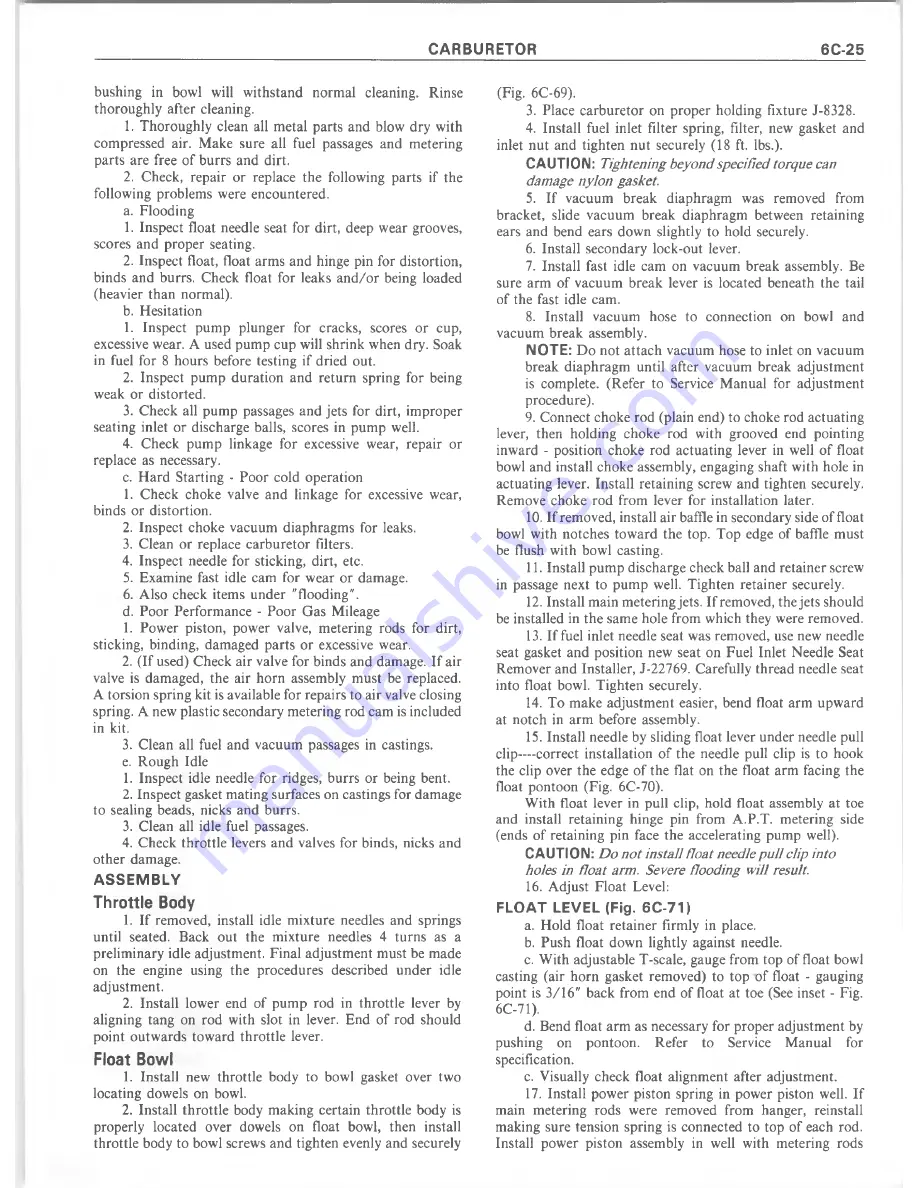
CARBURETOR
6C-25
bushing in bowl will w ithstand norm al cleaning. Rinse
thoroughly after cleaning.
1. Thoroughly clean all m etal parts and blow dry with
compressed air. Make sure all fuel passages and metering
parts are free of burrs and dirt.
2. Check, repair or replace the following parts if the
following problems were encountered.
a. Flooding
1. Inspect float needle seat for dirt, deep wear grooves,
scores and proper seating.
2. Inspect float, float arm s and hinge pin for distortion,
binds and burrs. Check float for leaks a n d /o r being loaded
(heavier than normal).
b. Hesitation
1. Inspect pum p plunger for cracks, scores or cup,
excessive wear. A used pum p cup will shrink when dry. Soak
in fuel for 8 hours before testing if dried out.
2. Inspect pum p duration and return spring for being
weak or distorted.
3. Check all pum p passages and jets for dirt, im proper
seating inlet or discharge balls, scores in pum p well.
4. Check pum p linkage for excessive wear, repair or
replace as necessary.
c. H ard Starting - Poor cold operation
1. Check choke valve and linkage for excessive wear,
binds or distortion.
2. Inspect choke vacuum diaphragm s for leaks.
3. Clean or replace carburetor filters.
4. Inspect needle for sticking, dirt, etc.
5. Examine fast idle cam for wear or damage.
6. Also check items under "flooding".
d. Poor Perform ance - Poor Gas Mileage
1. Power piston, power valve, metering rods for dirt,
sticking, binding, damaged parts or excessive wear.
2. (If used) Check air valve for binds and damage. If air
valve is damaged, the air horn assembly m ust be replaced.
