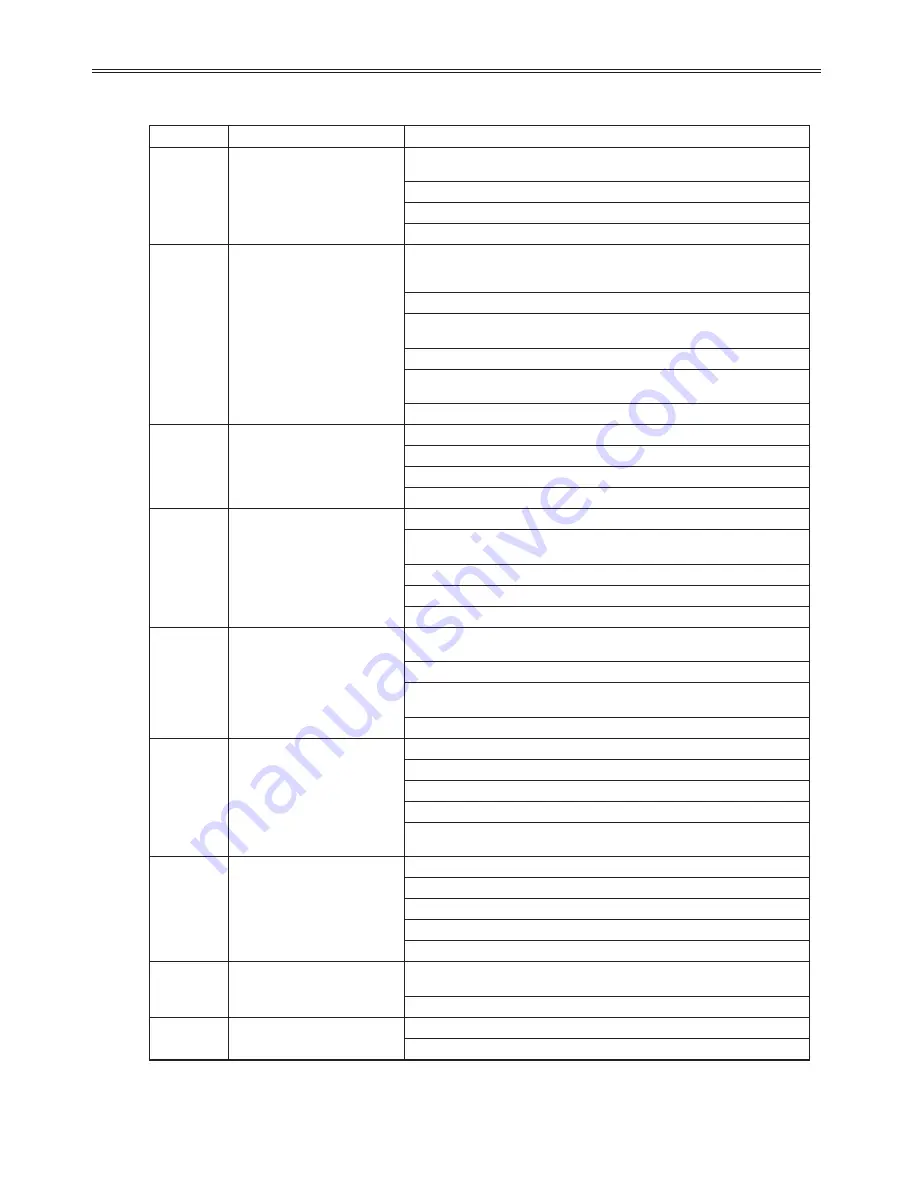
160
8 - TROUBLESHOOTING & MAINTENANCE
Fault Code
Description
Detailed Description of Fault / Possible Solutions
F47
Stack Protection Fault (stack
thermal overload)
The MX
3
electronic power stack OL protection has detected an overload
condition.
Check motor for jammed or overloaded condition.
Verify that the CT ratio (FUN 03) is correct.
Motor load exceeds power stack rating. Consult factory
F48
Bypass /2M Contactor Fault
A digital input has been programmed as a Bypass/2M Contactor Feedback input
and an incorrect bypass feedback has been detected for longer than the Bypass
Confirm time parameter setting (I/O 25).
Verify that the bypass/2M contactor coil and feedback wiring is correct.
Verify that the relay connected to the bypass/2M contactor(s) is programmed as
the UTS function (I/O 10 - I/O 15).
Verify that the bypass/2M contactor power supply is present (J4).
Verify that the appropriate Digital Input Configuration parameter (I/O 01 -08) has
been programmed correctly.
Verify that the bypass contactor(s) are not damaged or faulty.
F49
Inline Contactor Fault
The in-line contactor did not close.
Check wiring to coil of contactor.
Check feedback wiring from auxiliary contactor to digital input (I/O 01 - 08).
Check in-line fault delay (I/O 24).
F50
Control Power Low
Low control power (below 90V) has been detected while running.
Verify that the control power input level is correct, especially during starting
when there may be significant line voltage drop.
Check control power transformer tap setting (if available).
Check control power transformer fuses (if present).
Check wiring between control power source and starter.
F51
Current Sensor Offset Error
Indicates that the MX
3
control card self-diagnostics have detected a problem with
one or more of the current sensor inputs.
Verify that the motor FLA (QST 01) and CT ratio (FUN 03) are correct.
Verify that no actual current is flowing through any of the starter’s CTs when the
starter is not running.
Consult factory if fault persists.
F53
Tachometer Signal Loss
No tachometer signal detected during start or run.
Verify tachometer wiring and level of signal.
Verify tachometer Full Speed Voltage (FUN 13) setting.
Extend Tachometer Loss Time (FUN 14) to allow time for motor to start turning.
Increase Initial Current to make sure motor starts turning immediately after the
start command is given.
F54
BIST Fault
The Build In Self Test was cancelled.
The disconnect (if present) was closed during standard BIST testing.
Line voltage and/or phase current was detected during standard BIST testing.
During powered BIST testing the disconnect was opened during testing.
During powered BIST testing line voltage was lost during testing.
F55
BIST CT Fault
During powered BIST testing the starter detected that one or more CTs are located
on the incorrect phases or one or more CT's polarities are reversed.
Verify CT wiring, positioning and direction.
F56
RTD Open or Shorted
An open or shorted RTD was detected.
Verify the condition and wiring of the RTD.
Summary of Contents for RediStart EXEXMVRMX3 Series
Page 2: ......
Page 10: ......
Page 11: ...1 Introduction 1...
Page 17: ...2 Technical Specifications 7...
Page 27: ...3 Installation 17...
Page 48: ......
Page 49: ...4 Keypad Operation 39...
Page 59: ...5 Parameter Groups 49...
Page 67: ...6 Parameter Description 57...
Page 122: ...NOTES 112 6 PARAMETER DESCRIPTION...
Page 123: ...7 Theory of Operation 113...
Page 155: ...NOTES 145 7 THEORY OF OPERATION...
Page 156: ...146 7 THEORY OF OPERATION...
Page 157: ...8 Troubleshooting Maintenance 147...
Page 185: ...NOTES 175 8 TROUBLESHOOTING MAINTENANCE...
Page 186: ......
Page 187: ...Appendices 177...
Page 213: ...203 APPENDIX H 3 YEAR WARRANTY...
Page 221: ...Publication History Revision Date ECO 00 12 15 06 Initial Release...