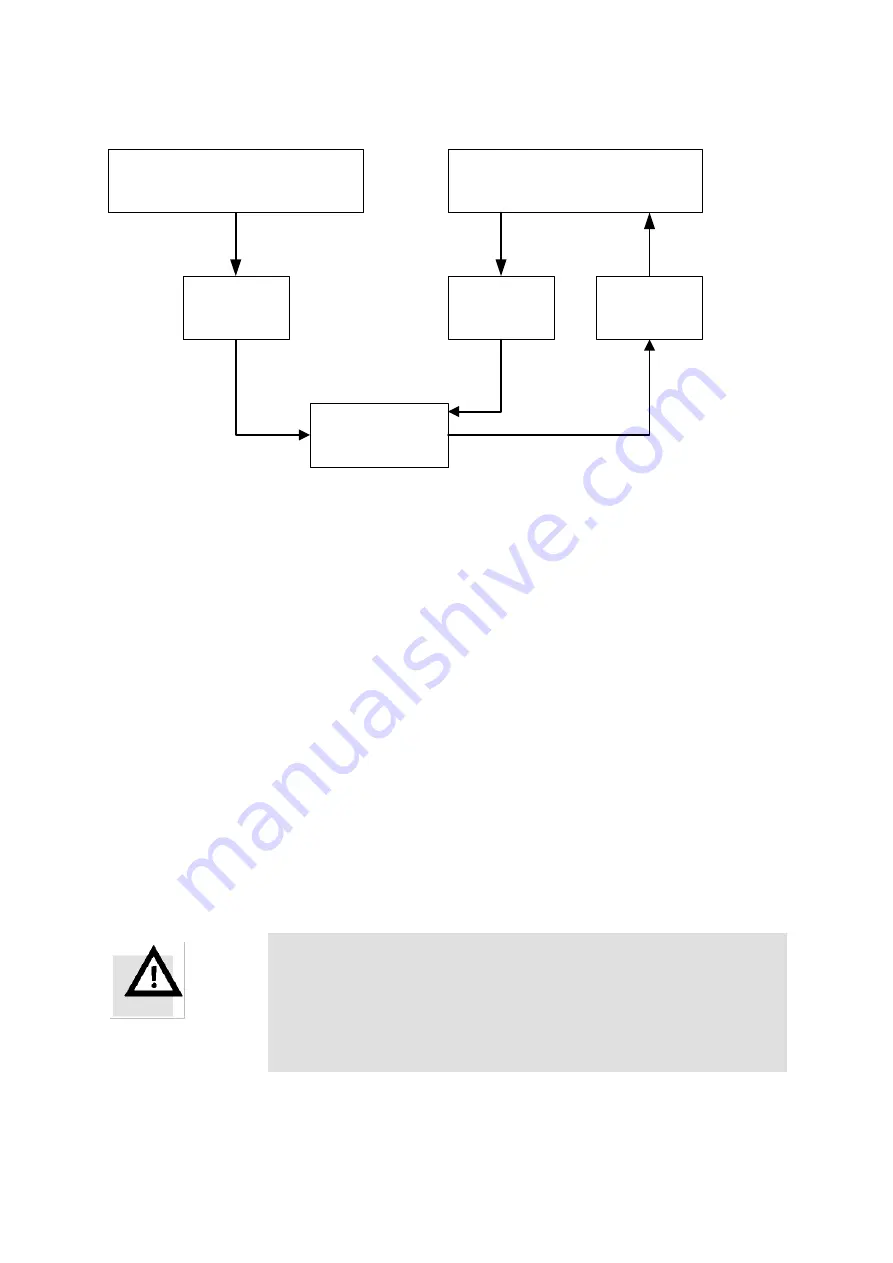
6. Setting Parameters
Festo P.BE-CMMP-CO-SW-EN 0708NH
55
The following diagram illustrates the connections between the individual parameter sets.
Default parameter set
Application-specific parameter set
CANopen
Object 1011
System
switched on
CANopen
Object 1010
Current
parameter set
Fig. 6.1: Connections between parameter sets
Two different concepts are conceivable for administering parameter sets:
1.
The parameter set is created with the parameterisation software and transmitted
completely into the individual controllers. With this procedure, only the objects
accessible via CANopen have to be put in via the CAN bus.
A disadvantage here is that
the parameterisation software is needed for each start-up of a new machine or in
case of a repair (controller exchange). This procedure therefore makes sense only for
individual units.
2.
This variant is based on the fact that most application-specific parameter sets differ
from the
default parameter set
in only a few parameters. This makes it possible for the
current parameter set
to be newly constructed via the CAN bus each time the system
is switched on. To do this, the higher level controller first loads the
default parameter
set
(call-up of the CANopen object
1011
h
_ 01
h
(
restore_all_default_parameters
). After
that, only the differeing objects are transmitted. The entire procedure lasts less than
1 second per controller. An advantage is that this procedure also works for
unparameterised controllers, so that the start-up of new systems or replacement of
individual controllers is not a problem, and the parameterisation software is not
required for this. Use of this method is recommended.
Warning
Before the final stage is switched on for the first time, make sure
the controller really contains the parameters you want.
An incorrectly parameterised controller can turn out of control and
cause personal injury or property damage.
Summary of Contents for CMMP Series
Page 2: ......