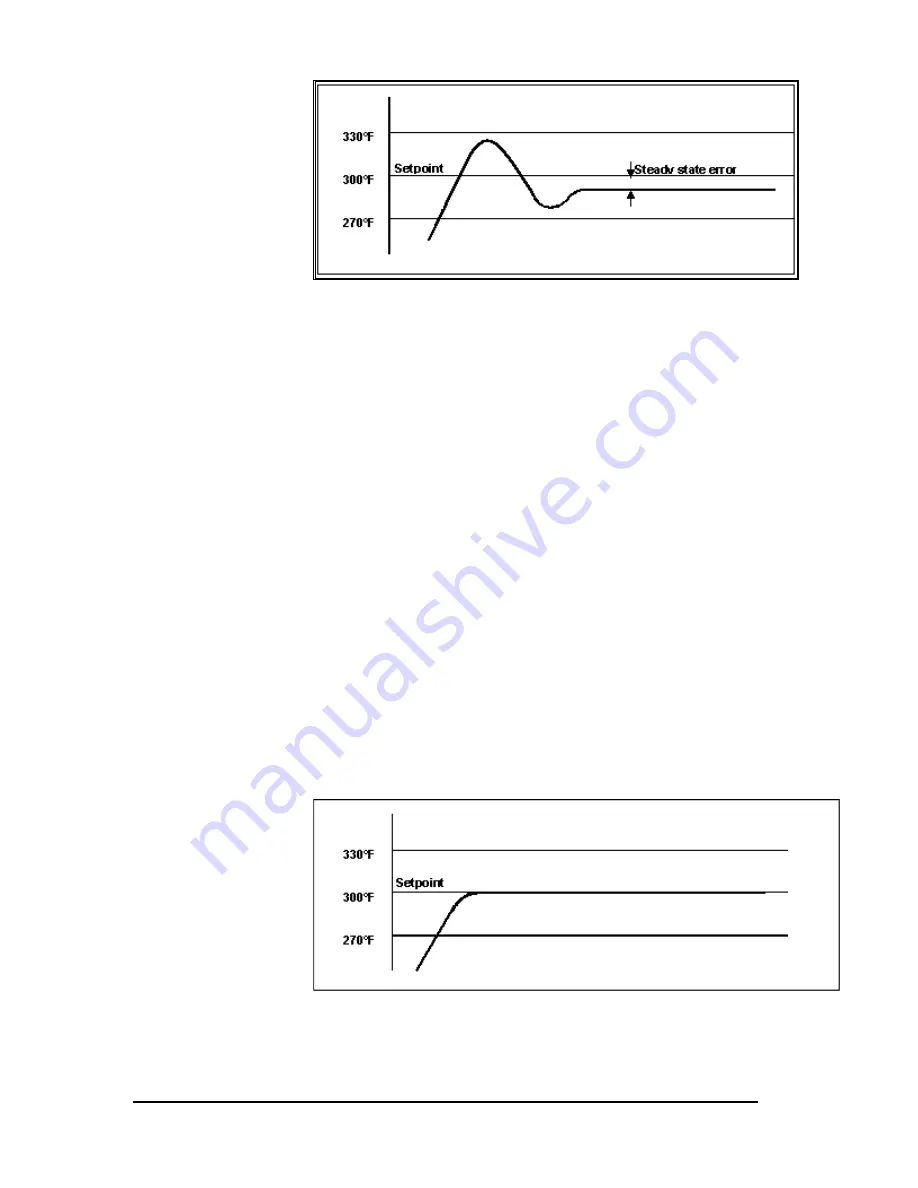
166
••••
9 - PID Loops
Simatic 505 SoftShop
Figure 9-8 Steady State Error
Thermal loading is induced by energy losses to the surroundings,
conduction through the machine, as well as the process. A proportional-
only controller can resolve this error only to a limited degree.
The Integral Component
The integral term of the PID expression provides a means to eliminate the
error in the proportional band. This term is defined as the
Error
integrated over time. Thus, in the case of the steady state error, the output
would be increased (or decreased depending on the sign of the
Error
)
over time. The amount of the integral adjustment is determined by the
magnitude of the
Error
, and the Integral gain. Excessive Integral gain
would cause an oscillation about the setpoint. Likewise, minimal Integral
gain would not reduce the
Error
in a timely manner and be ineffective.
The Derivative Component
The Derivative term of the PID expression provides a mathematical
means for limiting the rate of change of the process variable. As the rate
of change becomes larger, the derivative term reduces the output,
resulting in the reduction of the rate of change of the process variable.
The Derivative gain defines the magnitude of the output reduction as a
function of the rate of change of the process variable. Excessive
Derivative gain would result in an undesirable output oscillation as the
controller continues to eliminate the error.
When the PID gains are set appropriately, the resulting process variable
curve would take on the “ideal curve” appearance, as shown in Figure 9-
9.
Figure 9-9 Ideal Process Variable Curve
Many factors affect the process variable curve. These factors may take
the process beyond where the controller can create the ideal curve. It is
the function of the PID SmarTune utility to determine the optimum PID
gain values to achieve a response as close to the ideal curve as possible.