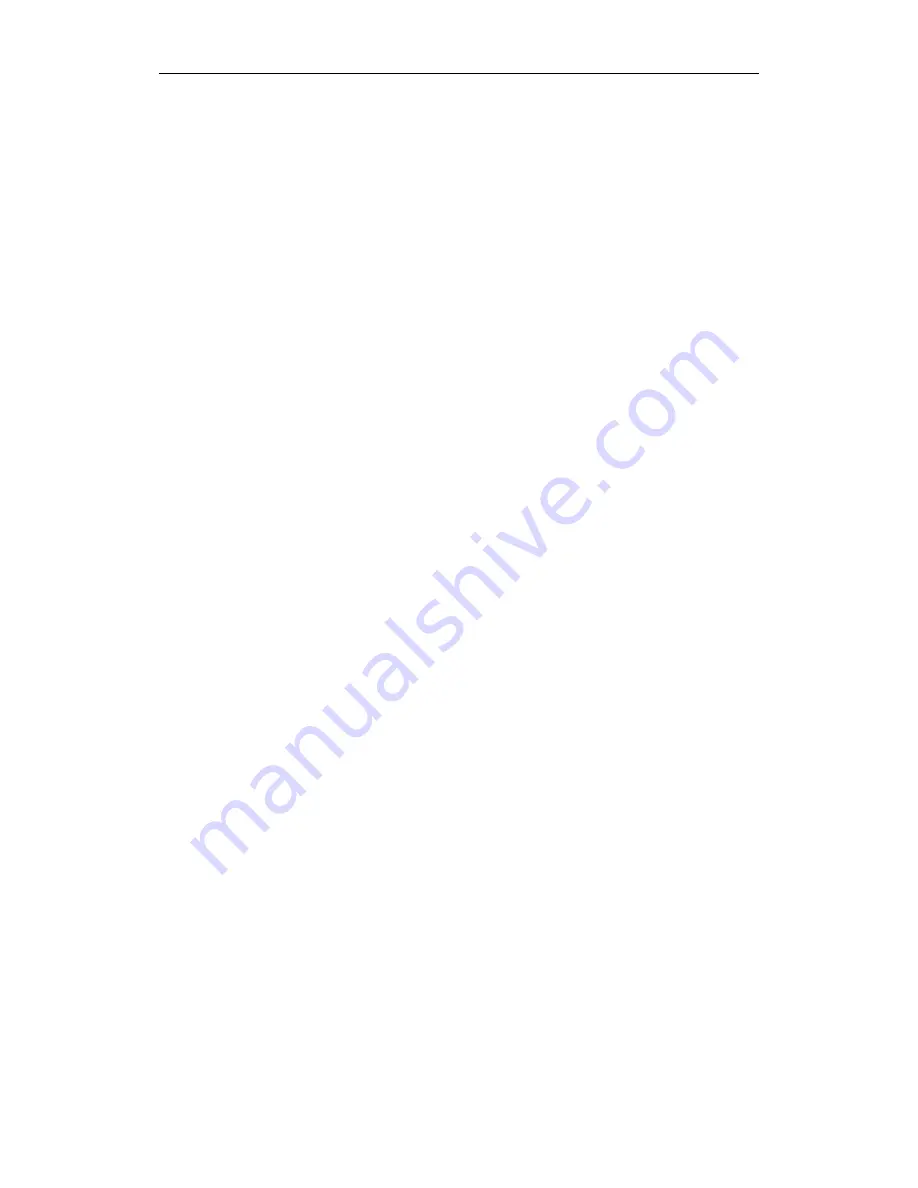
11.03
2 General Information about Integrated Safety Systems
2.8 Overview of the safety-related functions
© Siemens AG 2003 All Rights Reserved
SINUMERIK 840D/SIMODRIVE 611 digital SINUMERIK Safety Integrated (FBSI) - Edition 11.03
2-39
2.8 Overview of the safety-related functions
The safety-related functions are available in all modes and can communicate
with the process using safe input/output signals.
They can be implemented individually for each individual axis:
•
Safe standstill
A monitoring function or sensor (e.g. light barrier) responds and brings a
moving drive to a standstill.
•
Safe operating stop (SBH)
Monitors the drives during standstill. The drives remain fully functional in
the position controlled mode.
•
Safe standstill (SH)
The drive pulses are cancelled. The energy feed is safely and
electronically disconnected.
•
Safely-reduced speed (SG)
Configured speed limits are monitored, e.g. when setting-up without using
an agreement button.
•
Safe software limit switches (SE)
Variable traversing range limits
•
Safe software cam (SN)
Range detection
•
Safe input/output signals (SGE/SGA)
Interface to the process
•
Safe programmable logic (SPL)
All of the safe signals and internal logic are directly connected.
•
Safe brake management (SBM)
Two-channel brake control and cyclic brake test
•
Safety-relevant communication via standard bus connection of distributed
I/Os for process and safety signals via PROFIBUS using the PROFIsafe
protocol
•
Safe software relay (SI relay)
Designed to implement an EMERGENCY STOP with safe programmable
logic and similar requirements.
•
Safe braking ramp (SBR)
Monitors the speed characteristic. The actual speed must be reduced after
stop request has been issued.