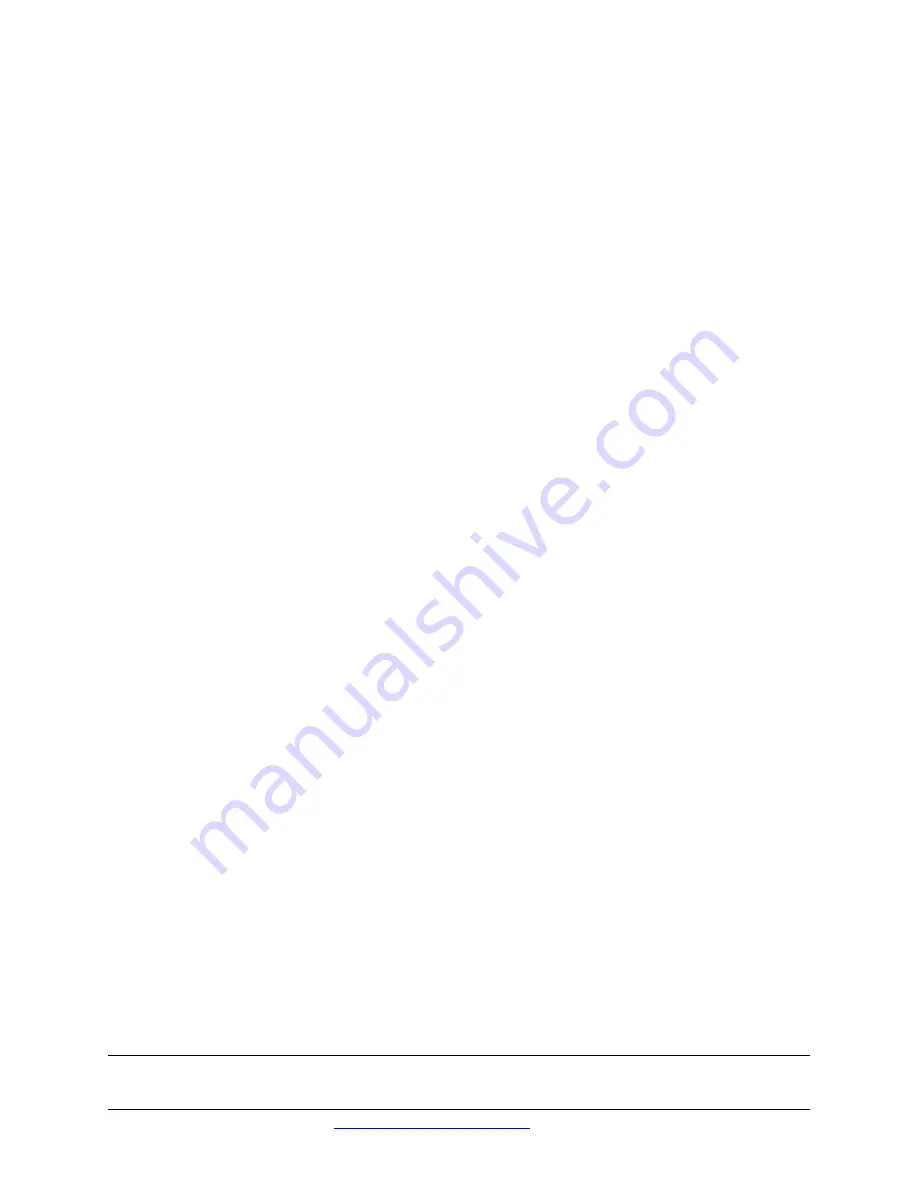
WESTLOCK CONTROLS CORPORATION
280 N. MIDLAND AVE., STE. 258, SADDLE BROOK, NJ 07663 TEL: 201-794-7650 FAX: 201-794-0913
www.westlockcontrols.com
10/5/2013
TECH-477/D.W.O. 21424
Page 36 of 206
9.
-Tout-
LCD Menu Timeout and Calibration Timeout Adjustment
10.
-RTC-
Real Time Clock Adjustment
These functions allow display, speed and valve characteristic changes from standard factory set-
tings.
Menu 4: Stro (Manual Override of Input Signal)
Entering this menu allows you access to the following three stroking functions via the
keypad:
1.
-Adjs-
Adjustment of Positioner to Any Position Using Keypad Arrows
2.
-OP-
Open, Sets the Valve to the Full Open Position
3.
-CLS-
Close, Sets the Valve to the Full Closed Position
These functions set the positioner to digital control mode (
network independent
) and
therefore allow override of the network setpoint control signal.
Menu 5: Node Add (PA node address assignment)
Entering this menu allows you access to the following three addresses assignment
functions via the keypad:
1. -Set- Selecting the desired node address
2. -Abort- Cancel the node address assignment and return to main tree option (Node Add)
3. -Save- Set the node address to stack communication. The device will reset automatically
to start to use the node address.
5.9.1 Description of Functions
LO
This function serves to set the fail position of the actuator/valve. Initially during
this calibration the valve is driven to the fail position (hard stop). The user will
notice full pressure to Outlet Port 2 and zero pressure to Outlet Port 1. After a
short period of time pressure will increase in Outlet Port 1 and the valve will
be driven to the fully energized position and then back to the fail position.
HI
This function serves to set the fully energized (full travel) position of the
actuator/valve. Initially during this calibration the valve is driven to the fully
energized (full travel) position (hard stop). The user will notice full pressure to
Outlet Port 1 and zero pressure to Outlet Port 2
PID
The PID function allows the user to modify the PID settings of the positioner
so the user can optimize the dynamic response of the positioner
regarding
the
speed of response, overshoot and
steady-state
error by varying the
appropriate gain settings. This function is often used to fine tune the PID
values obtained from the automatic calibration function (
ACAL
). The PID
entry allows the user to modify the tuning parameters in two different ways: