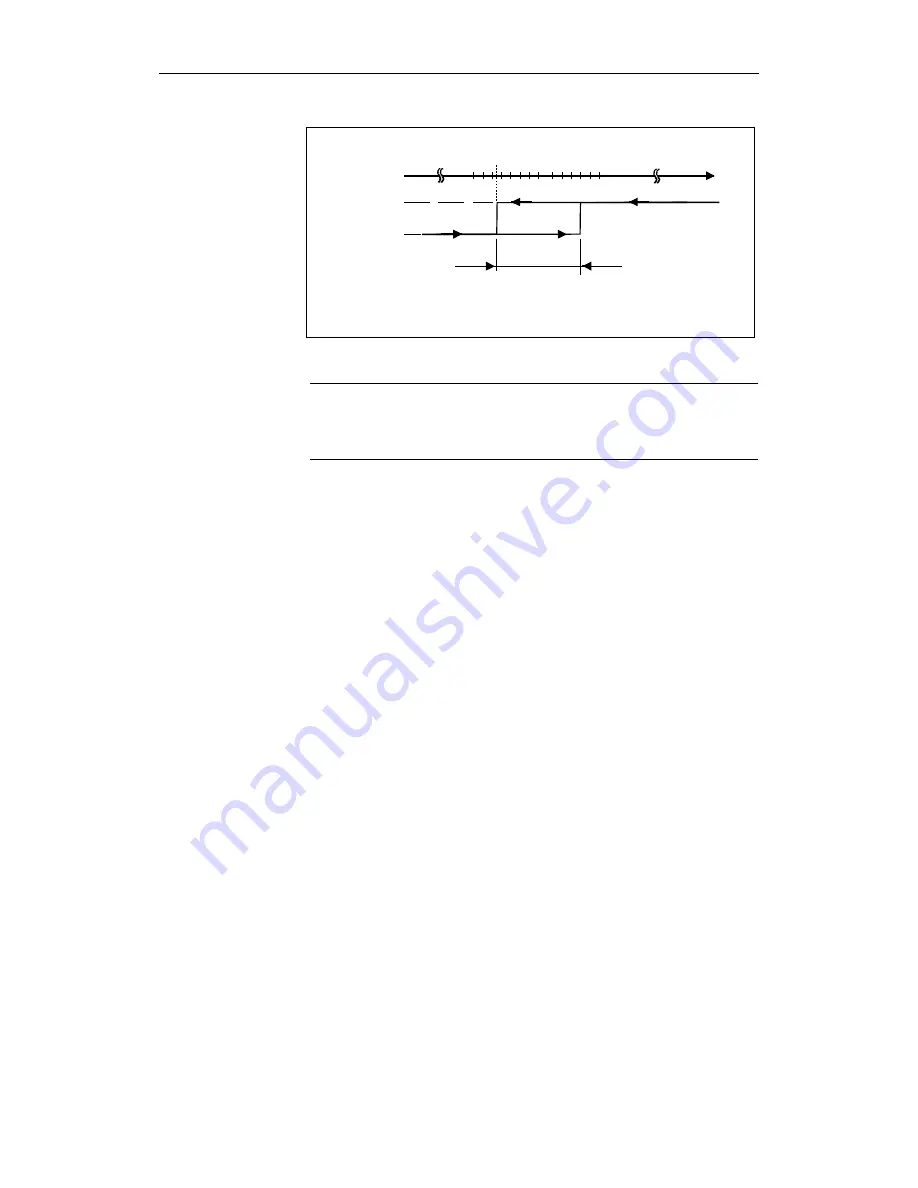
11.03
3 Safety-Related Functions
3.7 Safe software cams (SN)
© Siemens AG 2003 All Rights Reserved
SINUMERIK 840D/SIMODRIVE 611 digital SINUMERIK Safety Integrated (FBSI) - Edition 11.03
3-117
SN_05.DSF
s
SGA = 1
Cam position
SGA = 0
Tolerance
for safe
cams
Fig. 3-20
Hysteresis of cam SGAs
Note
Dynamic deviations in the cam signals at I/O devices themselves still occur as
a result of the different signal run times between the NCK and PLC I/O
devices. These deviations must be taken into account.
The status of the individual cams is indicated via SGAs SN1+, SN2+, SN3+,
SN4+ and SN1-, SN2-, SN3-, SN4-.
In the
NCK monitoring channel
, the NCK SGAs are assigned to output
terminals via the following machine data:
For 840D
MD 36988: $MA_SAFE_CAM_PLUS_OUTPUT
[
n
]
MD 36989: $MA_SAFE_CAM_MINUS_OUTPUT
[
n
]
In the
drive monitoring channel
, the PLC SGAs are mapped in the NC/PLC
interface (refer to Chapter 4, "Interface signals") and output via the PLC I/O by
the PLC user program.
The modulo display of the safe actual value is selected and parameterized for
rotary axes using the following machine data:
MD 30300: $MA_IS_ROT_AX
MD 30320: $MA_DISPLAY_IS_MODULO
MD 30330: $MA_MODULO_RANGE
The modulo range (cam actual value range) for rotary axes with cam can be set
using the following machine data:
MD 36902/1302: $MA_/$MD_SAFE_IS_ROT_AX
MD 36905/1305: $MA_/$MD_SAFE_MODULO_RANGE
The size of the cam actual value range should be selected to match the modulo
display of the safe actual value.
Output assignment
for SN
Modulo display of safe
actual value
(840D, SW4.2 and
higher)
Safe cams for
endlessly turning
rotary axes (840D,
SW4.2 and higher)