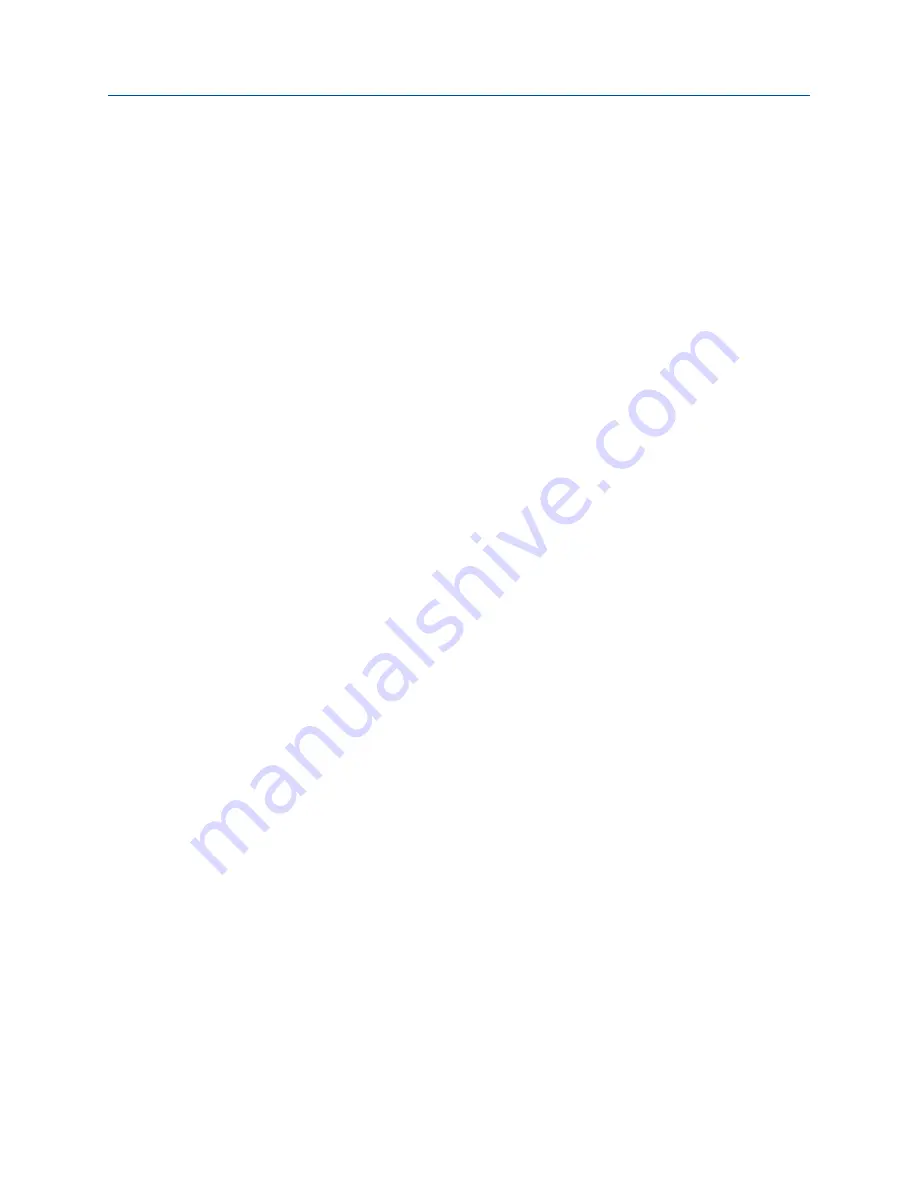
b) Identify the Discrete Output to be used for valve control.
c) Set
Source
to Batch Primary Valve.
d) Set
Polarity
to match the wiring.
The ON state of the Discrete Output must open the valve, and the OFF state must close the
valve.
e) Set
Fault Action
so that the valve will be closed if a fault occurs.
The appropriate setting is either Upscale or Downscale. The setting to use for your installation
depends on your valve type, your wiring, and your setting for
Polarity
.
4. Optional: For two-stage batching, assign one of the Discrete Outputs to the secondary valve.
You can also assign one of the Discrete Outputs to a pump when the batcher is configured for single
stage or two stage.
Configure a DO for valve control using the Field Communicator
Prerequisites
Channel B, Channel C, or Channel D must be available for valve control.
The selected channel must be wired to the valve.
The selected channel and the valve must be powered by a power supply, not by the transmitter.
Procedure
1. Verify the wiring between the selected channel and the valve.
2. Configure the selected channel to operate as a Discrete Output.
a) Choose
Configure
>
Manual Setup
>
Inputs/Outputs
.
b) Set Channel B, Channel C, or Channel D to operate as a Discrete Output.
c) Set
Power Source
to External.
3. Configure the selected channel for valve control.
a) Choose
Configure
>
Manual Setup
>
Inputs/Outputs
.
b) Select the channel to be used for valve control.
c) Select
Discrete Output x
.
d) Set
Source
to Primary Valve.
e) Set
Polarity
to match the wiring.
The ON state of the Discrete Output must open the valve, and the OFF state must close the
valve.
f) Set
Fault Action
so that the valve will be closed if a fault occurs.
The appropriate setting is either Upscale or Downscale. The setting to use for your installation
depends on your valve type, your wiring, and your setting for
Polarity
.
Configure process measurement applications
Configuration and Use Manual
March 2019
MMI-20025166
100
Micro Motion Model 5700 Transmitters with Configurable Outputs