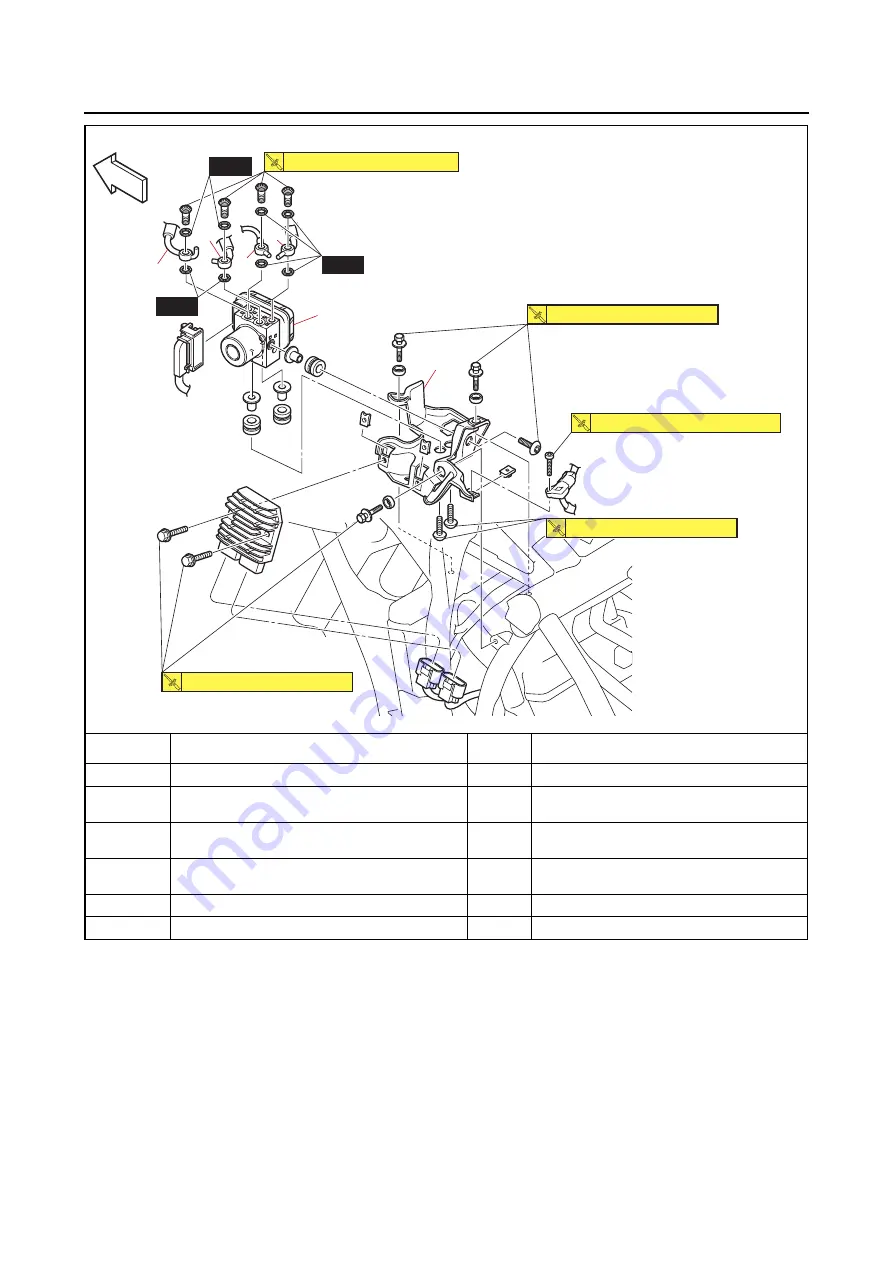
ABS (ANTI-LOCK BRAKE SYSTEM)
4-45
Removing the hydraulic unit assembly
Order
Job/Parts to remove
Q
’
ty
Remarks
8
Brake hose (hydraulic unit to rear brake caliper)
1
Disconnect.
9
Brake hose (hydraulic unit to right front brake
caliper)
1
Disconnect.
10
Brake hose (rear brake master cylinder to hy-
draulic unit)
1
Disconnect.
11
Brake hose (front brake master cylinder to hy-
draulic unit)
1
Disconnect.
12
Hydraulic unit bracket
1
13
Hydraulic unit assembly
1
7 N
•
m (0.7 k
g
f
•
m, 5.2 lb
•
ft)
T.
R
.
7 N
•
m (0.7 k
g
f
•
m, 5.2 lb
•
ft)
T.
R
.
7 N
•
m (0.7 k
g
f
•
m, 5.2 lb
•
ft)
T.
R
.
3
0 N
•
m (
3
.0 k
g
f
•
m, 22 lb
•
ft)
T.
R
.
3
.
8
N
•
m (0.
38
k
g
f
•
m, 2.
8
lb
•
ft)
T.
R
.
FWD
FW
D
New
New
New
9
8
10
11
1
3
12
Summary of Contents for Tenere 700 2020
Page 1: ...2020 SERVICE MANUAL T n r 700 XTZ690 XTZ690 U BW3 F8197 E0...
Page 2: ......
Page 6: ......
Page 8: ......
Page 56: ...CABLE ROUTING 2 33 Hydraulic unit assembly top and left side view 1 2 3 4 3 4...
Page 58: ...CABLE ROUTING 2 35 Radiator front and right side view A B C 1 2 3 3 4 5...
Page 60: ...CABLE ROUTING 2 37 Radiator left side view A B C D D F E G 1 1 2 2 3 4 5 6 6 7 5...
Page 62: ...CABLE ROUTING 2 39...
Page 65: ......
Page 213: ...CYLINDER HEAD 5 26...
Page 252: ...CRANKCASE 5 65 a 1 2 2 b 45 10 1...
Page 292: ...WATER PUMP 6 15...
Page 308: ...THROTTLE BODIES 7 15...
Page 311: ......
Page 317: ...IGNITION SYSTEM 8 6...
Page 325: ...CHARGING SYSTEM 8 14...
Page 329: ...LIGHTING SYSTEM 8 18...
Page 337: ...SIGNALING SYSTEM 8 26...
Page 393: ...FUEL INJECTION SYSTEM 8 82...
Page 407: ...IMMOBILIZER SYSTEM 8 96...
Page 452: ...ELECTRICAL COMPONENTS 8 141...
Page 469: ......
Page 470: ......