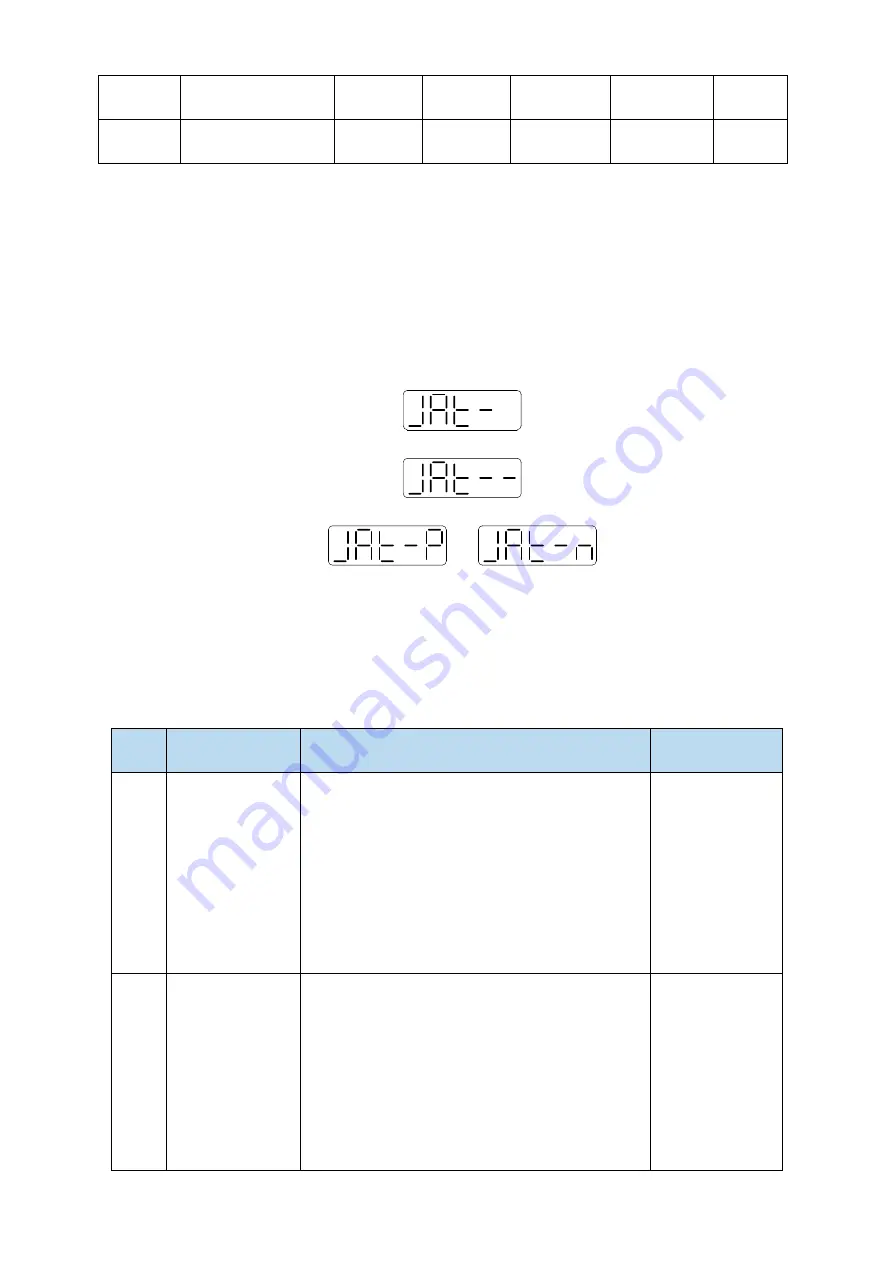
auto-tuning max
speed
P2-18
Inertia identification
initial inertia ratio
500
%
1~20000
Anytime
At once
The recommended parameters of P2-17 are 500 rpm or more. Low instruction speed will lead to
inaccurate identification of inertia ratio.
2. Execute the inertia identification
Before inertia identification, please confirm the direction of servo rotation by using F1-00 jog motion
function. Initial direction of servo operation is determined by INC or DEC at the beginning of inertia
identification.
If the servo jitter is under the adaptive default parameters, please switch to the adaptive large inertia
mode (P2-03.3=1) to ensure the basic smooth operation of the servo and then identify the inertia!
Servo entering parameter F0-07 in BB state:
Press ENTER, servo is enabled:
Press INC or DEC to run forward or reverse (select one of them):
or
At this point, start action, under the condition of P-05 = 0 (initial positive direction), if press INC, then
turn forward and then reverse; if press DEC, turn reverse and then forward. If the inertia identification
is successful, the load inertia ratio is prompted and written to P0-07 automatically after several forward
and reverse operations. If the inertia identification error occurs, the error code will be displayed. Press
STA/ESC key to exit the panel inertia identification operation.
Alarm for inertia identification of panel
Error
code
Meaning
Reasons and solutions
Reasons
Err-1
Motor
Torque
Saturation
①
Initial inertia is too small; in adaptive mode,
switch to large inertia mode P2-03.3=1 or the initial
inertia of inertia identification P2-18 set to 2 times
of the present value.
②
The maximum speed is too high (P2-17), but it is
recommended not to be less than 500 rpm. Low
instruction
speed
will
lead
to
inaccurate
identification of inertia ratio.
③
torque limit too small
(
P3-28/29
)
Initial inertia too
small; Maximum
speed too large;
Torque limit too
small
Err-2
value error is too
large
when
calculating
the
inertia
①
The maximum speed limit is too small (P2-17),
but it is recommended not to be less than 500 rpm.
Low instruction speed will lead to inaccurate
identification of inertia ratio.
②
The presumed inertia trip is too small. It is
suggested that the minimum for P2-15 should no be
less than 50 (0.5 cycles). If the trip is too small, the
identification of inertia ratio will be inaccurate.
③
mechanism friction too large
The
maximum
speed limit is too
small; the travel
is too small; the
friction of the
mechanism is too
large; the overrun
occurs
Содержание DS5L1 Series
Страница 1: ...DS5L1 series servo driver User manual WUXI XINJE ELECTRIC CO LTD Data No SC5 05 20200929 1 0 ...
Страница 2: ......
Страница 6: ......
Страница 33: ...Voltage DC 30V maximum Current SO1 DC 500mA maximum 400W and below servo can support SO others DC 50mA maximum ...
Страница 100: ...3 Set the auto tuning interface 4 Click ok to start inertia identification ...
Страница 106: ...3 set the auto tuning interface ...
Страница 112: ...with higher rigidity 6 Start auto tune 7 Open the servo enable then click ok ...
Страница 169: ...Appendix 9 Torque speed characteristic curve ...
Страница 170: ......