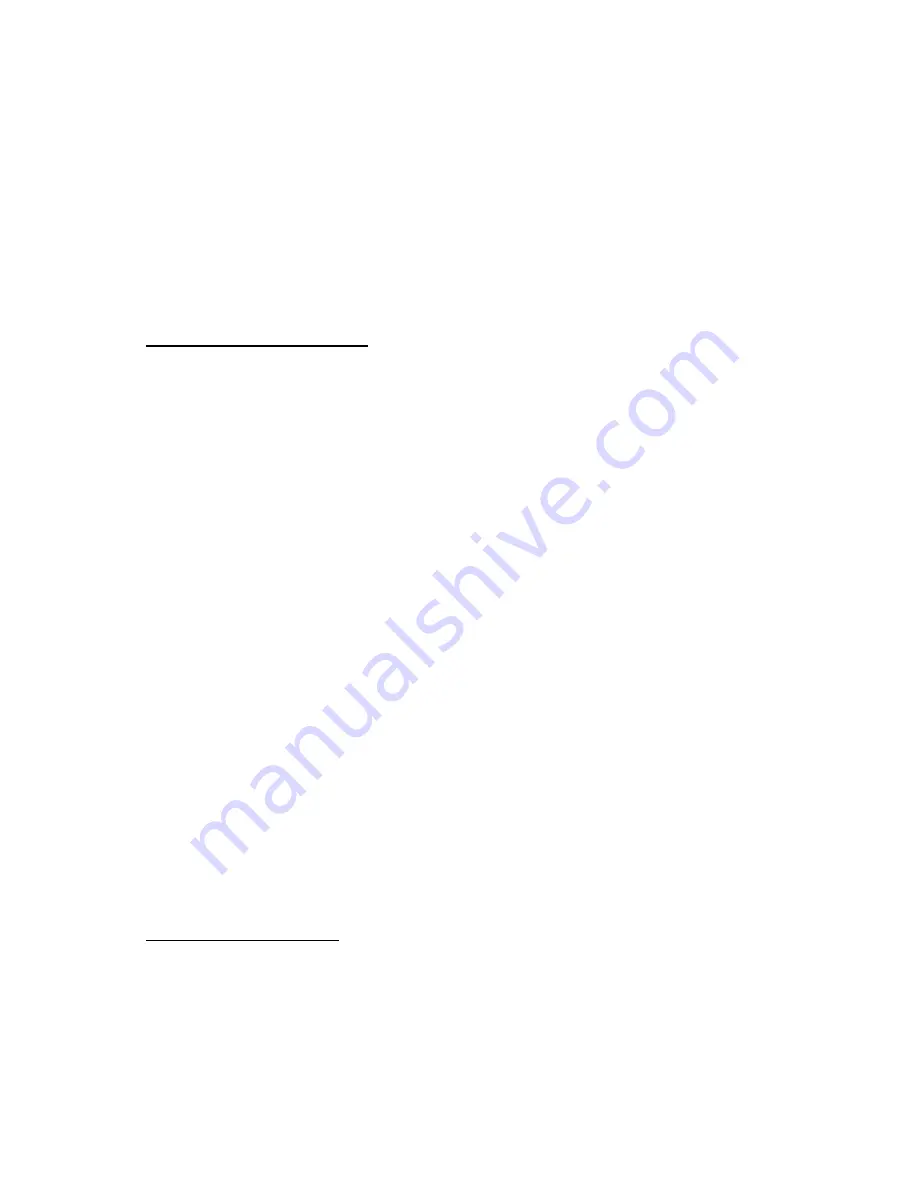
xii
Scroll to U10 menu
– ROTOR ALIGNMENT and change the parameter ALIGNMENT
from DISABLED to ENABLED
Scroll to A5 menu and to the parameter ENCODER ANG OFST press enter and manually
enter the ‘known’ offset value – the motor should then be able to run – attempt this on test
controls.
If the rotor alignment is not known as is the case on the majority of motors/encoders you will
have to perform a physical alignment. The preferred way of doing this is a rotating alignment
under no load
(before ropes are fitted or with the ropes lifted and clear of the sheave)
if
your ropes are already fitted or it’s an existing installation skip to option 3.
OPTION 2
– Rotating alignment
Clear any active faults in the drive in the F1 menu (and verify they have cleared)
Scroll to U10 menu
– ROTOR ALIGNMENT and change the parameter ALIGNMENT
from DISABLED to ENABLED
Also in the U10 alignment menu ensure the parameter ALIGNMENT METHOD is set to
OPEN LOOP
Next change the parameter BEGIN ALIGNMENT to ON RUN
The drive is now ready for alignment, so simply press and hold your RUN, RUN UP, or
RUN DOWN buttons and you should see the brake lift, the motor should rotate for about 4
seconds smoothly then stop on its own accord
– it’s important that the test buttons remain
fully pressed for the duration of the tune, if the buttons are released for any reason you
will need to restart this whole procedure. When the motor has stopped and the run LED
on the drives operator has extinguished you may release your buttons
Assuming this went successfully the drive will have established the encoders position
relative to the motor poles and automatically saved this value, it can be checked in the
drives A5 menu (parameter ENCODER ANG OFST).
Attempt to run on inspection control to verify.
NOTE:
If drive ENCODER ANG OFST is set to a number other than 30000, then the
alignment was most likely performed
If this procedure didn’t complete successfully and a fault was displayed, please refer to
the fault section of this supplement or the drives technical manual for diagnostic
information
Option 3
– Static alignment
If it is not possible to perform a rotating alignment the encoder angle offset can be obtained by
performing a ‘static’ alignment where the brake is not lifted.
To perform this:
Clear any active faults in the drive in the F1 menu (and verify they have cleared)
Scroll to U10 menu
– ROTOR ALIGNMENT and change the parameter ALIGNMENT
from DISABLED to ENABLED
Содержание HPV 900 Series 2
Страница 4: ......
Страница 195: ...APPENDIX Dimensions Mounting Holes Weights 173 Figure 46 Frame 2 Dimensions Mounting Holes and Weight...
Страница 196: ...APPENDIX Dimensions Mounting Holes Weights 174 Figure 47 Frame 3 Dimensions Mounting Holes and Weight...
Страница 197: ...APPENDIX Dimensions Mounting Holes Weights 175 Figure 48 Frame 3 5 Dimensions Mounting Holes and Weight...
Страница 198: ...APPENDIX Dimensions Mounting Holes Weights 176 Figure 49 Frame 4 Dimensions Mounting Holes and Weight...
Страница 199: ...APPENDIX Dimensions Mounting Holes Weights 177 Figure 50 Frame 5 Dimensions Mounting Holes and Weight...
Страница 227: ...205 Z Z MARKER LOST 150 Zero Speed Level parameter 47 Zero Speed logic output 105 Zero Speed Time parameter 47...
Страница 228: ......
Страница 229: ......