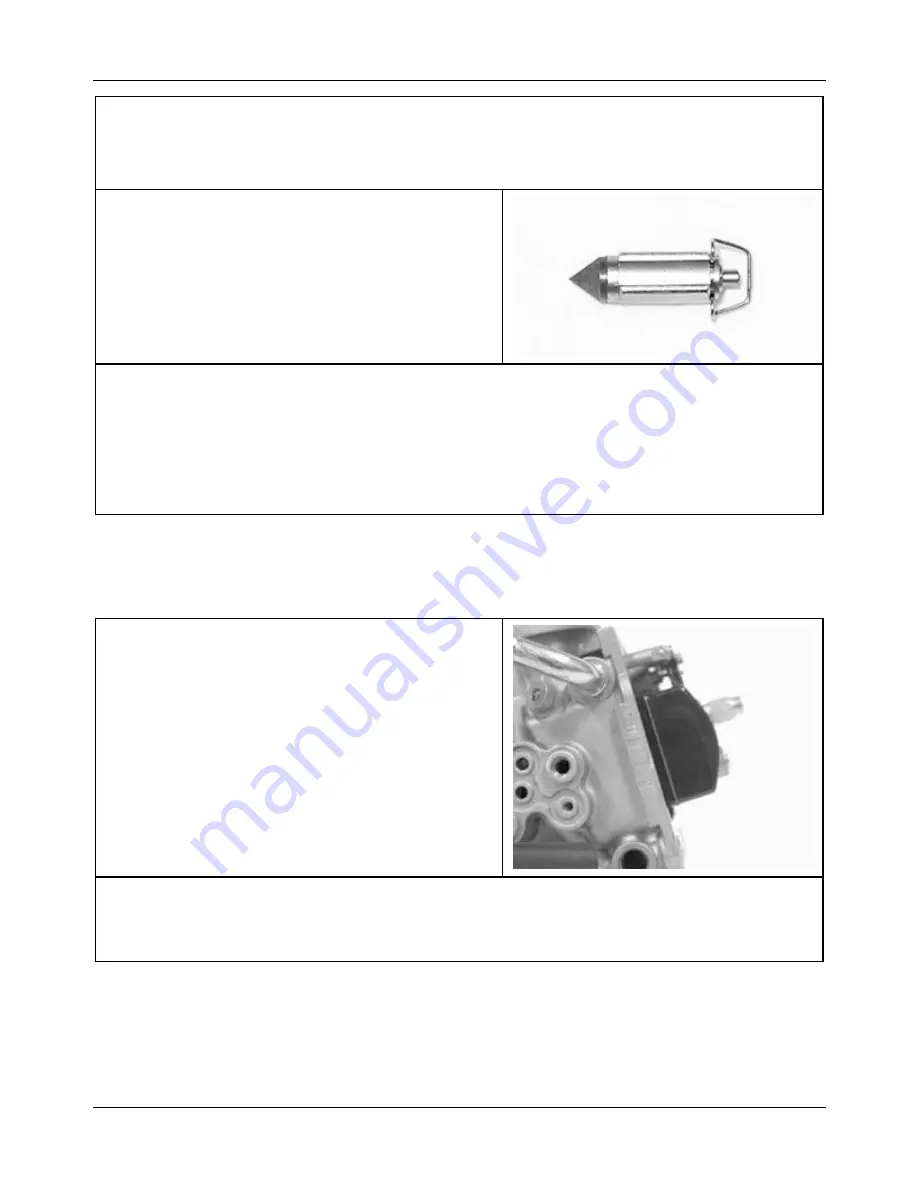
208
emulsifier.
-
Re-fit the emulsion jet, ensuring the atomizer is correctly located, and tighten.
-
Re-fit the main jet.
-
Check there are no signs of wear on the sealing
surface of the float needle, the softened pin or
the return spring.
-
If there are any signs of wear, replace the
needle with a new one.
-
Check that the float shows no signs of wear on the hinge, or the metal tab in contact with
the float needle and check that fuel has not infiltrated the float.
-
If there are any defects, replace the float with a new one.
-
Re-fit the float, together with the needle, inserting the pin from the fuel inlet side.
Note:
Ensure the return spring on the float tab is in the correct position.
10.11.10 Checking the Float Height
10.11.10.1 Kehin CVK 30 Carburetor
-
Holding the carburetor upside-down, check that
the float is parallel to the plane of the bowl.
-
If found to be out of alignment, adjust by
bending the metal tab that controls the needle,
until corrected.
-
When making adjustments to the metal tab,
ensure it remains parallel to the pin on which
the float hinges.
-
Remove the float bowl drainage screw and then thoroughly clean and blow out the bowl,
paying particular attention in cleaning the accelerator pump ducts.
-
Repeatedly actuate the accelerator pump piston and blow with compressed air.
Summary of Contents for GT 200
Page 1: ......
Page 90: ...90 9 1 2 Turn Signal Lights Horn Services and Accessory Pre Wiring ...
Page 151: ...151 10 10 Lubrication Circuit ...