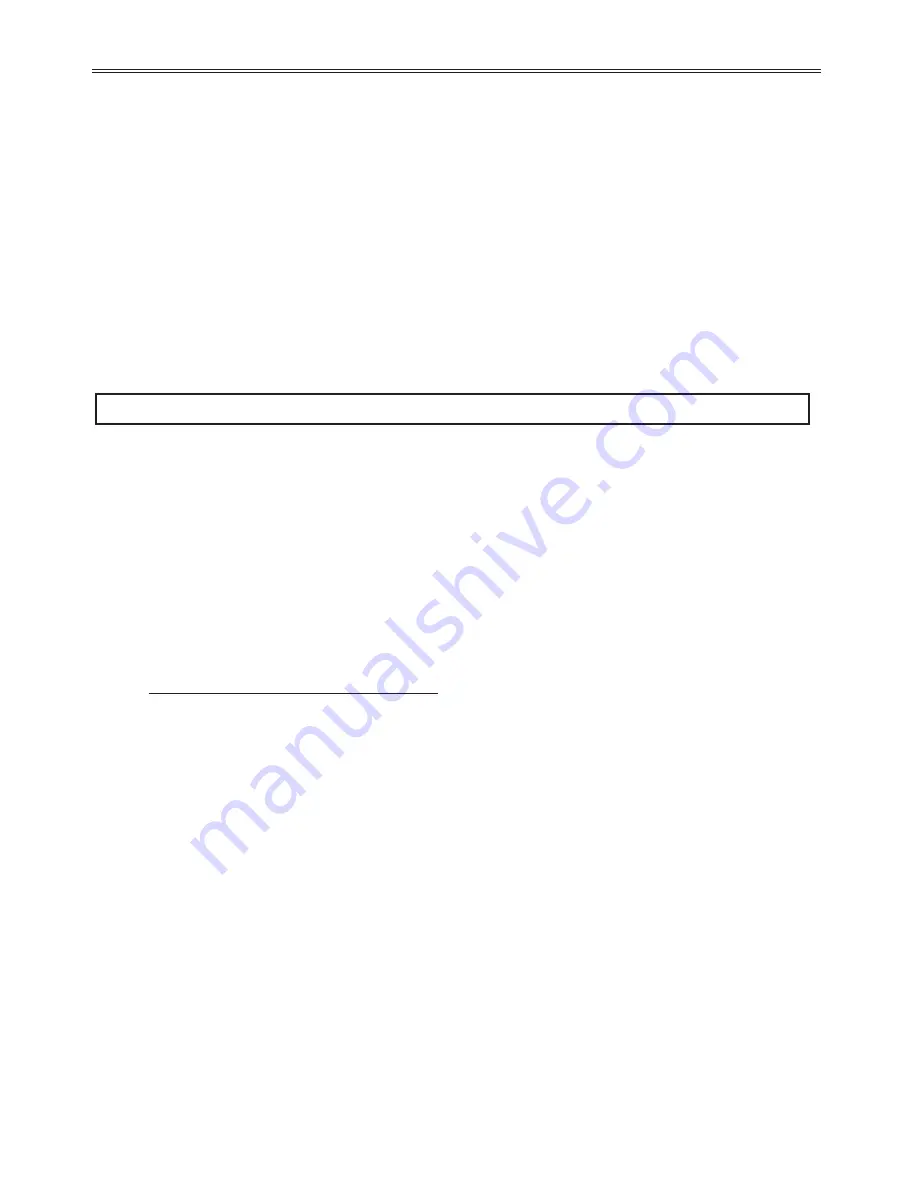
7.5.9
DC Injection Braking Parameters
Brake Level:
The DC Brake Level parameter sets the level of DC current applied to the motor during braking. The desired
brake level is determined by the combination of the system inertia, system friction, and the desired braking
time. If the motor is braking too fast the level should be reduced. If the motor is not braking fast enough the
level should be increased.
Brake Time:
The DC Brake Time parameter sets the time that DC current is applied to the motor. The desired brake time is
determined by the combination of the system inertia, system friction, and the desired braking level. If the
motor is still rotating faster than desired at the end of the brake time increase the brake time if possible. If the
motor stops before the desired brake time has expired decrease the brake time to minimize unnecessary motor
heating.
Brake Delay:
The DC Brake Delay Time is the time delay between when a stop is commanded and the DC braking current
is applied to the motor. This delay allows the residual magnetic field and motor counter EMF to decay before
applying the DC braking current. If a large surge of current is detected when DC braking is first engaged
increase the delay time. If the delay before the braking action begins is too long then decrease the delay time.
In general, low horsepower motors can utilize shorter delays while large horsepower motor may require longer
delays.
Slow Speed Cyclo Converter
7.6
Slow Speed Cyclo Converter
The MX
3
Soft Starter implements a patented Slow Speed algorithm that can be used to rotate a three-phase AC motor, with control of the
stator current, at speeds less than the rated synchronous speed of the motor. The algorithm is used with a standard three-phase six-switch
SCR based soft starter. The advantages of the MX
3
starter algorithm over other "jogging" techniques are that: the low speed motor
rotation is done without any additional hardware such as additional mechanical contactors and/or extra SCRs, the peak phase currents are
reduced compared with other jogging techniques, motor heating is minimized, and higher shaft torque can be generated.
7.6.1
Operation
Slow speed forward and reverse operation is achieved by energizing a digital input that has been programmed to either Slow Speed
Forward or Slow Speed Reverse (refer to the Digital Input Configuration parameters on page 111 for more information). The active
control source (Local Source or Remote Source) must be set to terminal. Slow Speed Start/Stop control is not available from the LCD
keypad. The starter must be in the idle state in order to enter slow speed operation.
Relay outputs can be programmed to energize during slow speed operation (refer to the Relay Output Configuration parameters on page
112 for more information). This feature can be used to disable mechanical brakes or energize clutches during slow speed operation.
Motor Overload Calculations During Slow Speed Operation
During Slow Speed Operation the MX
3
Solid State Motor Overload Protection is fully active. During slow speed operation the Running
Motor overload setting is used.
z
NOTE:
When the motor is operating at slow speeds its cooling capacity can be greatly reduced. Therefore the running time of the
motor at a given current level is dependant on the motor's thermal capacity. Although the Motor OL is active (if it has not been
intentionally disabled) during slow speed operation it is recommended that the motor temperature be monitored if slow speed is used for
long periods of time.
164
7 - THEORY OF OPERATION
Summary of Contents for RediStart MX3 Series
Page 9: ...1 Introduction 1...
Page 15: ...2 Technical Specifications 7...
Page 35: ...3 Installation 27...
Page 61: ...4 Keypad Operation 53...
Page 71: ...5 Parameter Groups 63...
Page 79: ...6 Parameter Description 71...
Page 145: ...7 Theory of Operation 137...
Page 188: ...NOTES 180 7 THEORY OF OPERATION...
Page 189: ...8 Troubleshooting Maintenance 181...
Page 208: ...NOTES 200 8 TROUBLESHOOTING MAINTENANCE...
Page 209: ...Appendices 201...
Page 237: ...Publication History Revision Date ECO 00 12 15 06 Initial Release...