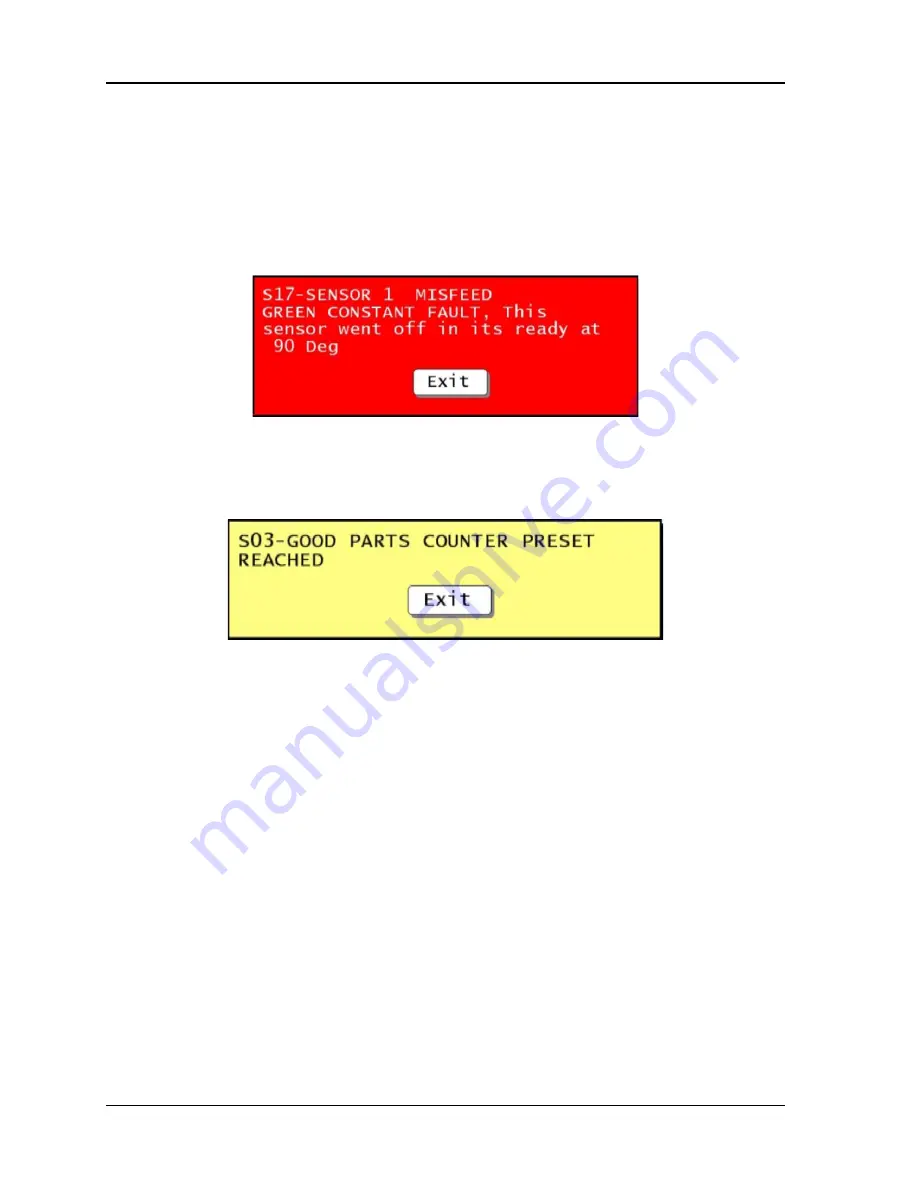
1147100
SmartPAC PRO Servo User Manual
186
Chapter 7
– Fault Messages
This chapter documents the fault messages that display on the SmartPAC PRO Servo LCD or in the
Error/Event Log, providing a brief explanation of each message and a remedy for correcting the
problem.
Responding to Fault Messages
When an error occurs, a red message window like the one shown in Figure 7-1 displays, indicating
the type of error and providing a brief explanation.
Figure 7-1. Error Code Window
If the press stops because one of the counter presets has been reached, a yellow message window like
the one shown in Figure 7-2 displays.
Figure 7-2. Counter Preset Message Window
When an error message displays, correct the malfunction or other problem, consulting the Problem
and Remedy descriptions for the appropriate error message in the sections that follow. When the
problem has been corrected, press EXIT (or Remote Reset Button, if installed) to clear the message. If
the problem has been solved, you will be able to run the press. Otherwise, you will get the fault
message again.
If the problem persists, contact Wintriss Tech. Support. Do not attempt to run the press before
correcting the problem.
In the following sections, messages are grouped in five categories:
•
Messages that display when a counter preset is reached
•
Messages that display for equipment problems
•
Messages that display for programming problems
•
Messages that display when a sensor signals a fault
•
Miscellaneous fault messages
Summary of Contents for SmartPAC PRO Servo
Page 2: ......
Page 4: ......
Page 14: ......
Page 16: ......
Page 18: ......
Page 26: ...1147100 SmartPAC PRO Servo User Manual 26 Chapter 1 Introduction ...
Page 70: ...1147100 SmartPAC PRO Servo User Manual 70 Chapter 3 Displays and Operating Modes ...
Page 158: ...1147100 SmartPAC PRO Servo User Manual 158 Chapter 5 Program Mode ...
Page 204: ......
Page 206: ......
Page 208: ......
Page 210: ......
Page 212: ......
Page 213: ......
Page 214: ......
Page 215: ......
Page 216: ......
Page 217: ......
Page 218: ......
Page 219: ......
Page 220: ......
Page 221: ......
Page 222: ......
Page 223: ......
Page 224: ......
Page 225: ......
Page 226: ......
Page 227: ......
Page 228: ......