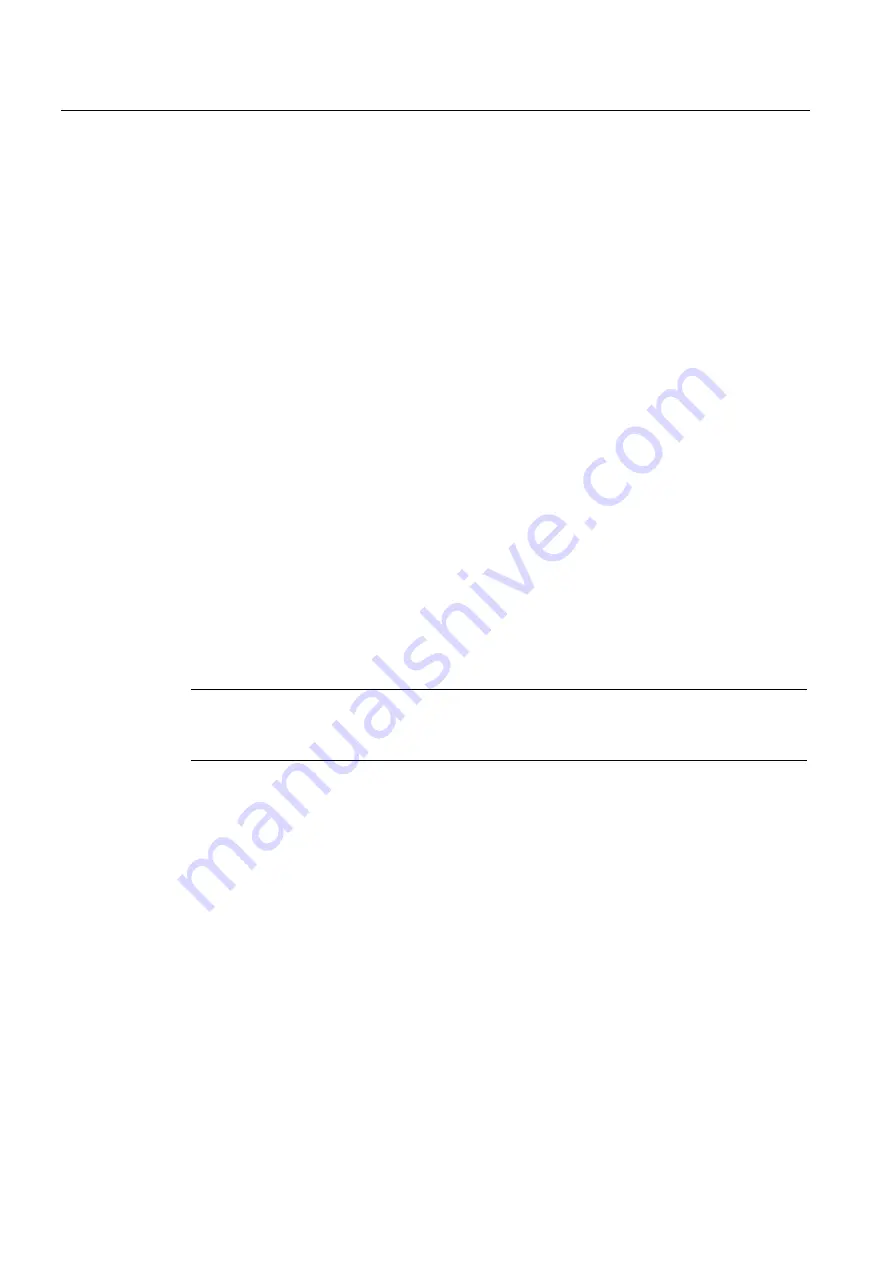
Configuring the fieldbus
6.3 Communication over CANopen
Frequency inverters with Control Units CU230P-2 HVAC, CU230P-2 DP, CU230P-2 CAN
164
Operating Instructions, 01/2011, FW 4.4, A5E02430659B AD
PDO services
The PDO services can be subdivided as follows:
●
Write PDO
●
Read PDO
●
SYNC service
Write PDO
The "Write PDO" service is based on the "push" model. The PDO has exactly one producer.
There can be no consumer, one consumer, or multiple consumers.
Via Write PDO, the producer of the PDO sends the data of the mapped application object to
the individual consumer.
Read PDO
The "Read PDO" service is based on the "pull" model. The PDO has exactly one producer.
There can be one consumer or multiple consumers.
Via Read PDO, the consumer of the PDO receives the data of the mapped application object
from the producer.
SYNC service
The SYNC object is periodically sent from the SYNC producer. The SYNC signal represents
the basic network cycle. The time interval between two SYNC signals is determined in the
master by the standard parameter "Communication cycle time".
In order to ensure CANopen accesses in real-time, the SYNC object has a high priority,
which is defined using the COB ID. This can be changed via p8602 (factory setting = 80hex).
The service runs unconfirmed.
Note
The COB ID of the SYNC object must be set to the same value for all nodes of a bus that
should respond to the SYNC telegram from the master
The COB ID of the SYNC object is defined in object 1005h (p8602).
Содержание SINAMICS G120 CU230P-2
Страница 2: ......