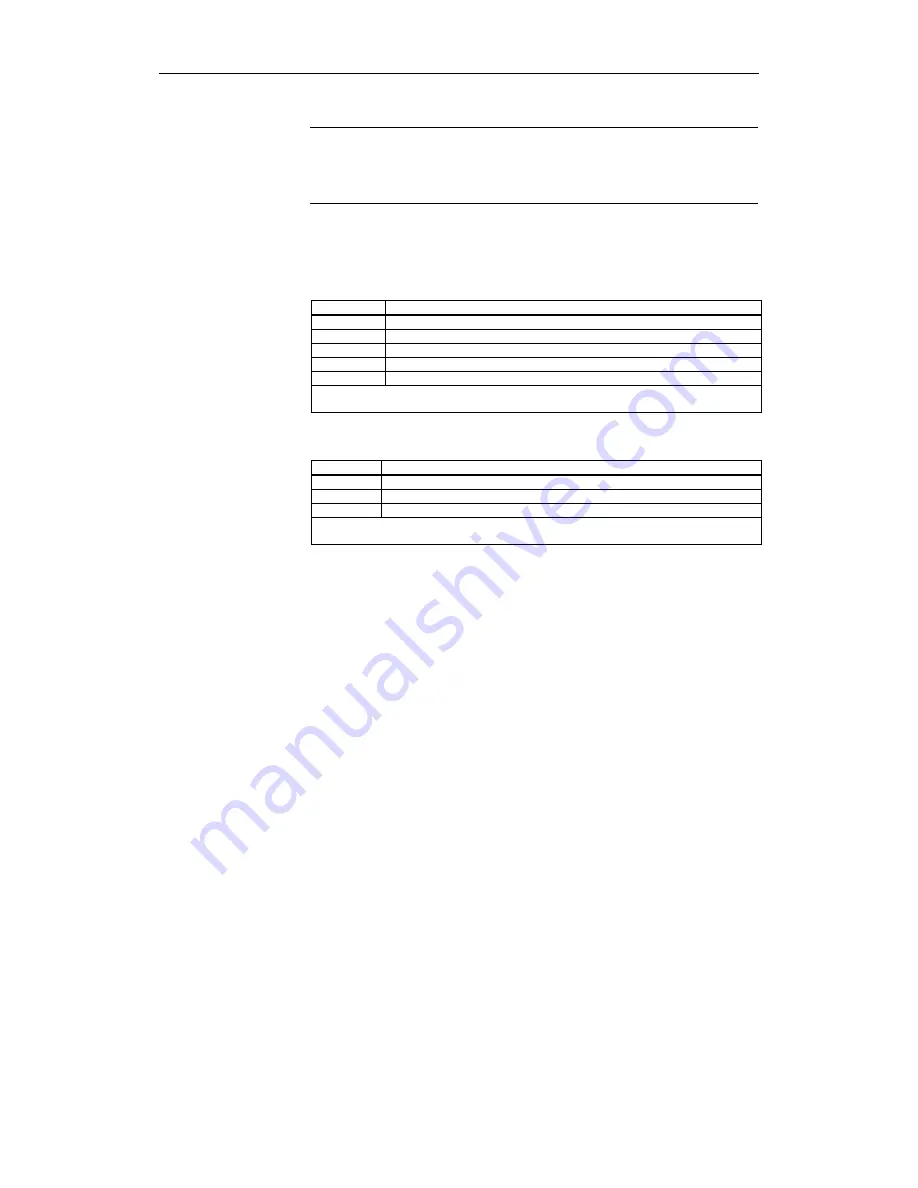
3 Safety-Related Functions
11.03
3.4 Safe operating stop (SBH)
© Siemens AG 2003 All Rights Reserved
3-86
SINUMERIK 840D/SIMODRIVE 611 digital SINUMERIK Safety Integrated (FBSI) - Edition 11.03
!
Important
After the machine has been powered-up, the "safe standstill" function must
always be tested with Safety Integrated for all axes/spindles by testing the
shutdown path.
3.3.1
Overview of the machine data for the SH function
Table 3-15
Overview of machine data for 840D
Number Name
36956 $MA_SAFE_PULSE_DISABLE_DELAY
36957 $MA_SAFE_PULSE_DIS_CHECK_TIME
36960 $MA_SAFE_STANDSTILL_VELO_TOL
36976 $MA_SAFE_PULSE_STATUS_INPUT
36986 $MA_SAFE_PULSE_ENABLE_OUTPUT
Note:
Data is described in Chapter 4, "Machine data for SINUMERIK 840D"
Table 3-16
Overview of machine data for 611 digital
Number Name
1356 $MD_SAFE_PULSE_DISABLE_DELAY
1357 $MD_SAFE_PULSE_DIS_CHECK_TIME
1360 $MD_SAFE_STANDSTILL_VELO_TOL
Note:
Data is described in Chapter 4, "Machine data for SIMODRIVE 611digital"
3.4 Safe operating stop (SBH)
The purpose of the SBH function is to safely monitor the standstill position of an
axis/spindle operating in the closed-loop position or speed controlled mode.
When SBH is active (SGA "SBH active" = 1), operating personnel can, for
example, enter protected machine areas in the set-up mode without first having
to power-down the machine.
An incremental encoder is sufficient to implement the function. The axis/spindle
is monitored for a change in the actual position value...
The features of the SBH function are as follows:
•
The axis remains in closed-loop control
•
Parameterizable standstill tolerance window
•
Stop response after SBH has responded is STOP B.
The standstill of the axis/spindle is monitored via a standstill tolerance window
that is parameterized using the following machine data:
For 840D
MD 36930:
$MA_SAFE_STANDSTILL_TOL
For 611 digital
MD 1330:
$MD_SAFE_STANDSTILL_TOL
Overview of MD
for 840D
Overview of MD
for 611 digital
Description
Function features
Standstill tolerance