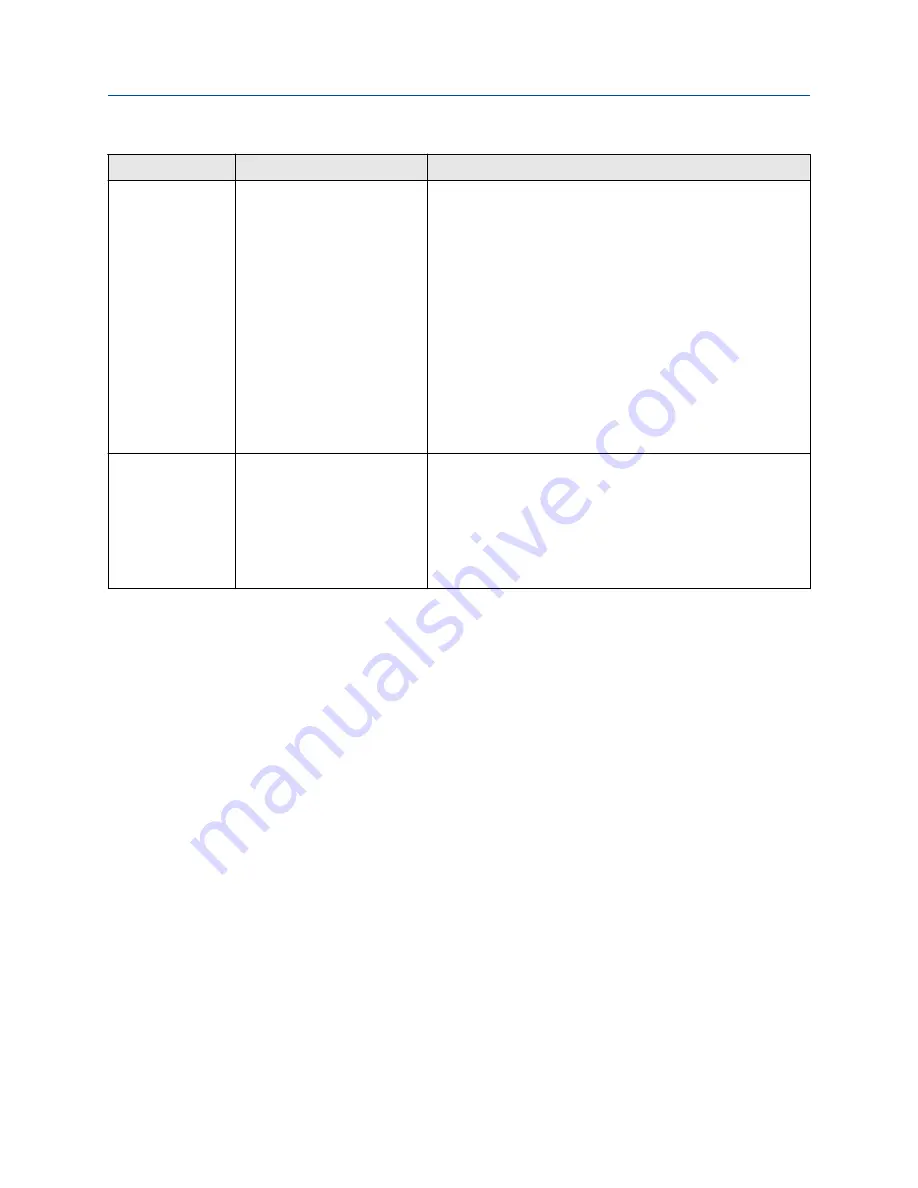
Method
Description
Setup
mA Input
An external device sends
temperature data to the meter
via the mA Input. This data will
be available in addition to the
internal temperature data.
a. Choose
Menu
>
Configuration
>
Process Measurement
>
Temperature
.
b. Set
External Temperature
to On.
c. Choose
Menu
>
Configuration
>
Inputs/Outputs
>
Channel
D
.
d. Set
I/O Type
to MAI.
e. Set
Power
appropriately.
f. Choose
I/O Settings
.
g. Set
Assignment
to External Temperature.
h. Set
Lower Range Value
and
Upper Range Value
appropriately.
Digital
communications
A host writes temperature data
to the meter at appropriate
intervals. This data will be
available in addition to the
internal temperature data.
a. Choose
Menu
>
Configuration
>
Process Measurement
>
Temperature
.
b. Set
External Temperature
to On.
c. Perform the necessary host programming and
communications setup to write temperature data to the
transmitter at appropriate intervals.
2. (A, B, C, and D tables only) Choose the method to be used to supply pressure data, and perform the
required setup.
Configure process measurement applications
Configuration and Use Manual
March 2019
MMI-20025166
56
Micro Motion Model 5700 Transmitters with Configurable Outputs