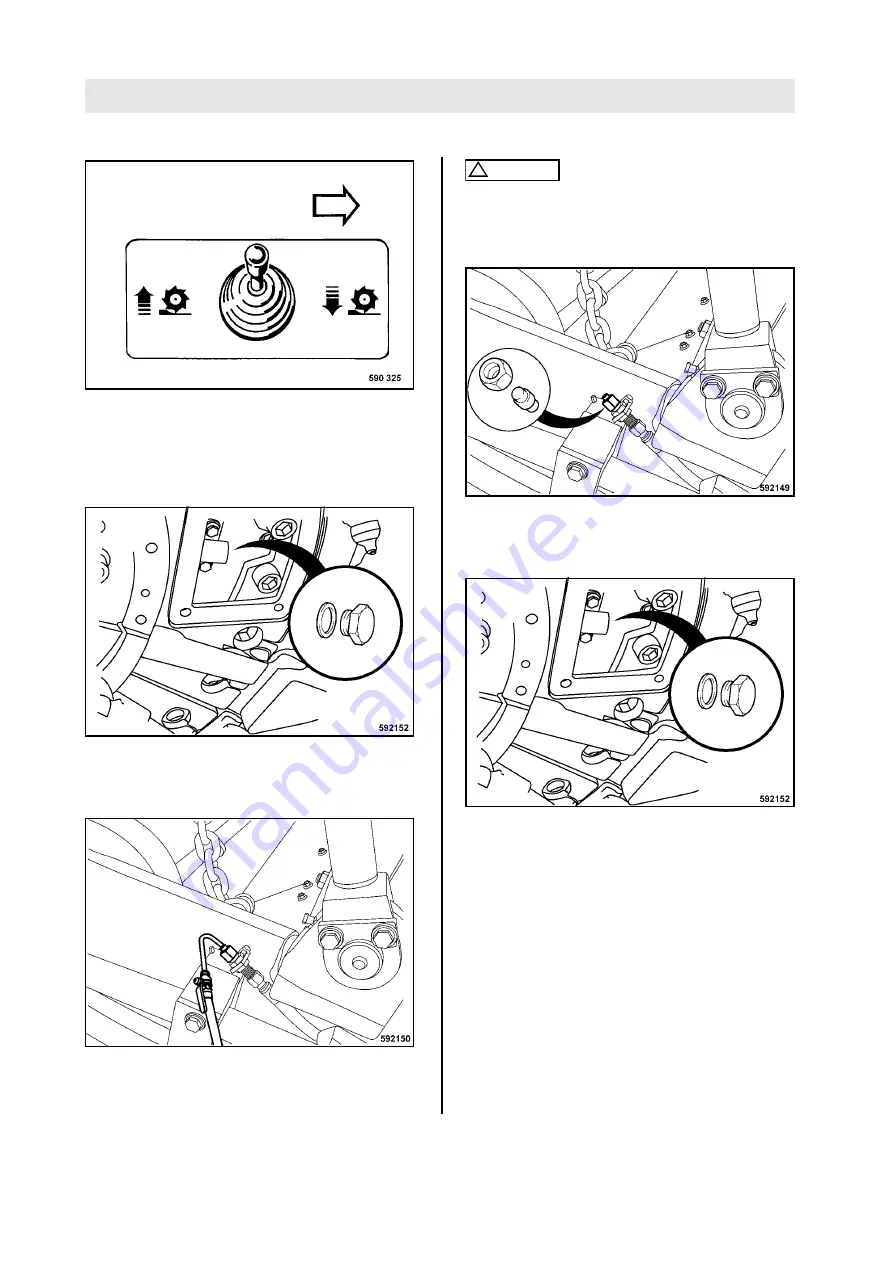
Every 500 operating hours
BOMAG
148
MPH 122-2
Fig. 298
l
With the lever for lifting/lowering the rotor (Fig.
298) lower the rotor to lowest position to gain
better access, until both rear wheels are off the
ground.
Fig. 299
l
Unscrew the oil drain plug (Fig. 299) for venti-
lation during filling.
Fig. 300
l
Use a gear oil pump (Fig. 300) to fill in oil.
!
Caution
Make sure to fill in the exact quantity!
For quality and quantity of oil refer to the "table
of fuels and lubricants".
Fig. 301
l
Turn the nut with the drain plug tightöy into the
oil drain hose (Fig. 301).
Fig. 302
l
Turn the oil drain (Fig. 302) plug back in with a
new seal ring.
Summary of Contents for Bomag MPH 122-2
Page 2: ......
Page 8: ...Table of Contents BOMAG 8 MPH 122 2...
Page 9: ...BOMAG 9 MPH 122 2 1 Technical Data...
Page 13: ...BOMAG 13 MPH 122 2 2 Safety regulations...
Page 24: ...Safety regulations BOMAG 24 MPH 122 2...
Page 25: ...BOMAG 25 MPH 122 2 3 Indicators and Controls...
Page 26: ...Indicators and Controls BOMAG 26 MPH 122 2...
Page 27: ...Indicators and Controls BOMAG 27 MPH 122 2 Fig 9 Fig 10...
Page 49: ...BOMAG 49 MPH 122 2 4 Operation...
Page 82: ...Operation BOMAG 82 MPH 122 2...
Page 83: ...BOMAG 83 MPH 122 2 5 Operation of binder dosing system...
Page 95: ...BOMAG 95 MPH 122 2 6 Maintenance...
Page 124: ...Every 10 operating hours BOMAG 124 MPH 122 2...
Page 130: ...Every 50 operating hours BOMAG 130 MPH 122 2...
Page 172: ...Every 4000 operating hours BOMAG 172 MPH 122 2...
Page 189: ...BOMAG 189 MPH 122 2 7 Trouble shooting...
Page 197: ......
Page 198: ......