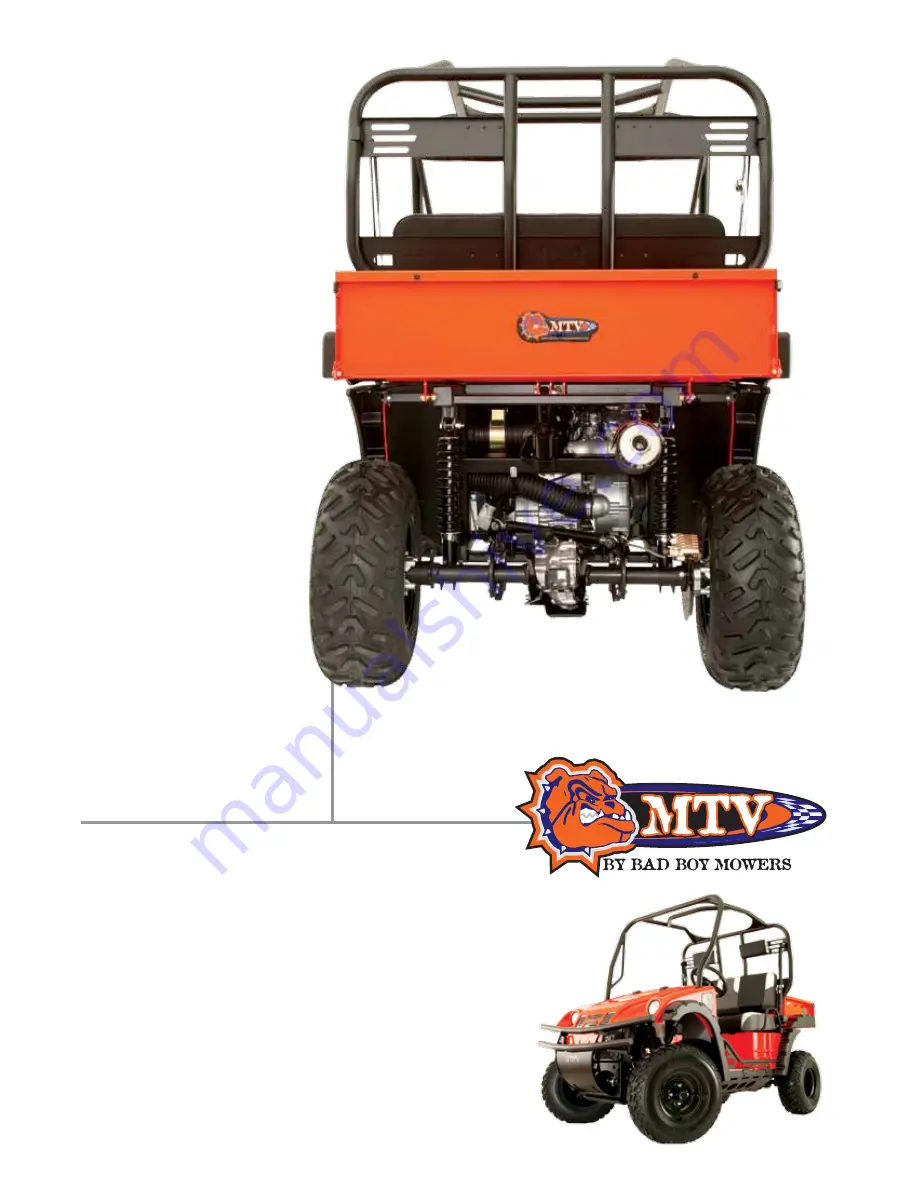
All information contained within this publication is based on the
latest product information at the time of publication. Due to
constant improvements in the design and quality of production
components, some minor discrep ancies may result between the
actual vehicle and the information presented in this publi cation.
Model 1500
(Gas Powered)
Multi-Terrain Vehicle
(MTV)
Service Manual
Summary of Contents for 1500
Page 5: ...PAGE 5 Serial Number on MTV PIN Number Located under seat on passenger side...
Page 57: ...PAGE 57...
Page 108: ...PAGE 108 SERVICE MANUAL...
Page 130: ...PAGE 130 SERVICE MANUAL...
Page 131: ...PAGE 131...