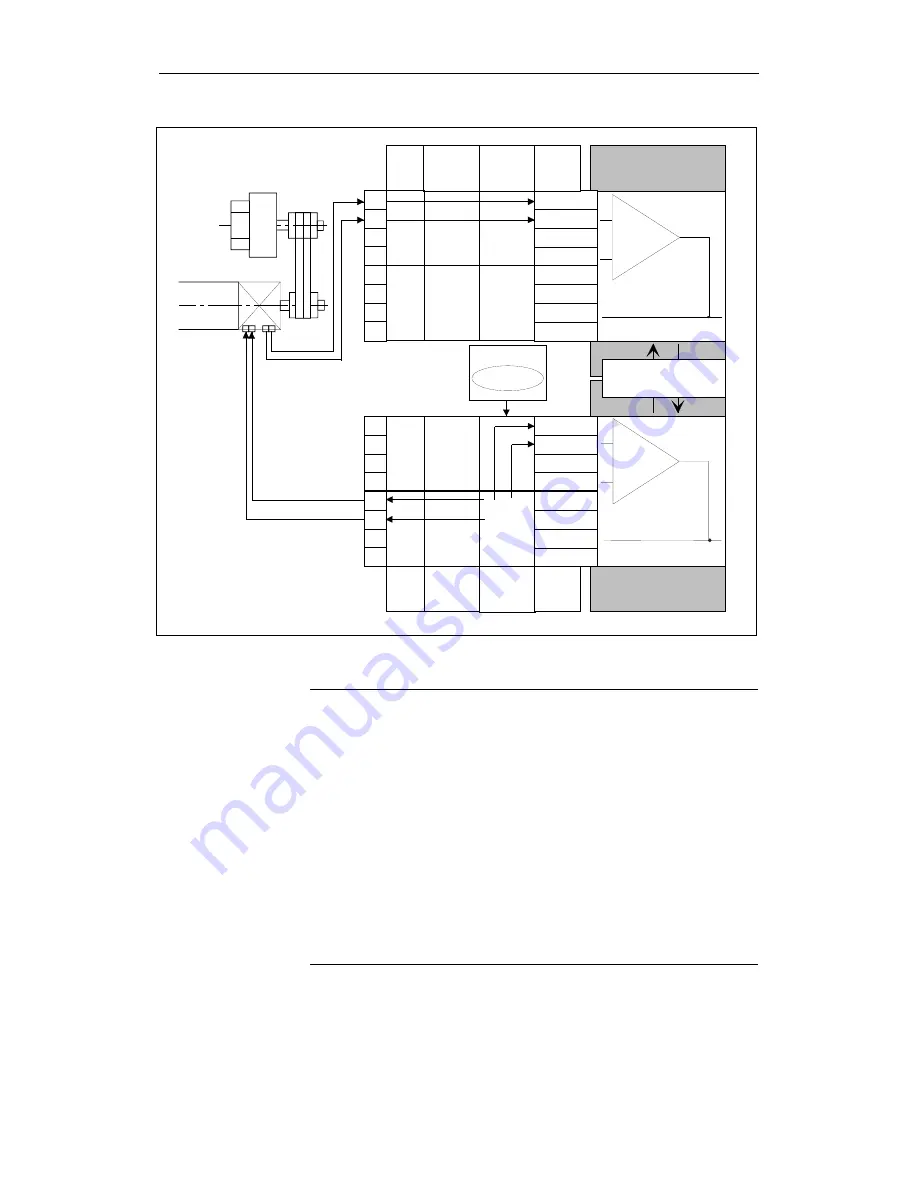
3 Safety-Related Functions
11.03
3.5 Safely-reduced speed (SG)
© Siemens AG 2003 All Rights Reserved
3-108
SINUMERIK 840D/SIMODRIVE 611 digital SINUMERIK Safety Integrated (FBSI) - Edition 11.03
NCK
HW
I/O
NCK
monitoring channel
SBH/SG
SE
SN
per axis/spindle
...
...
SBH/SG
SE
SN
per axis/spindle
PLC
HW
I/O
Drive
monitoring channel
Monitoring
comparators
Monitoring
comparators
O
I
...
...
...
...
...
I
...
...
...
...
O
I7O
images
I/O
images
Pro-
cessing
...
SGE
SGA
Bit 0
Bit 1
Bit 2
Bit 0
Bit 1
Bit 2
PLC
user
program
Result and data
cross-check
1PHxx...
Gearbox
I1 I2
O1 O2
Spindle
SGE
SGA
NC
H function
SG_02.DSF
Fig. 3-18
Spindle with 1-encoder system
Note
The above circuit (Fig. 3-16) triggers the request signals E1/E2 for gear stage
switchover for the NCK/PLC and drive simultaneously. There is usually a
delay in the internal gear stage selection because of the different processing
speeds of the two channels (due to the PLC cycle time, the NCK usually
detects the signal change earlier than the PLC). As this cannot be avoided,
gear stage changeover without errors is only possible under the following
conditions:
1. The gear stage is selected at zero speed, the time delay does not cause
an offset of the two SI values.
The gear stage is selected when the motor is moving (e.g. oscillating), i.e. the
time delay also cause an offset of the SI values. In this case, the following
measures are possible:
MD 36942 / or MD 1342 SAFE_POS_TOL must be parameterized as
necessary and resynchronization of the spindle (<axis DB>.DBX 16.6: active
measuring system) must be triggered after gear changeover (if this has not
already been done) to re-align the SI actual values.