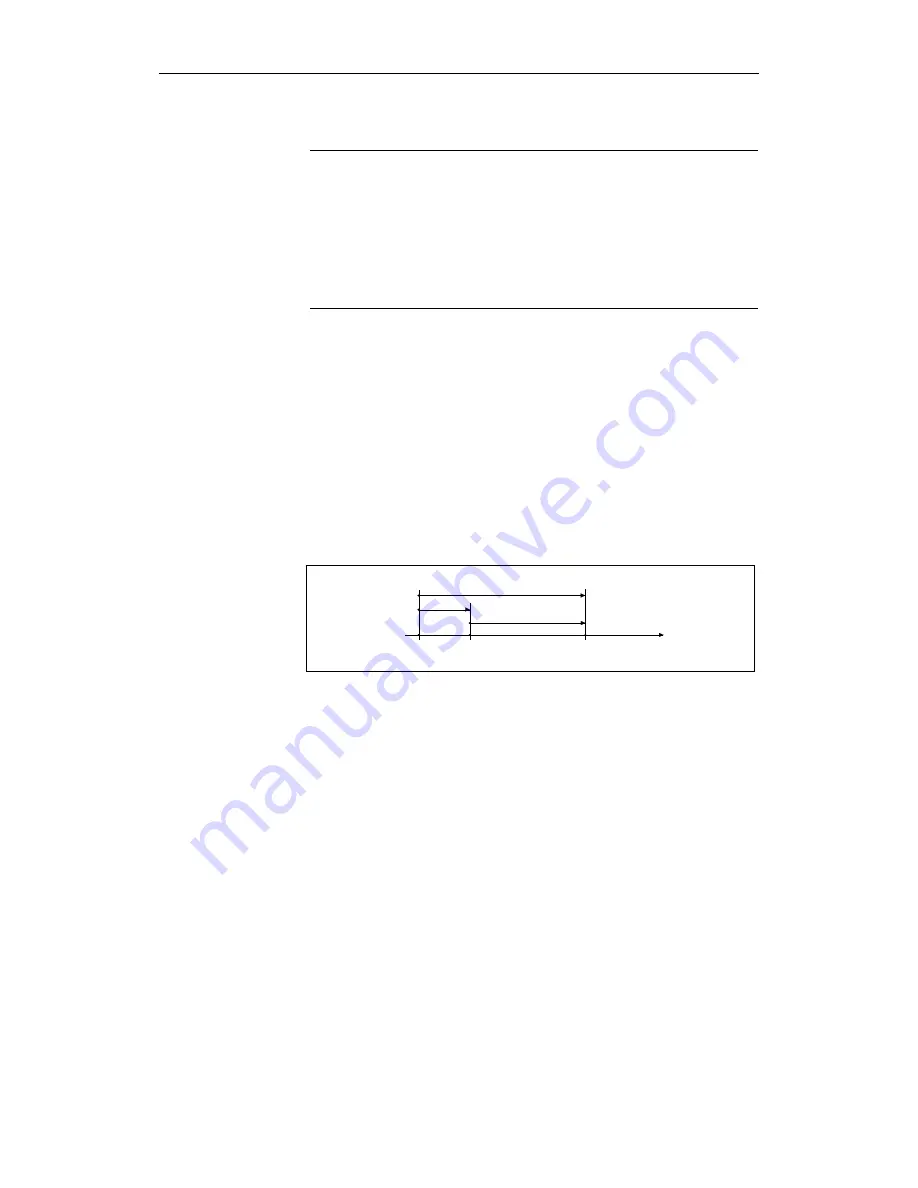
3 Safety-Related Functions
11.03
3.11 Encoder mounting arrangements
© Siemens AG 2003 All Rights Reserved
3-170
SINUMERIK 840D/SIMODRIVE 611 digital SINUMERIK Safety Integrated (FBSI) - Edition 11.03
Note
SW 5.1 and higher
If the ratio of the gear between the motor and load is not slip-free, the
1-encoder system must be selected. The 2nd spindle encoder is connected to
another drive module via an actual-value input. SE and SN cannot be
configured in such cases (refer to Chapter 3.11.5, "Application: Spindle with
2 encoders and drive with slip").
For SW 5.2 and higher, systems with slip are also possible (refer to
Chapter 3.11.4).
3.11.2
Adjustment, calibration, axis states and historical data
For 2-encoder systems, the built-in encoder is generally an integral component
of the motor (the encoder is adjusted to match the motor). The information
about distance, speed and rotor position (on synchronous drives) is obtained
from one encoder. It is no longer possible to adjust the encoders in motor
measuring systems in the conventional sense.
The machine zero and encoder zero are calibrated purely on the basis of the
offset value (the machine must be calibrated). This process must be carried out
for both incremental and absolute encoders.
Absoluter G eberistwert
Verschiebe-
wert
Lageistwert
G eber-
nullpunkt
M aschinen-
nullpunkt
Einschaltposition/
Stillstandsposition
ABSOL_01.DSF
Fig. 3-42
Positions and actual values
When calibrating the machine, a known or measured position is approached by
means of a dial gauge, fixed stop, etc. and the offset value determined. This
offset is then entered in the appropriate machine data. Calibration is always
required for a position-controlled axis/spindle.
References:
/IAD/, SINUMERIK 840D Installation and Start-Up Guide
/FBD/,
SINUMERIK
840D,
Descriptions
of
Functions
R1, "Reference Point Approach"
The axis state "axis not referenced" is reached after the power supply has been
connected and the drive and control system have completely run-up. This state
is indicated using the axis-specific interface signal "reference point reached" as
follows:
Motor encoder
adjustment
Machine calibration
"Axis not referenced"
state