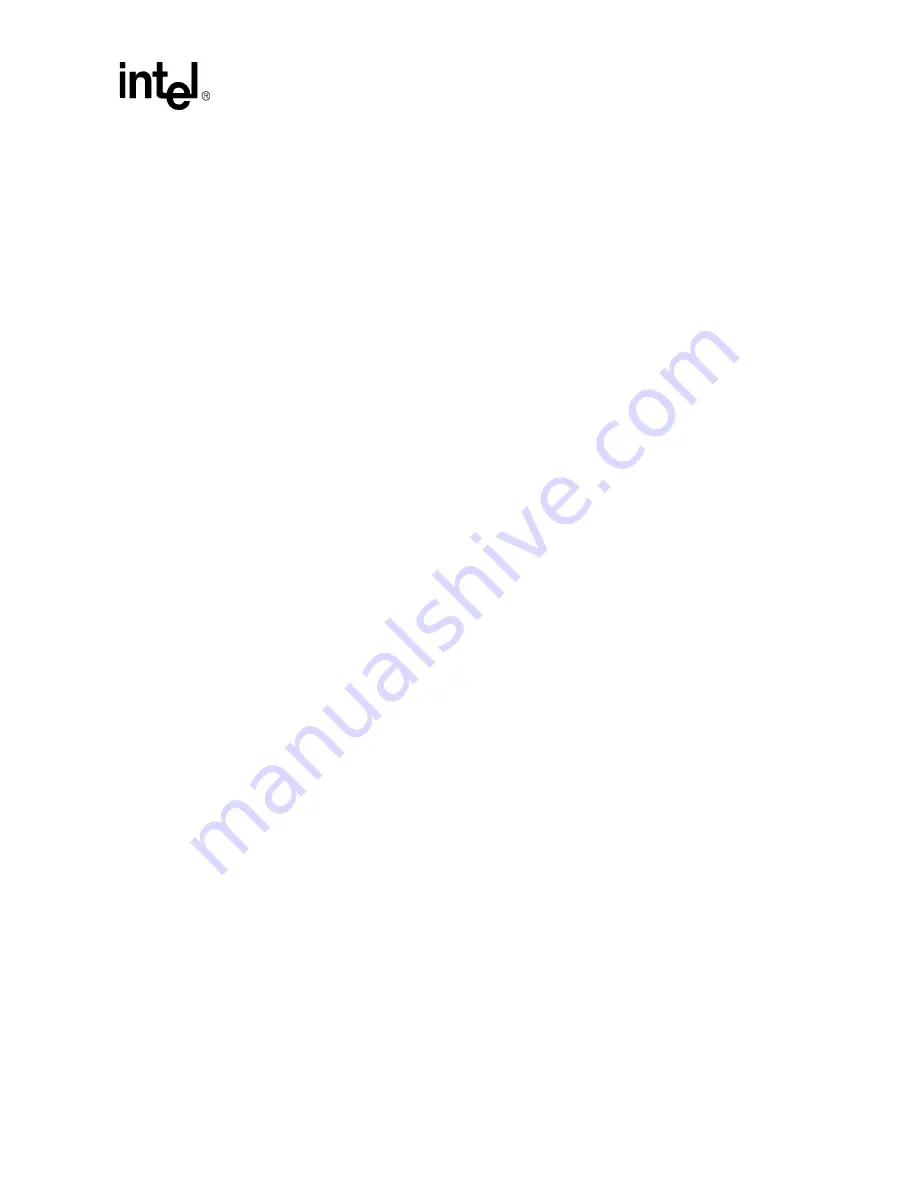
January 2007
89
Intel
®
855GME Chipset and Intel
®
6300ESB ICH Embedded Platform Design Guide
4.3.5
Intel
®
Pentium
®
M/Celeron
®
M Processor Power Status
Indicator (PSI#) Signal
PSI# is located at pin E1 of the Intel Pentium M/Celeron M processor pin-map and may be used to:
•
Improve the light load efficiency of the voltage regulator, resulting in platform power savings
•
Simplify voltage regulator designs because it removes the need for integrated 100 µs timers
that are required to mask the PWRGOOD signal during Intel SpeedStep
®
Technology
transitions
4.3.6
Thermal Power Dissipation
The amount of current required from the processor power delivery circuit and the heat generated by
processors has increased as processor frequencies go up and the silicon process geometry shrinks.
The package of any integrated device may only dissipate so much heat into the surrounding
environment. The temperature of a device, such as a processor power delivery circuit-switching
transistor, is a balance of heat being generated by the device and its ability to shed heat either
through radiation into the surrounding air or by conduction into the circuit board. Increased power
effectively raises the temperature of the processor power delivery circuits. Switching transistor die
temperatures may exceed the recommended operating value if the heat cannot be removed from the
package effectively.
As the demands for higher frequency and performance processors increase, the amount of power
dissipated, i.e., heat generated, in the processor power delivery circuit is a concern for system,
thermal and electrical design engineers. The high input voltage, low duty factor inherent in power
supply designs leads to increasing power dissipation losses in the output stage of the traditional
buck regulator topology used in the industry today.
These power dissipation losses may be attributed to the following three main areas of the processor
power delivery circuit:
•
During switching of the top control MOSFET
•
Resulting from drain to source resistance (R
DS_(ON)
) DC losses across the bottom synchronous
MOSFET
•
Generated through the magnetic core and windings of the main power inductor
There has been significant improvement in the switching MOSFET technology to lower gate
charge of the control MOSFET allowing them to switch faster, thus reducing switching losses. For
example, improvements in lowering the R
DS(ON)
parametric of the synchronous MOSFET have
resulted in reduced DC losses and the Direct Current Resistance (DCR) of the power inductor has
been reduced to lower the amount of power dissipation in the circuit’s magnetic.
However, these technology improvements by themselves are not sufficient to effectively remove
the heat generated during the high current demand and tighter voltage regulation required by
today’s mobile processors. There are several mechanisms for effectively removing heat from the
package of these integrated devices. Some of the most common methods are listed below.
•
Attaching a heat spreader or heat pipe to the package with a low thermal coefficient bonding
material.
•
Adding and/or increasing the copper fill area attached to high current carrying leads.
•
Adding or redirecting air flow to stream across the device.
Summary of Contents for 6300ESB ICH
Page 24: ...24 Intel 855GME Chipset and Intel 6300ESB ICH Embedded Platform Design Guide Introduction...
Page 102: ...102 Intel 855GME Chipset and Intel 6300ESB ICH Embedded Platform Design Guide...
Page 122: ...122 Intel 855GME Chipset and Intel 6300ESB ICH Embedded Platform Design Guide...
Page 190: ...190 Intel 855GME Chipset and Intel 6300ESB ICH Embedded Platform Design Guide Hub Interface...
Page 318: ...318 Intel 855GME Chipset and Intel 6300ESB ICH Embedded Platform Design Guide Layout Checklist...