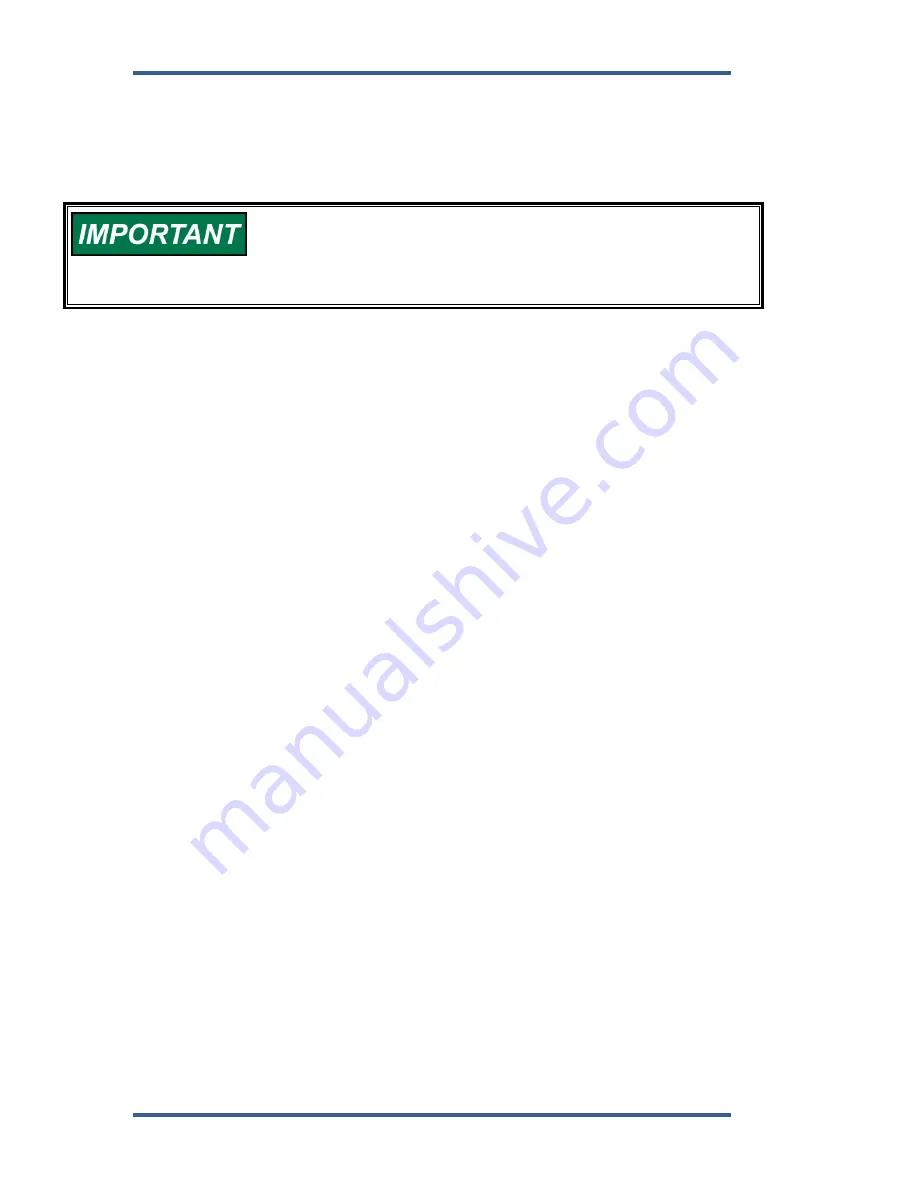
2301E Digital Control
Manual 26641
24
Woodward
Power wiring for using the PWM output function is required to be local and
dedicated, only located on the engine skid or relatively close to the control and
PWM load. The power connected to control 48(+) and 49(
–) terminals must also
be used for the relay driver external Vdc source connected at terminals 42(+) and
43(
–). In addition, the PWM load device power must also be from the same
source as the power connected to control terminals 48(+) and 49(
–-).
The PWM functionality is limited to use on skid applications. When
PWM drivers are used, the 2301E must be located on the same power
bus as the driven circuitry. The 2301E and the device being driven
need to be co-located on the same engine. In addition, the Power bus
input for the 2301E must be used to power the DO signals.
4
–20 mA Output (Terminals 16–17)
The analog output can be configured several different ways depending on the
application needs and is typically used to drive an external meter. The output
current is 4 to 20 mA. This current signal is supplied via shielded wires to
terminals 16(+) and 17(
–). The shield is connected to terminal 18 (chassis). Note
that these terminals must be isolated from ground. The Output can be software
configured to one of several control parameters. These parameters include:
Engine Speed
Engine Speed Reference
Fuel Demand
Generator Output
System Load Percent
Synchronizer Input
Analog Input #2
Speed Setting Bias Signal
Base Load Reference
Misfire RPM per Sec
2
The Analog Output is factory set for 4 to 20 mA, representing the engine speed.
Default range is 0 to 100%. Software settings must be changed if an output of 0
to 20 mA is needed. Use shielded twisted-pair wires. For electrically isolated
devices such as 4 to 20 mA analog meters, the shield should be grounded at the
control end of the cable. For input to other devices, use the recommendation of
the device manufacturer.
Communication Ports
The control’s two serial communication ports are used to configure and service
the unit. These ports are on a common return and are isolated ports.
The RS-232 serial communication service port communicates using either the
2301E Toolkit Service Tool or the Control Assistant software. Refer to Figure 2-3
for plant wiring information.
The RS-422 serial communication port communicates using a Modbus RTU
protocol, functioning as a Modbus Slave device, via a RS-422 driver. The 2301E
can be fully operated and many values monitored via Modbus communications.
Alternatively Modbus communications can be used to interface with a PLC or
plant DCS. Refer to Figure 2-4 for plant wiring information.
Содержание 2301E
Страница 14: ...2301E Digital Control Manual 26641 4 Woodward Figure 1 1a 2301E Outline Drawing Ordinary Locations...
Страница 15: ...Manual 26641 2301E Digital Control Woodward 5 Figure 1 1b 2301E Outline Drawing Hazardous Locations...
Страница 16: ...2301E Digital Control Manual 26641 6 Woodward Figure 1 2a 2301E Control Wiring Diagram sheet 1...
Страница 17: ...Manual 26641 2301E Digital Control Woodward 7 Figure 1 2b 2301E Control Wiring Diagram sheet 2...
Страница 18: ...2301E Digital Control Manual 26641 8 Woodward Figure 1 2c 2301E Control Wiring Diagram notes...
Страница 80: ...2301E Digital Control Manual 26641 70 Woodward This screen shows an example of the Final Settings...
Страница 100: ...2301E Digital Control Manual 26641 90 Woodward Figure 4 5 Typical Transient Response Curves...
Страница 181: ...Manual 26641 2301E Digital Control Woodward 171 Declarations...