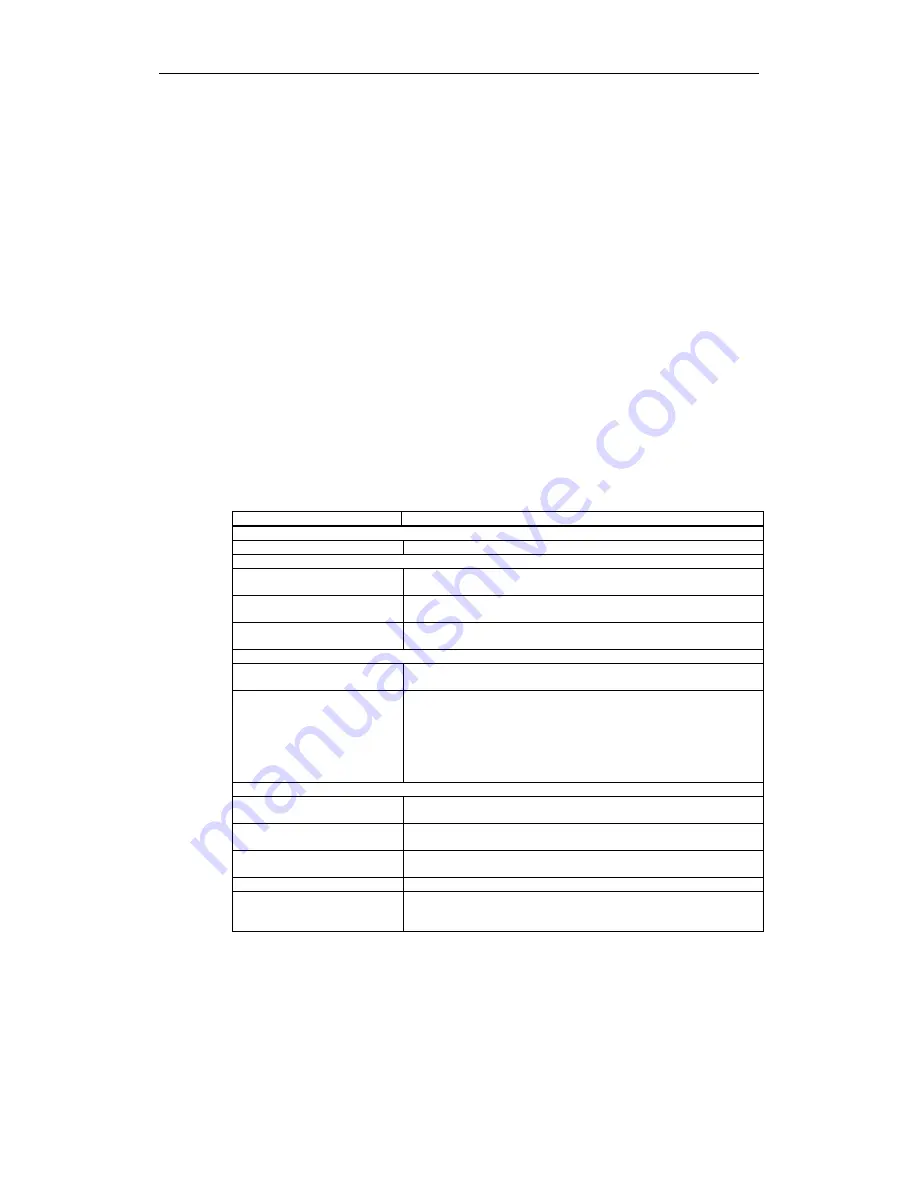
11.03
5 Commissioning
5.4 NCK acceptance test support
© Siemens AG 2003 All Rights Reserved
SINUMERIK 840D/SIMODRIVE 611 digital SINUMERIK Safety Integrated (FBSI) - Edition 11.03
5-289
The acceptance test report function is based on the interaction between the
NCK/drive and the SinuCom NC operator interface. This means that if this
function is used, these components must have a certain minimum software
version.
SinuCom NC software
Version 06.03.07. or higher
NCU system software
Version 06.04.15 or higher
The basic functionality of the SinuCom NC software is explained within the
scope of its own documentation. This documentation also provides information
about the steps when handling the acceptance test support function, a
description of the screen forms and the menu prompting. This is the reason that
this is not handled in this documentation.
References:
Start-up Tool SINUMERIK SinuCOM NC
Edition
08.2003
5.4.1
Scope of the test list
The test steps of the SI acceptance test, supported by the system, is based on
the previous test execution and comprises the following steps:
Designation
Purpose of the test step
General
Overview
Document the machine details (e.g. manufacturer, machine type,…)
Check the forced-checking procedure measures
Shutdown paths
Test the forced checking procedure of the shutdown paths for the
NCK and drive.
External stops
Test the forced checking procedure of the (used) external stop
responses (when using SPL).
SPL inputs/outputs
Test the forced checking procedure (if required) of the external SPL
I/O.
Qualitative function checks
EMERGENCY STOP
Test the internal EMERGENCY STOP functionality when executed
via external stop responses and the response to the external SPL I/O.
Inter-relationships between
functions
Test all of the states relevant for the safety functions that should be
first documented within the scope of a function table or similar
(interdependency of sensor signals, positions, modes).
In this case, the following should be taken into account – the active
monitoring function for SI-monitored axes (internal safety functions)
and the switching state of safety-related external SPL output
peripherals
Quantitative function checks
SBH (safe operating stop)
Test the response when provoking that the SBH limit value is
exceeded and define associated characteristic quantities/parameters.
SG (safely-reduced speed)
Test the response when provoking that the SG limit value is exceeded
and define associated characteristic quantities/parameters.
SE (safe software limit switch)
Test the response when provoking that the SE limit value is exceeded
and define associated characteristic quantities/parameters.
Termination
Finished
The test results are saved and loaded.
The acceptance report is generated based on the test results that
have been determined.
Software requirements