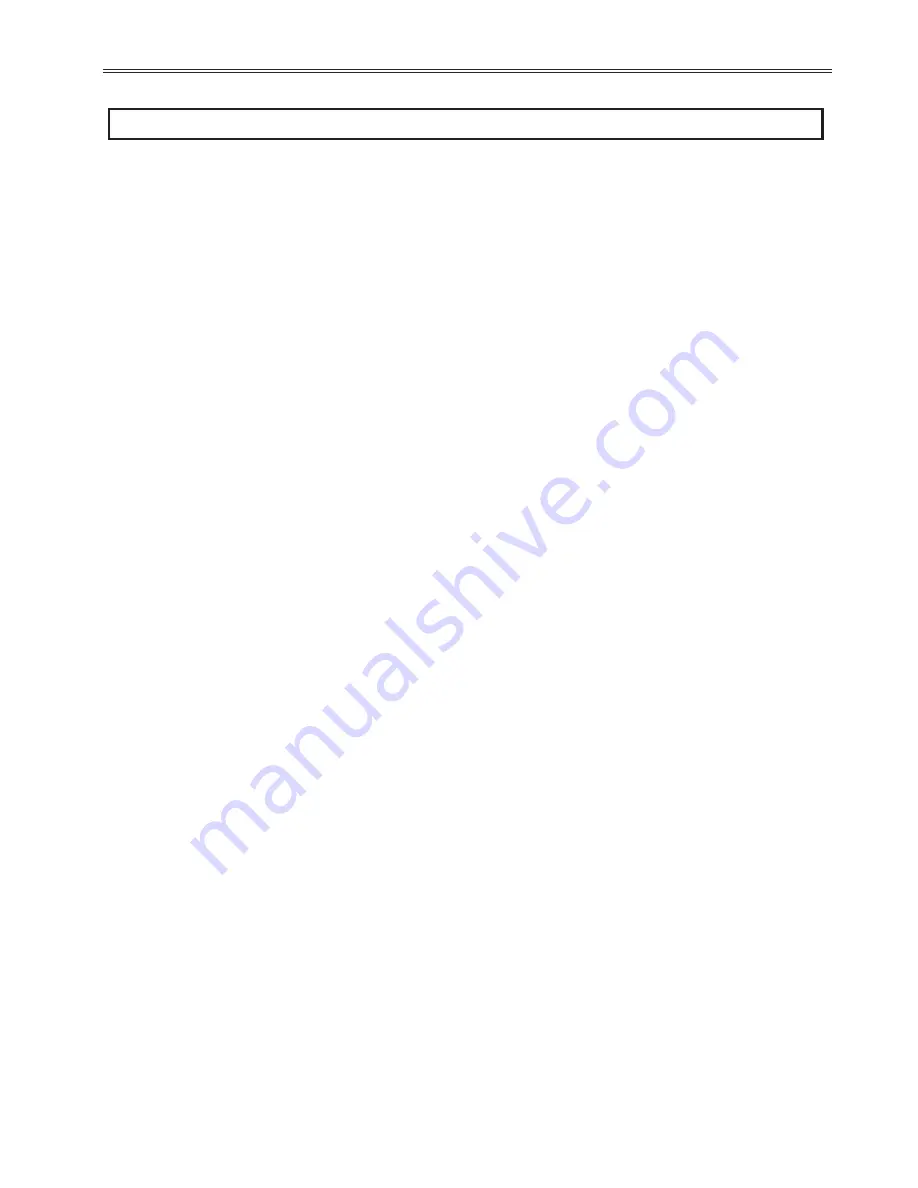
Installation Considerations
3.2
Installation Considerations
3.2.1
Site Preparation
General Information
Before the starter can be installed, the installation site must be prepared. The customer is responsible for:
•
Providing the correct power source
•
Providing the correct power protection
•
Selecting the control mechanism
•
Obtaining the connection cables, lugs and all other hardware
•
Ensuring the installation site meets all environmental specifications for the enclosure NEMA rating
•
Installing and connecting the motor
Power Cables
The power cables for the starter must have the correct NEC/CSA current rating for the unit being installed. Depending upon the model,
the power cables can range from a single #14 AWG conductor to four 750 MCM cables. (Consult local and national codes for selecting
wire size).
Site Requirements
The installation site must adhere to the applicable starter NEMA/CEMA rating. For optimal performance, the installation site must meet
the appropriate environmental and altitude requirements.
3.2.2
EMC Installation Guidelines
General
In order to help our customers comply with European electromagnetic compatibility standards, Benshaw Inc. has
developed the following guidelines.
Attention
This product has been designed for Class A equipment. Use of the product in domestic environments may cause radio
interference, in which case the installer may need to use additional mitigation methods.
Enclosure
Install the product in a grounded metal enclosure.
Grounding
Connect a grounding conductor to the screw or terminal provided as standard on each controller. Refer to layout/power
wiring schematic for grounding provision location.
Wiring
Refer to Wiring Practices on page 31.
Filtering
To comply with Conducted Emission Limits (CE requirement), a high voltage (1000V or greater) 0.1 uF capacitor
should be connected from each input line to ground at the point where the line enters the cabinet.
3.2.3
Use of Power Factor Capacitors
Power factor correction capacitors and surge capacitors CAN NOT be connected between the starter and the motor. These devices can
damage the SCRs during ramping. These devices appear like a short circuit to the SCR when it turns on, which causes a di/dt level
greater than the SCR can handle. If used, power factor correction capacitors or surge capacitors must be connected ahead of the starter
and sequenced into the power circuit after the start is completed. A programmable relay can be configured as an up-to-speed (UTS) relay
and then used to pull-in a contactor to connect the capacitors after the motor has reached full speed.
z
NOTE:
If the motor manufacturer supplies surge capacitors they must be removed before starting.
3.2.4
Use of Electro-Mechanical Brakes
If an electro-mechanical brake is used with the starter, it must be powered from the line side of the starter to ensure full voltage is applied
to the brake during a start so it will properly release. A programmable relay can be configured as a run relay and then used to pull-in a
contactor to power the brake whenever the starter is providing power to the motor.
3.2.5
Reversing Contactor
If the application requires a reversing contactor, it should be connected on the output side (load) of the soft starter. The contactor must
be closed before starting the soft starter. The soft starter must be off before switching the direction of the reversing contactor. The
reversing contactor must never be switched while the soft starter is operating.
29
3 - INSTALLATION
Summary of Contents for RediStart MX3 Series
Page 9: ...1 Introduction 1...
Page 15: ...2 Technical Specifications 7...
Page 35: ...3 Installation 27...
Page 61: ...4 Keypad Operation 53...
Page 71: ...5 Parameter Groups 63...
Page 79: ...6 Parameter Description 71...
Page 145: ...7 Theory of Operation 137...
Page 188: ...NOTES 180 7 THEORY OF OPERATION...
Page 189: ...8 Troubleshooting Maintenance 181...
Page 208: ...NOTES 200 8 TROUBLESHOOTING MAINTENANCE...
Page 209: ...Appendices 201...
Page 237: ...Publication History Revision Date ECO 00 12 15 06 Initial Release...