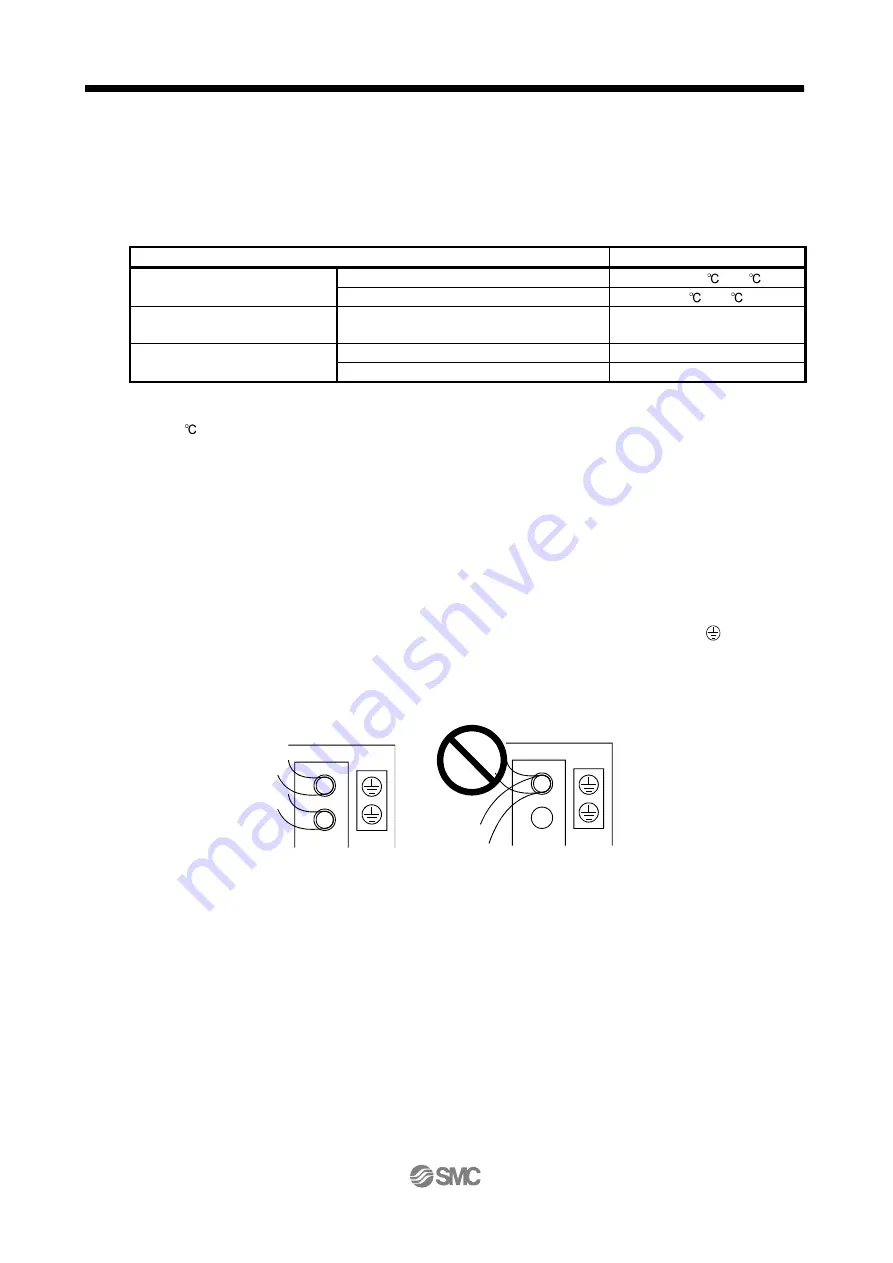
App. - 11
APPENDIX
(3) Environment
(a) Operate the driver at or above the contamination level 2 set forth in IEC/EN60664-1. For this purpose,
install the driver in a control box which is protected against water, oil, carbon, dust, dirt, etc. (IP54).
(b) Use the servo motor under the following environmental conditions.
Environment
Conditions
(Note 1) Ambient temperature
In operation
(Note 2) 0
to 55
Under preservation or under transportation
-20
to 65
Ambient humidity
In operation, under preservation or under
transportation
90%RH or less
Altitude
In operation or under preservation
1000m or lower
Under transportation
10000m or lower
Note 1. The ambient temperature here represents the temperature within the control panel.
2. Close mounting of drivers is possible. In case of mounting drivers closely, bring the ambient temperature within 0 to
45
, or use it at 75% or lower effective load ratio.
(4) Power supply
(a) This driver can be supplied from star-connected supply with earthed neutral point of overvoltage
category III set forth in IEC/EN60664-1. However, when using the neutral point of 400V class for single-
phase supply, a reinforced insulating transformer is required in the power input section.
(b) When supplying interface power from external, use a 24VDC power supply which has been insulation
reinforced in I/O.
(5) Grounding
(a) To prevent an electric shock, always connect the protective earth (PE) terminals (marked
) of the
driver to the protective earth (PE) of the control box.
(b) Do not connect two ground cables to the same protective earth (PE) terminal. Always connect the
cables to the terminals one-to-one.
PE
terminal
PE
terminal
(c) If a leakage current breaker is used to prevent an electric shock, the protective earth (PE) terminals of
the driver must be connected to the corresponding earth terminals.
(6) Wiring and installation
(a) When wiring the CNP1 and CNP2 connectors with the twisted wire, strip its sheath and twist its core. At
this time, take care to avoid a short caused by the loose wires of the core and the adjacent pole. Do not
solder the core as it may cause a contact fault.
(b) Be sure to install the driver on a metallic control panel.