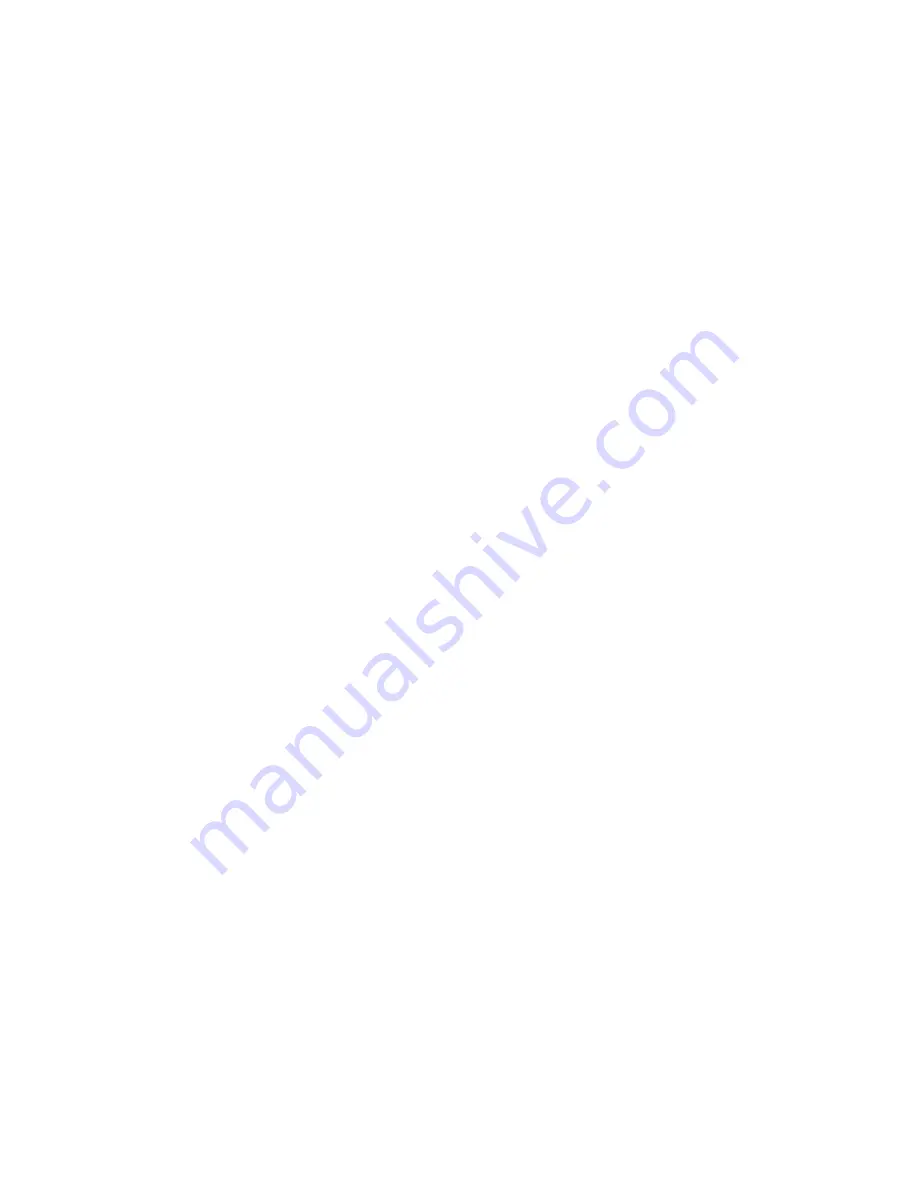
Setup Parameters
MedWeld 4000 Operator’s Guide
Modified: 9/17/08
5 - 21
M-032116 Programs #T03300, #T02300 and #T02400
Inverter Operating
Parameters
The following setup parameters apply only to programs such as T023xx.
TRANSFORMER TYPE:
(NONE) (TR75X)
(TR76X)
This parameter tells the weld processor the type of welding
transformer being used in the application. The software will check
the duty cycle for each welding transformer and use this to alert the
operator if the transformer is in danger of saturation from exceeding
the duty cycle.
FIRING MODE:
(PRI CURRENT)
(PRI VOLTAGE)
•
Primary Current: selects the constant current (ACC) firing mode for
welds in nnnn0 Amps.
•
Primary Voltage: selects the constant primary voltage (AVC) mode
for welding in % of current available or %I.
This parameter controls how the inverter will supply weld current.
It also sets how fault conditions will be reported if the desired
amount of energy could not be delivered to the weld.
NOMINAL LINE VOLTAGE: nnn
(0 - 999)
Nominal line voltage is used by the welding control to set the
expected facility power when installed at a location. This parameter
(along with the line voltage measurement) is used by the welding
control to establish a reference point for determining the
compensation required for line voltage fluctuations when welding
in the %I firing mode. The value of the nominal line voltage also
helps to normalize voltage based calculations for more advanced
functions such as C-factor.
This value should be set based on the average voltage of the
welding bus.
EXAMPLE:
If the welding bus at the facility is 480 volts, the value of the nominal line
voltage should be set to 480. To be more accurate, a line voltage
measurement should be taken with a multi-meter during normal working
hours or during production. On weekends and during down time a
typicaly welding bus can be significantly higher than during production
and an accurate reading gives the welding control more accurate
information for calculations.
MAXIMUM PRIMARY CURRENT: NNNN (0 - 9999)
MAXIMUM SECONDARY CURRENT:NNNNN (0 - 99999)
These parameters set the range of acceptable values used by the
MFDC Inverter to determine the amount of weld current to provide,
based on the selected firing mode.
Содержание MedWeld 4000
Страница 77: ...9 cdQ Y W dXU UTGU T _TYVYUT UTGU T UbQd_bµc 7eYTU b_WbQ c D D Q T D This page is intentionally left blank ...
Страница 153: ...Weld Schedules 4 54 Modified 9 17 08 MedWeld 4000 Operator s Guide M 032116 Programs T03300 T02300 and T02400 ...
Страница 255: ...Hardware Troubleshooting 9 10 Modified 9 17 08 MedWeld 4000 Operator s Guide M 032116 Programs T03300 T02300 and T02400 ...
Страница 257: ...Application Note Current Compensation 2 ML 010041 Application Note Current Compensation ...
Страница 261: ...Application Note Cascade Welding 4 ML 010041 Application Note Cascade Firing ...