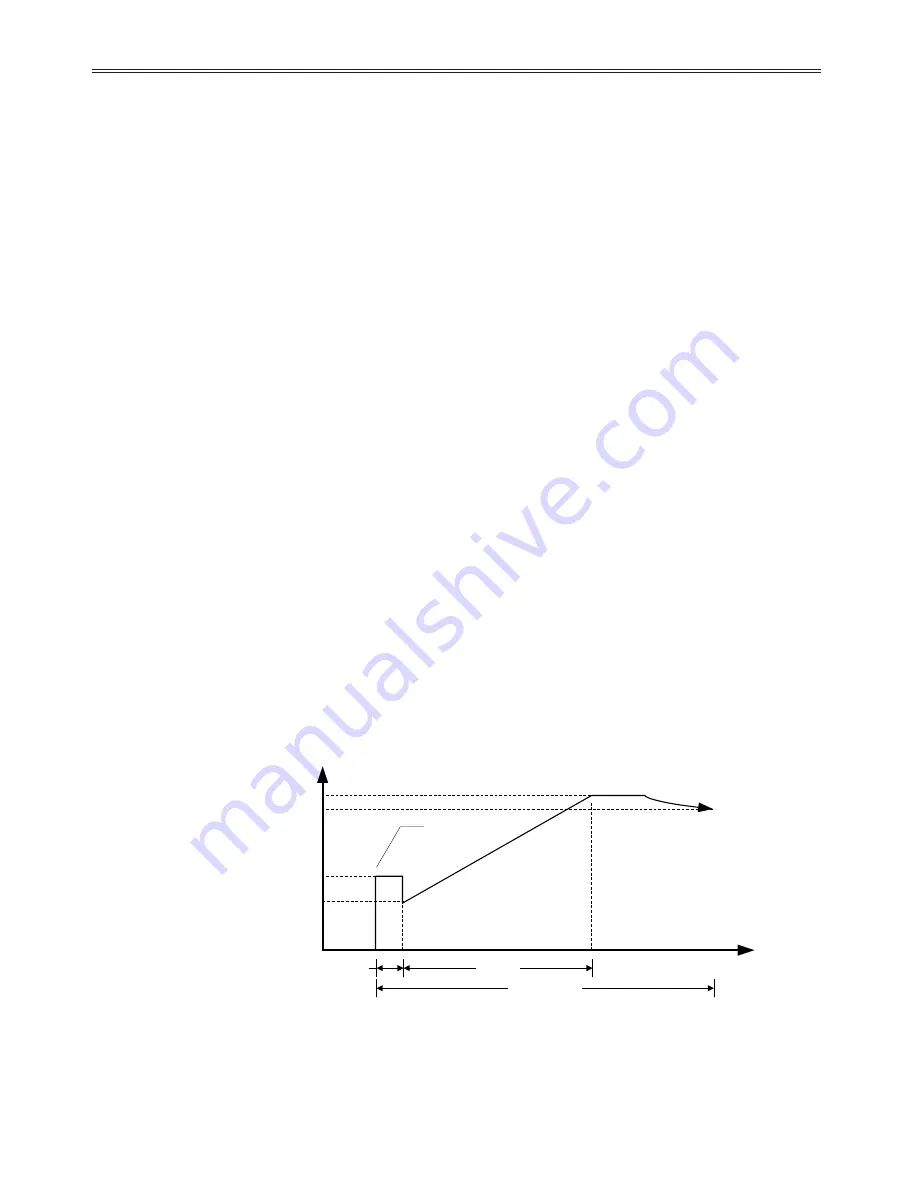
124
7 - THEORY OF OPERATION
Ramp Time
The ramp time is the time it takes for the current to go from the initial current to the maximum current. To
make the motor accelerate faster, decrease the ramp time. To make the motor accelerate slower, increase the
ramp time.
If the ramp time expires before the motor reaches full speed, the starter maintains the maximum current level
until either the motor reaches full speed, the Up to Speed time expires, or the motor thermal overload trips.
z
NOTE:
Setting the ramp time to a specific value does not necessarily mean that the motor will take this
time to accelerate to full speed. The motor and load may achieve full speed before the ramp time expires if
the application does not require the set ramp time and maximum current to reach full speed. Alternatively, the
motor and load may take longer than the set ramp time to achieve full speed.
7.3.2
Programming A Kick Current
General
The kick current sets a constant current level that is applied to the motor before the ramp begins. The kick
current is only useful on motor loads that are hard to get rotating but then are much easier to move once they
are rotating. An example of a load that is hard to get rotating is a ball mill. The ball mill requires a high
torque to get it to rotate the first quarter turn (90°). Once the ball mill is past 90° of rotation, the material
inside begins tumbling and it is easier to turn.
Kick Level
The kick current parameter is usually set to a low value and then the kick time is adjusted to get the motor
rotating. If the kick time is set to more than 2.0 seconds without the motor rotating, increase the kick current
by 100% and re-adjust the kick time.
Kick Time
The kick time adjustment should begin at 0.5 seconds and be adjusted by 0.1 or 0.2 second intervals until the
motor begins rotating. If the kick time is adjusted above 2.0 seconds without the motor rotating, start over
with a higher kick current setting.
7.3.3
TruTorque Acceleration Control Settings and Times
General
TruTorque acceleration control is a closed loop torque based control. The primary purpose of TruTorque
acceleration control is to smoothly start motors and to reduce the torque surge that can occur as an AC
induction motor comes up to speed. This torque surge can be a problem in applications such as pumps and
belt driven systems. In pumping applications, this torque surge can result in a pressure peak as the motor
comes up to speed. In most situations this small pressure peak is not a problem. However in selected cases,
even a small pressure rise can be highly undesirable. In belt driven applications, TruTorque can prevent the
slipping of belts as the motor reaches full speed.
TruTorque acceleration control can be very useful for a variety of applications. However it is best used to
start centrifugal pumps, fans, and other variable torque applications. TruTorque generally should not be used
in applications where the starting load varies greatly during the start such as with a reciprocating compressor,
where the starting load is very low, or where the starting load varies greatly from one start to another.
TruTorque control is not recommended for the starting of AC synchronous motors.
Motor
Torque
Time
Kick Time
Ramp Time
Up To Speed Timer
Motor Running
Torque
Initial Torque
Optional Kick
Current
Max Torque
Start command
Figure 33: TruTorque Ramp
Summary of Contents for RediStart EXEXMVRMX3 Series
Page 2: ......
Page 10: ......
Page 11: ...1 Introduction 1...
Page 17: ...2 Technical Specifications 7...
Page 27: ...3 Installation 17...
Page 48: ......
Page 49: ...4 Keypad Operation 39...
Page 59: ...5 Parameter Groups 49...
Page 67: ...6 Parameter Description 57...
Page 122: ...NOTES 112 6 PARAMETER DESCRIPTION...
Page 123: ...7 Theory of Operation 113...
Page 155: ...NOTES 145 7 THEORY OF OPERATION...
Page 156: ...146 7 THEORY OF OPERATION...
Page 157: ...8 Troubleshooting Maintenance 147...
Page 185: ...NOTES 175 8 TROUBLESHOOTING MAINTENANCE...
Page 186: ......
Page 187: ...Appendices 177...
Page 213: ...203 APPENDIX H 3 YEAR WARRANTY...
Page 221: ...Publication History Revision Date ECO 00 12 15 06 Initial Release...