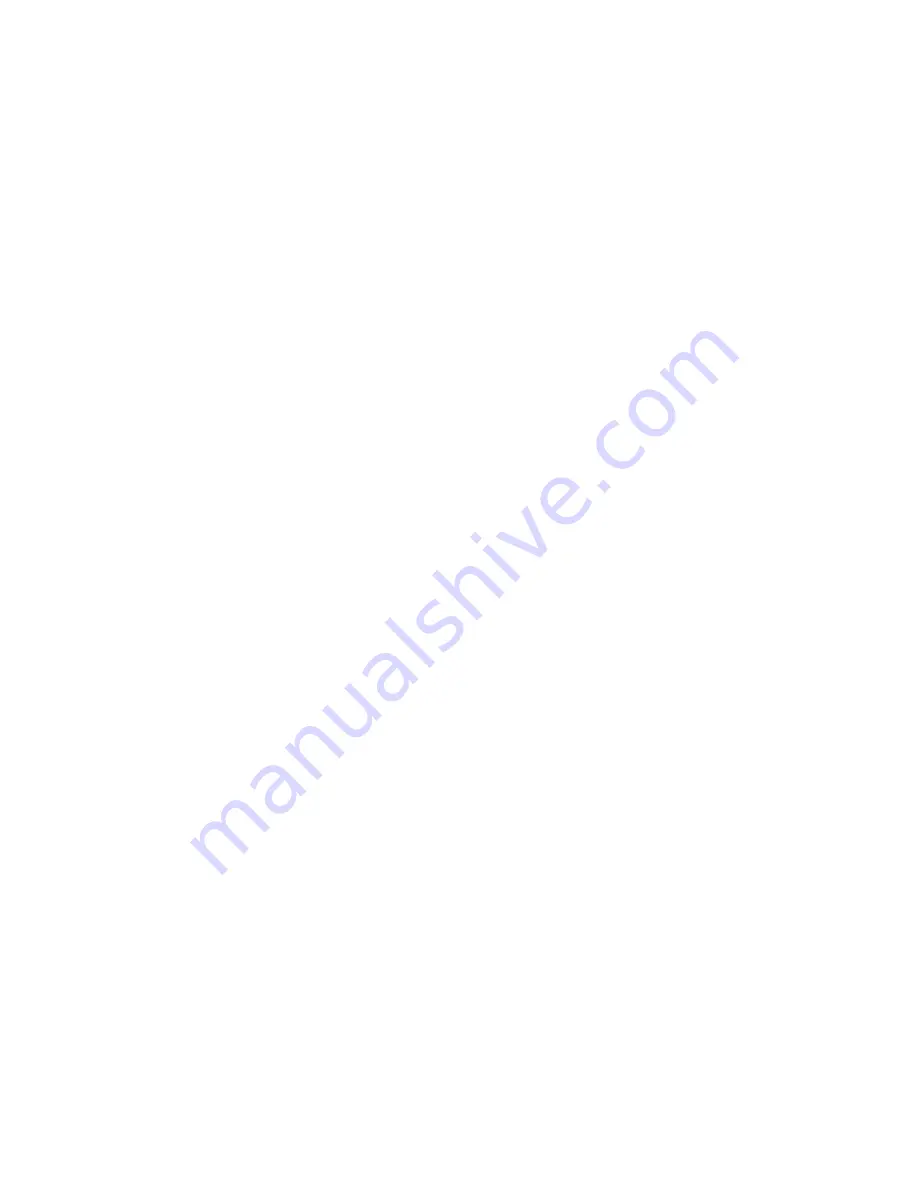
Communications and I/O
3 - 2
Modified: 9/17/08
MedWeld 4000 Operator’s Guide
M-032116 Programs #T03300, #T02300 and #T02400
Local Inputs
The Control Stop input is 24 VDC. It can be either internally- or
externally-powered. Refer to “Providing Local I/O” on page 2-5 for
more information.
CONTROL STOP Input
CSTP
If this is dropped during a schedule, when this input is de-activated,
the control aborts the present schedule and will not initiate another
schedule until the input becomes activated. The isolation contactor
also drops out (to disable weld current). A CONTROL STOP fault
condition is generated. See page 5-2 for more details.
Attempting to initiate a weld when this input is inactive will
generate a CONTROL STOP fault.
ISOLATION CONTACTOR Input
IC
This is an input to the weld control enclosure, showing whether the
isolation contactor is open or closed. It is normally closed.
If this contact fails to change state when the control attempts to pass
current, the control will generate an ISO-CNTR OFF WHEN
NEEDED fault condition and trip the circuit breaker. Refer to page
5-5 for more information about this fault.
If this contact fails to return to its original state after the contactor is
turned off (including the Isolation Contactor Delay), the control
will generate an ISO-CNTR ERR BKR TRIPPED fault condition,
and trip the circuit breaker.
THERMAL SWITCH Input
TS2
This input to the weld processor indicates that the SCR module has
reached an over-temperature condition.
If this input is not active when the control receives the signal to
initiate a weld, the weld processor completes the schedule in No
Weld and generates a SYSTEM COOLING fault. See page 5-6 for
more details.
INVERTER READY TO WELD
(IRTW)
(Progams T02300 and T02400 only):
This is an input to the weld
processor from the inverter. It indicates that the following
conditions are true at the inverter, and the inverter is ready to
receive a firing signal from the weld sequence:
•
The inverter thermal switches indicate that cooling water is
present.
•
The isolation contactor is ready to be pulled in (to provide weld
current).
•
No fault conditions exist at the inverter.
Содержание MedWeld 4000
Страница 77: ...9 cdQ Y W dXU UTGU T _TYVYUT UTGU T UbQd_bµc 7eYTU b_WbQ c D D Q T D This page is intentionally left blank ...
Страница 153: ...Weld Schedules 4 54 Modified 9 17 08 MedWeld 4000 Operator s Guide M 032116 Programs T03300 T02300 and T02400 ...
Страница 255: ...Hardware Troubleshooting 9 10 Modified 9 17 08 MedWeld 4000 Operator s Guide M 032116 Programs T03300 T02300 and T02400 ...
Страница 257: ...Application Note Current Compensation 2 ML 010041 Application Note Current Compensation ...
Страница 261: ...Application Note Cascade Welding 4 ML 010041 Application Note Cascade Firing ...