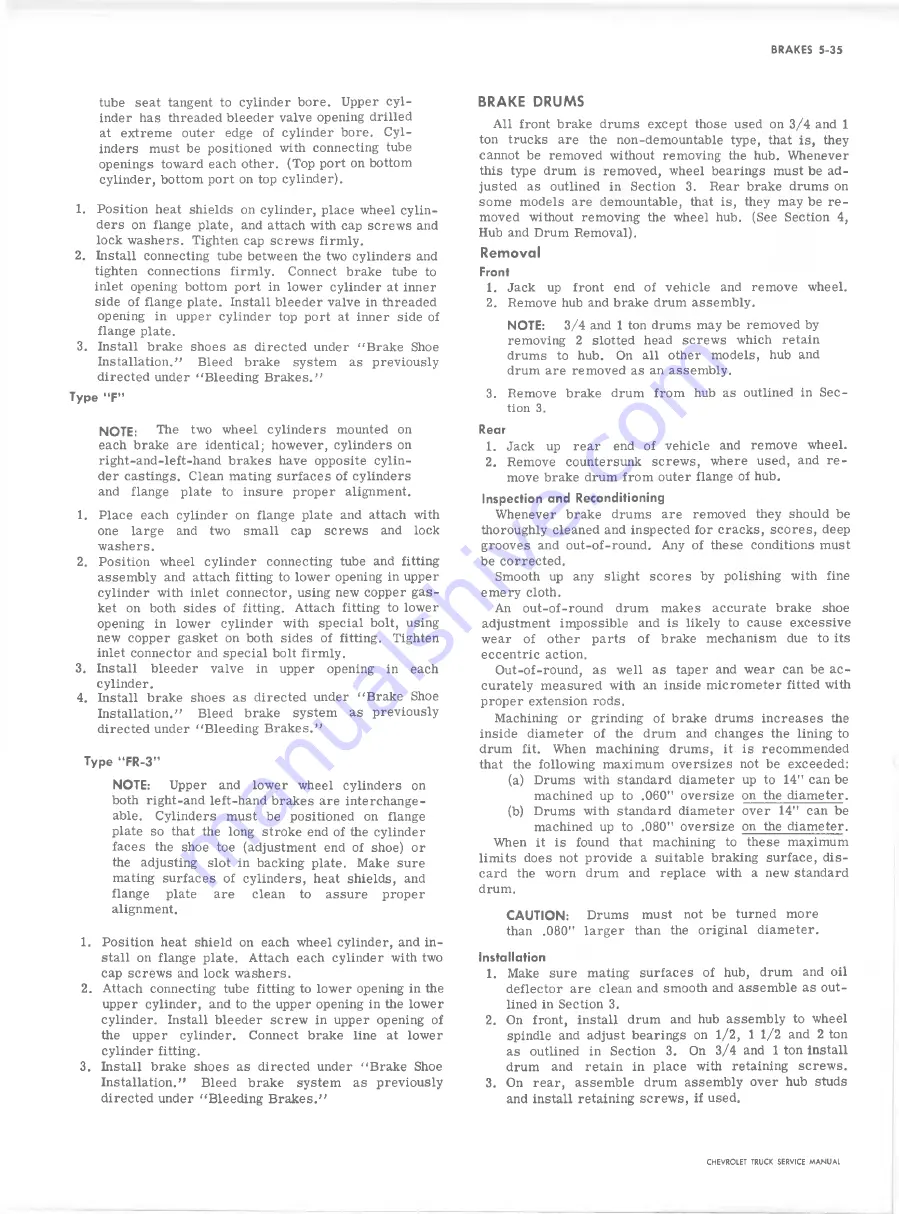
BRAKES 5-35
tube seat tangent to cylin d er b o re. Upper c y l
inder has threaded b le e d e r va lve opening d r ille d
at extrem e outer edge o f cylin d er bore. C y l
inders must be positioned with connecting tube
openings toward each other. (Top port on bottom
cylin d er, bottom p ort on top cylin d er).
1. P osition heat shields on cylin d er, place wheel c y lin
d ers on flange plate, and attach with cap screw s and
lock w ashers. Tighten cap screw s fir m ly .
2. Install connecting tube between the two cylin d ers and
tighten connections fir m ly . Connect brake tube to
in let opening bottom p o rt in lo w e r cylin d er at inner
side o f flange plate. In stall b le e d e r va lve in threaded
opening in upper cylin d er top p o rt at inner side of
flange plate.
3. Install brake shoes as d irected under “ Brake Shoe
In stallation .”
B leed brake system as p revio u sly
d irected under "B le e d in g Brakes.
”
Type “ F”
NOTE:
The two w heel cylin d ers mounted on
each brake are iden tical; how ever, cylin d ers on
righ t-an d-left-h an d brakes have opposite c y lin
d er castings. Clean mating su rfaces o f cylin d ers
and flange plate to insure p ro p er alignment.
1. P la ce each cylin d er on flange plate and attach with
one la rg e and two sm a ll cap screw s and lock
w ashers.
2. P osition wheel c y lin d e r connecting tube and fittin g
assem bly and attach fittin g to lo w e r opening in upper
cylin d er with in let connector, using new copper g a s
ket on both sides o f fittin g. Attach fittin g to low er
opening in lo w er c y lin d e r with sp ecia l bolt, using
new copper gasket on both sides o f fittin g. Tighten
in let connector and sp ecial bolt fir m ly .
3. In stall
b leed er va lv e in upper opening in each
cylin d er.
4. Install brake shoes as d irected under "B r a k e Shoe
In stallation .”
