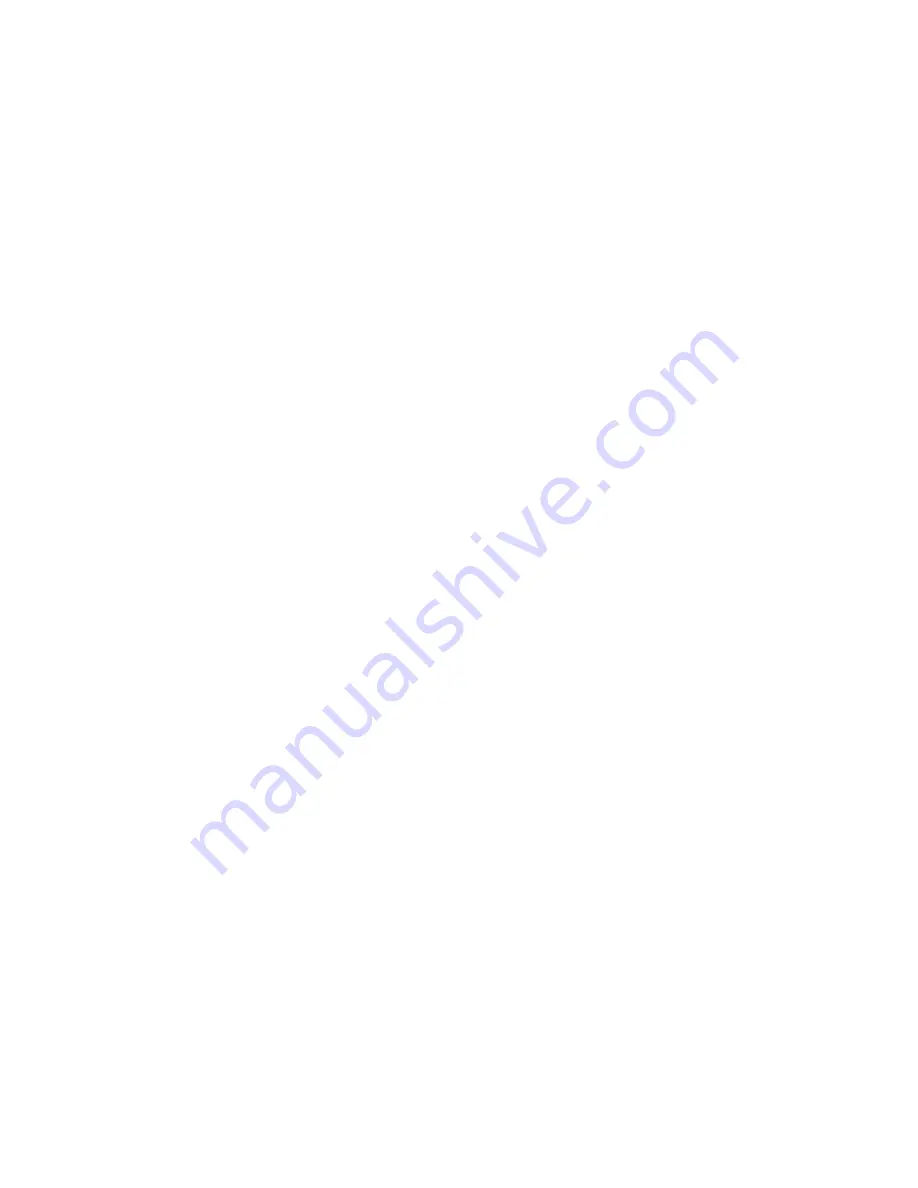
APPENDIX
– Selection and Mounting of Encoder
187
Appendix
Selecting and Mounting of Encoder
Encoder Specification
The HPV 900 Series 2 has connections for an
incremental two-channel quadrature encoder.
