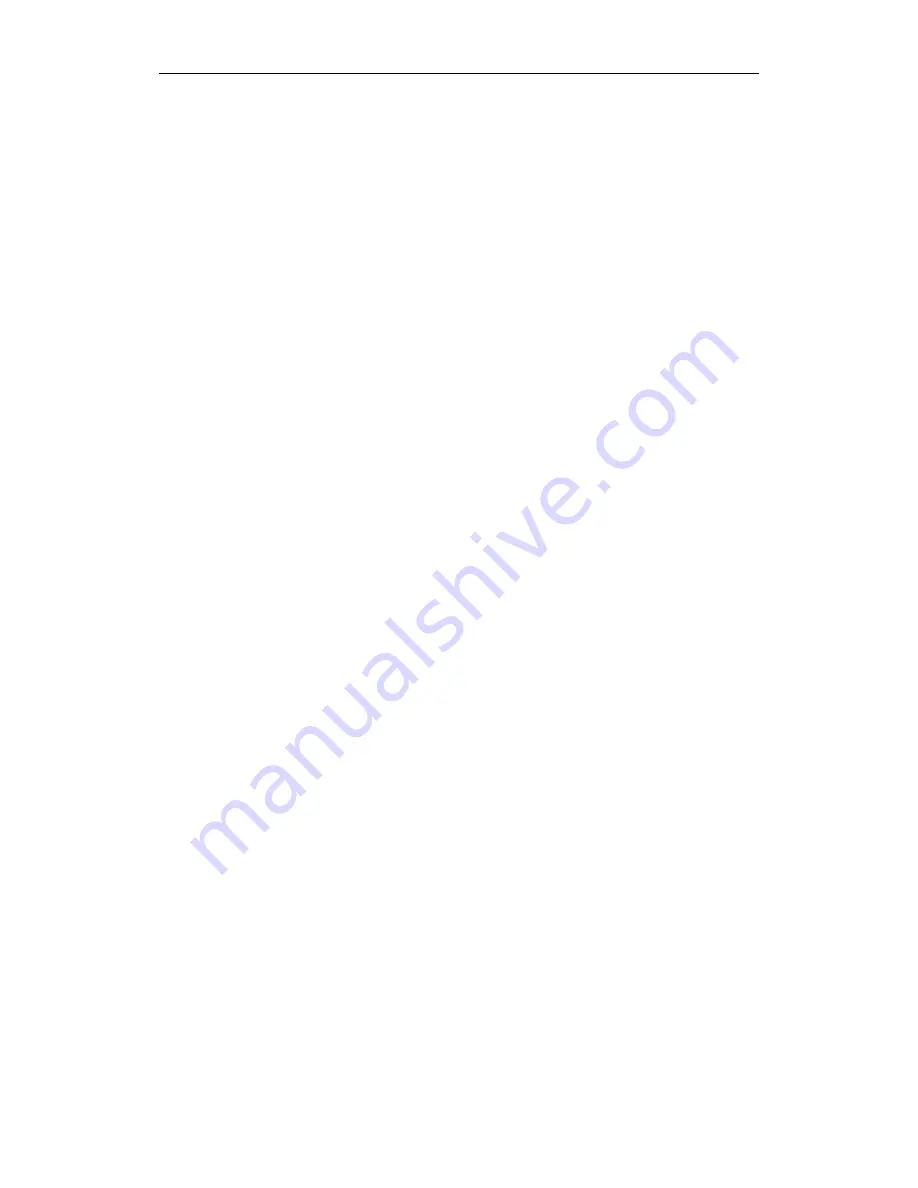
3 Safety-Related Functions
11.03
3.1 Basic mechanisms of SI functions
© Siemens AG 2003 All Rights Reserved
3-58
SINUMERIK 840D/SIMODRIVE 611 digital SINUMERIK Safety Integrated (FBSI) - Edition 11.03
Ø
Optocoupler control
Effect -> module-specific
When the optocoupler control voltage is switched-out, this means that when a
fault condition develops, the gating unit pulses are not converted in the power
module of the drive into a torque. Electrical isolation between the drive
converter DC link (600V) and the motor is therefore not possible. This is also
not required for the "functional safety".
Measure
Ø
can be controlled through two channels, physically de-coupled from
the drive and the NC. This provides an effective and safe possibility of
canceling the drive converter pulses on a module-for-module basis – and is
incorporated in the cyclic tests (forced checking procedure). The requirements
for EMERGENCY STOP are fulfilled. It is not always absolutely necessary to
open the line contactor.
Before working on live components (e.g. maintenance, service …) it is always
necessary to isolate the machine from the line supply.
3.1.2 Shutdown
paths
The drive pulses must be cancelled through two channels. The machine
manufacturer needs to configure a shutdown path in the NCK monitoring
channel and another in the drive monitoring channel.. (refer to Fig. 3-2,
"Shutdown path of the drive CPU" and Fig. 3-3, "Shutdown path of the NCK
CPU" via Terminal 663).
For SI the shutdown paths are utilized by stop functions with the highest priority
STOP A and STOP B. These stop functions can be initiated through any
monitoring channel (for example, if an active STOP C, STOP D or STOP E
function has not been able to shut down the drives).
It is therefore absolutely essential to ensure that the shutdown paths operate
properly and this must be checked at the specified intervals (e.g. after power
ON).
The pulse cancellation test is initiated via the PLC-SGE "test stop selection" (it
can also be initiated internally in the case of an error). The SGE can be
supplied from an assigned PLC HW input or a signal (memory bit) from the PLC
user program. The comparator in the drive CPU directly activates a pulse inhibit
via the drive bus in the drive module (internal signal "cancel pulses"). The
checkback signal is also output directly by the drive module via the drive bus
(internal signal "pulses cancelled status"). No additional wiring is required. The
comparator in the drive channel is supplied via a PLC interface data block (refer
to Chapter 4, "Interface signals").
Shutdown paths to
cancel pulses
Shutdown path of
drive CPU