B leed brake system as p reviou sly
d irected under "B le e d in g B ra k e s .”
Type “ FR-3”
NOTE:
Upper and lo w e r wheel cylin d ers on
both right-and left-hand brakes are in terch an ge
able. C ylin ders must be positioned on flange
plate so that the long stroke end o f the cylin d er
fa ces the shoe toe (adjustm ent end o f shoe) o r
the adjusting slot in backing plate. Make sure
mating surfaces o f cylin d ers, heat shields, and
flange
plate
are
clean
to
assure
p ro p er
alignm ent.
1. P o sitio n heat shield on each w heel cylin d er, and in
s ta ll on flange plate. Attach each cylin d er with two
cap screw s and lock w ashers.
2. Attach connecting tube fittin g to lo w e r opening in the
upper cylin d er, and to the upper opening in the low er
cylin d er. In stall b le e d e r s c re w in upper opening o f
the upper cylin d er. Connect brake line at lo w er
cylin d er fitting.
3. In stall brake shoes as d irected under "B r a k e Shoe
In sta lla tion .”
B leed brake system as p revio u sly
d ire c te d under “ B leedin g B ra k e s
. n
BRAKE DRUMS
A ll fron t brake drums except those used on 3/4 and 1
ton trucks a re the non-demountable type, that is , they
cannot be rem oved without rem ovin g the hub. W henever
this type drum is rem oved, wheel bearings must be ad
justed as outlined in Section 3. R ea r brake drums on
som e m odels are demountable, that is, they may be r e
m oved without rem ovin g the wheel hub. (See Section 4,
Hub and Drum R em oval).
Rem oval
Front
1. Jack up fron t end o f v e h icle and rem ove wheel.
2. R em ove hub and brake drum assem bly.
NOTE:
3/4 and 1 ton drums may be rem oved by
rem oving 2 slotted head screw s which retain
drums to hub. On a ll other m odels, hub and
drum a re rem oved as an assem bly.
3. Rem ove brake drum fro m hub as outlined in S ec
tion 3.
Rear
1. Jack up re a r end o f veh icle and rem ove wheel.
2. R em ove countersunk screw s, where used, and r e
m ove brake drum fro m outer flange o f hub.
Inspection and Reconditioning
W henever brake drums a re rem oved they should be
thoroughly cleaned and inspected fo r crack s, s c o re s , deep
g ro o v e s and out-of-round. Any o f these conditions must
be co rrected .
Smooth up any sligh t s c o re s by polishing with fine
e m e ry cloth.
An out-of-round drum m akes accurate brake shoe
adjustment im p ossib le and is lik ely to cause ex c e s s iv e
w ear o f other p arts o f brake m echanism due to its
e c c en tric action.
O ut-of-round, as w e ll as taper and w ea r can be a c
cu rately m easured with an inside m ic ro m e te r fitted with
p ro p er extension rods.
Machining o r grinding o f brake drums in crea ses the
inside diam eter o f the drum and changes the lining to
drum fit. When machining drums, it is recom m ended
that the follow in g m axim um o v e r s iz e s not be exceeded:
(a) Drums with standard d iam eter up to 14" can be
machined up to .060" o v e r s iz e on the d ia m e te r.
(b) Drums with standard d iam eter o v e r 14" can be
machined up to .080" o v e r s iz e on the d ia m e te r.
When it is found that machining to these maximum
lim its does not p rovid e a suitable braking su rface, d is
card the worn drum and replace with a new standard
drum.
CA UTIO N:
Drums must not be turned m ore
than .080" la r g e r than the o rig in a l d ia m eter.
Installation
1. Make sure mating su rfaces o f hub, drum and o il
d e fle c to r a re clean and smooth and assem ble as out
lined in Section 3.
2. On front, in sta ll drum and hub assem bly to wheel
spindle and adjust bearin gs on 1/2, 11/2 and 2 ton
as outlined in Section 3. On 3/4 and 1 ton in stall
drum and retain in p lace with retaining screw s.
3. On re a r, assem ble drum assem bly o v e r hub studs
and in stall retaining screw s, if used.
CHEVROLET TRUCK SERVICE MANUAL
Summary of Contents for 10 Series 1970
Page 1: ......
Page 38: ...HEATER AND AIR CONDITIONING 1A 8 CHEVROLET TRUCK SERVICE MANUAL...
Page 57: ...HEATER AND AIR CONDITIONING 1A 27 Fig 35 Compressor M ountings CHEVROLET TRUCK SERVICE MANUAL...
Page 78: ......
Page 142: ...CHEVROLET TRUCK SERVICE MANUAL Fig 5 10 30 Series Truck Frame FRAME 2 4...
Page 145: ...CHEVROLET TRUCK SERVICE MANUAL FRAME 2 7...
Page 148: ......
Page 238: ......
Page 383: ...ENGINE FUEL 6M 19 F ig I t Engine Fuel S p ecial Tools CHEVROLET TRUCK SERVICE MANUAL...
Page 384: ......
Page 392: ......
Page 432: ...Fig 1 C lu tch Linkage Except P 2 0 4 0 Series...
Page 528: ...Fig 31 T yp ica l Power Steering Hose Routings...
Page 530: ......
Page 550: ......
Page 568: ...ELECTRICAL BODY AND CHASSIS 12 6 Fig 5 Rear Lighting Composite CHEVROLET TRUCK SERVICE MANUAL...
Page 628: ......
Page 640: ......
Page 649: ...SPECIFICATIONS 9 ENGINE SECTION 6 CHEVROLET TRUCK SERVICE MANUAL...
Page 671: ......