For better noise immunity, the HPV 900 Series 2
provides…
an isolated power supply, which separates
the processor power from the encoder
optically isolated encoder signals from the
HPV 900 Series 2’s processor
Encoder Feedback
Supply Voltage:
12VDC or 5VDC
Capacity:
200mA or 400mA
PPR:
600 - 40,000
Maximum Frequency:
300 kHz
Input:
2 channel quadrature
5 or 12 volts dc differential
(A, /A, B, /B) {Z,/Z for
Incremental PM}
Encoder Considerations
Electrical interference and mechanical speed
modulations are common problems that can
result in improper speed feedback getting to the
drive. To help avoid these common problems,
the following electrical and mechanical
considerations are suggested.
IMPORTANT
Proper encoder speed feedback is essential for
a drive to provide proper motor control.
Electrical Considerations
If possible, insulate both the encoder case
and shaft from the motor. For more
information, see Insulating Encoder from
Motor on page 187.
Use twisted pair cable with shield tied to
chassis ground at drive end. For more
information, see Encoder Wiring on page 30.
Use limited slew rate differential line drivers.
For more information, see Differential Line
Drivers on page 189.
Do not allow capacitors from internal
encoder electronics to case. For more
information, see Capacitors from Electronics
to Case on page 190.
Do not exceed the operating specification of
the encoder/drive. For more information, see
Exceeding Operating Specification on page
191.
Use the proper encoder supply voltage and
use the highest possible voltage available
(i.e. HPV 900 Series 2 - 12VDC preferred).
For more information, see Encoder Supply
Voltage on page 191.
Mechanical Considerations
Use direct motor mounting without
couplings. For more information, see Direct
Motor Mounting on page 188.
Use hub or hollow shaft encoder with
concentric motor stub shaft. For more
information, see motor stub shaft on page
188.
If possible, use a mechanical protective
cover for exposed encoders. For more
information, see Encoder Protective Covers
on page 189.
Encoder Mounting
Insulating Encoder from Motor
It is preferred that both the encoder case and
shaft are insulated from the motor, in order to
minimize encoder bearing currents and ground
noise.
There will be PWM electrical noise on the motor
shaft that will take the easiest path to ground. If
the encoder is not electrically isolated from the
motor, this path could be through the encoder
bearings and/or electronics. Encoder bearing
current will reduce the life of the bearings and
create additional ground noise. The solution
would be to electrically isolate both the encoder
shaft and case from the motor.
Insulating the encoder case from the motor also
reduces ground current coupling from the motor
frame to the internal electronics of the encoder.
Ground noise from the motor frame can disturb
the operation of the encoder and propagate
down the connected cable to disturb the
transmission of the encoder signals. (i.e. there
can be coupling from the case to the internal
electronics even though a discrete capacitor is
not present)
Figure 54 shows how to insulate a hollow-shaft
encoder from the motor (similar mounting
hardware and insulating insert can be used for
hub-shaft encoders).
Содержание HPV 900 Series 2
Страница 4: ......
Страница 195: ...APPENDIX Dimensions Mounting Holes Weights 173 Figure 46 Frame 2 Dimensions Mounting Holes and Weight...
Страница 196: ...APPENDIX Dimensions Mounting Holes Weights 174 Figure 47 Frame 3 Dimensions Mounting Holes and Weight...
Страница 197: ...APPENDIX Dimensions Mounting Holes Weights 175 Figure 48 Frame 3 5 Dimensions Mounting Holes and Weight...
Страница 198: ...APPENDIX Dimensions Mounting Holes Weights 176 Figure 49 Frame 4 Dimensions Mounting Holes and Weight...
Страница 199: ...APPENDIX Dimensions Mounting Holes Weights 177 Figure 50 Frame 5 Dimensions Mounting Holes and Weight...
Страница 227: ...205 Z Z MARKER LOST 150 Zero Speed Level parameter 47 Zero Speed logic output 105 Zero Speed Time parameter 47...
Страница 228: ......
Страница 229: ......