A torsion spring kit is available for repairs to air valve closing
spring. A new plastic secondary metering rod cam is included
in kit.
3. Clean all fuel and vacuum passages in castings.
e. Rough Idle
1. Inspect idle needle for ridges, burrs or being bent.
2. Inspect gasket m ating surfaces on castings for damage
to sealing beads, nicks and burrs.
3. Clean all idle fuel passages.
4. Check throttle levers and valves for binds, nicks and
other damage.
ASSEMBLY
Throttle Body
1. If removed, install idle m ixture needles and springs
until seated. Back out the m ixture needles 4 turns as a
prelim inary idle adjustm ent. Final adjustm ent m ust be made
on the engine using the procedures described under idle
adjustm ent.
2. Install lower end of pum p rod in throttle lever by
aligning tang on rod with slot in lever. End of rod should
point outw ards tow ard throttle lever.
Float Bowl
1. Install new throttle body to bowl gasket over two
locating dowels on bowl.
2. Install th ro ttle body m aking certain throttle body is
properly located over dowels on float bowl, then install
throttle body to bowl screws and tighten evenly and securely
(Fig. 6C-69).
3. Place carburetor on proper holding fixture J-8328.
4. Install fuel inlet filter spring, filter, new gasket and
inlet nut and tighten nut securely (18 ft. lbs.).
C A U T IO N :
Tightening beyond specified torque can
damage nylon gasket.
5. If vacuum break diaphragm was removed from
bracket, slide vacuum break diaphragm between retaining
ears and bend ears down slightly to hold securely.
6. Install secondary lock-out lever.
7. Install fast idle cam on vacuum break assembly. Be
sure arm of vacuum break lever is located beneath the tail
of the fast idle cam.
8. Install vacuum hose to connection on bowl and
vacuum break assembly.
NOTE:
D o not attach vacuum hose to inlet on vacuum
break diaphragm until after vacuum break adjustm ent
is complete. (Refer to Service M anual for adjustm ent
procedure).
9. Connect choke rod (plain end) to choke rod actuating
lever, then holding choke rod with grooved end pointing
inward - position choke rod actuating lever in well of float
bowl and install choke assembly, engaging shaft with hole in
actuating lever. Install retaining screw and tighten securely.
Remove choke rod from lever for installation later.
10. If removed, install air baffle in secondary side o f float
bowl with notches tow ard the top. Top edge of baffle m ust
be flush with bowl casting.
11. Install pum p discharge check ball and retainer screw
in passage next to pum p well. Tighten retainer securely.
12. Install main m etering jets. If removed, the jets should
be installed in the same hole from which they were removed.
13. If fuel inlet needle seat was removed, use new needle
seat gasket and position new seat on Fuel Inlet Needle Seat
Remover and Installer, J-22769. Carefully thread needle seat
into float bowl. Tighten securely.
14. To m ake adjustm ent easier, bend float arm upward
at notch in arm before assembly.
15. Install needle by sliding float lever under needle pull
clip-—correct installation of the needle pull clip is to hook
the clip over the edge of the flat on the float arm facing the
float pontoon (Fig. 6C-70).
W ith float lever in pull clip, hold float assembly at toe
and install retaining hinge pin from A.P.T. metering side
(ends of retaining pin face the accelerating pum p well).
CAUTION:
Do not install float needle pull clip into
holes in float arm. Severe flooding will result.
16. Adjust Float Level:
FLOAT LEVEL (Fig. 6C-71)
a. Hold float retainer firmly in place.
b. Push float down lightly against needle.
c. W ith adjustable T-scale, gauge from top of float bowl
casting (air horn gasket removed) to top of float - gauging
point is 3/16" back from end of float at toe (See inset - Fig.
6C-71).
d. Bend float arm as necessary for proper adjustm ent by
pushing on pontoon.
Refer to Service M anual for
specification.
c. Visually check float alignment after adjustment.
17. Install power piston spring in power piston well. If
main metering rods were removed from hanger, reinstall
making sure tension spring is connected to top of each rod.
Install power piston assembly in well with metering rods
Summary of Contents for 1977 10 Series
Page 1: ......
Page 2: ......
Page 4: ......
Page 6: ......
Page 42: ......
Page 65: ...STEERING 3B 23 Fig 3B 65 M easure Back and Remark Housing Fig 3B 67 Tighten Lock Nut...
Page 86: ...4B 14 OVERHAUL MANUAL Fig 4B 28 Gear Teeth C ontact Pattern Check...
Page 125: ...REAR AXLE DIFFERENTIAL 4B 53 Fig 18E Gear Teeth Contact Pattern Check...
Page 156: ......
Page 164: ...4C 8 OVERHAUL MANUAL Fig 4C 12 Gear Tooth Pattern Contact Pattern...
Page 166: ......
Page 194: ......
Page 284: ......
Page 320: ......
Page 322: ...400 7A 2 OVERHAUL MANUAL Fig 7A 1C Side Cross Section Typical...
Page 444: ...7B 64 OVERHAUL MANUAL Fig 7B 11S M od el 2 03 Transfer Case Exploded V iew...
Page 458: ......
Page 466: ......
Page 467: ......
Page 468: ......