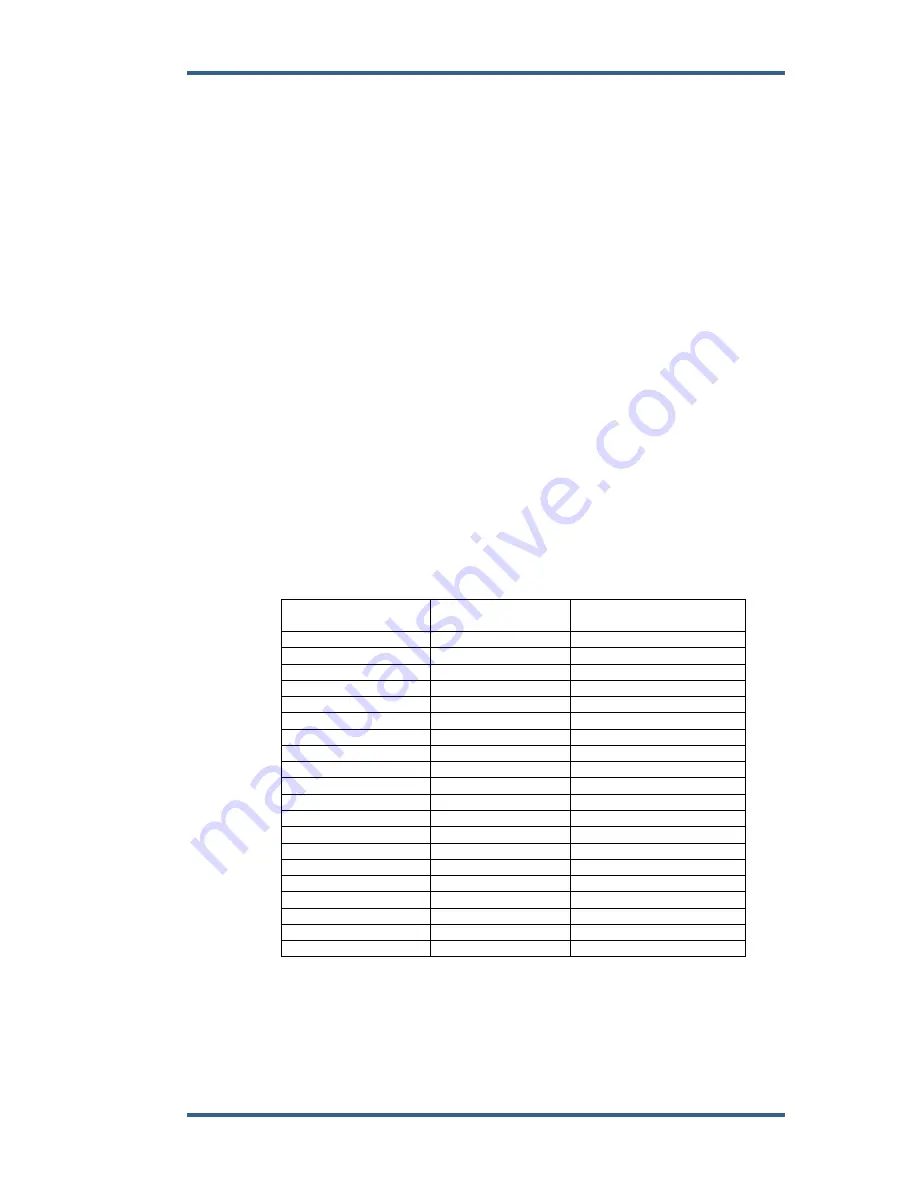
Manual 26641
2301E Digital Control
Woodward
97
c.
Load the engine with as many load points as are practical. At each load
point, Gain A may need to be varied to maintain engine stability. Do not
change Reset or Actuator Compensation after the first setting in step b.
Should it be necessary to change these settings to obtain good control,
repeat all previous steps until only Gain is changed at each load step.
At each load point, record the Fuel Demand % that is displayed in
A**DISPLAY MENU**. Also record the engine load (KW) and Gain A at
each point. If KW percent is selected for the X axis of the curve, the
ratio of KW to Rated KW times 100 will be used as the load percent
value. The actuator bump feature can be used to make small fuel
changes about the load point to verify stability.
The table below aids in collecting the data for the Gain Plot. When
entering the values into the control, the software will not allow
overlapping the breakpoint values (that is, Breakpoint A must be less
than breakpoint B, which must be less than breakpoint C, etc).
Gain settings reflect the sensitivity of the engine load to fuel demand as
shown in Figure 4-8. Flat portions of the engine plot will require
relatively small values of gain, steep portions of the plot will require
larger gain numbers (actuator has to move a lot to pickup small amount
of load).
d.
Create a plot of the system by plotting PID GAIN as a function of load.
A typical result is shown in Figure 4-8.
The following table may help in the construction of the plot. Use as
many load steps as possible, it is not necessary to use all 20 points
given below.
Load/RPM Point
Gain (for good
control)
Actuator or kW Output or
Speed
Load/RPM Point 1
Load/RPM Point 2
Load/RPM Point 3
Load/RPM Point 4
Load/RPM Point 5
Load/RPM Point 6
Load/RPM Point 7
Load/RPM Point 8
Load/RPM Point 9
Load/RPM Point 10
Load/RPM Point 11
Load/RPM Point 12
Load/RPM Point 13
Load/RPM Point 14
Load/RPM Point 15
Load/RPM Point 16
Load/RPM Point 17
Load/RPM Point 18
Load/RPM Point 19
Load/RPM Point 20
2. Set Gain A to the value recorded at point 1b. This should give good control at
no load.
3. Use the plot of the engine to determine the linearity of the fuel system. This
curve should be linearized between inflection points as shown in Figure 4-8.
4. Set the Gain A Breakpoint for the actuator output at or slightly below the load
value at the min load point. Set the GAIN value at breakpoint A.
Содержание 2301E
Страница 14: ...2301E Digital Control Manual 26641 4 Woodward Figure 1 1a 2301E Outline Drawing Ordinary Locations...
Страница 15: ...Manual 26641 2301E Digital Control Woodward 5 Figure 1 1b 2301E Outline Drawing Hazardous Locations...
Страница 16: ...2301E Digital Control Manual 26641 6 Woodward Figure 1 2a 2301E Control Wiring Diagram sheet 1...
Страница 17: ...Manual 26641 2301E Digital Control Woodward 7 Figure 1 2b 2301E Control Wiring Diagram sheet 2...
Страница 18: ...2301E Digital Control Manual 26641 8 Woodward Figure 1 2c 2301E Control Wiring Diagram notes...
Страница 80: ...2301E Digital Control Manual 26641 70 Woodward This screen shows an example of the Final Settings...
Страница 100: ...2301E Digital Control Manual 26641 90 Woodward Figure 4 5 Typical Transient Response Curves...
Страница 181: ...Manual 26641 2301E Digital Control Woodward 171 Declarations...