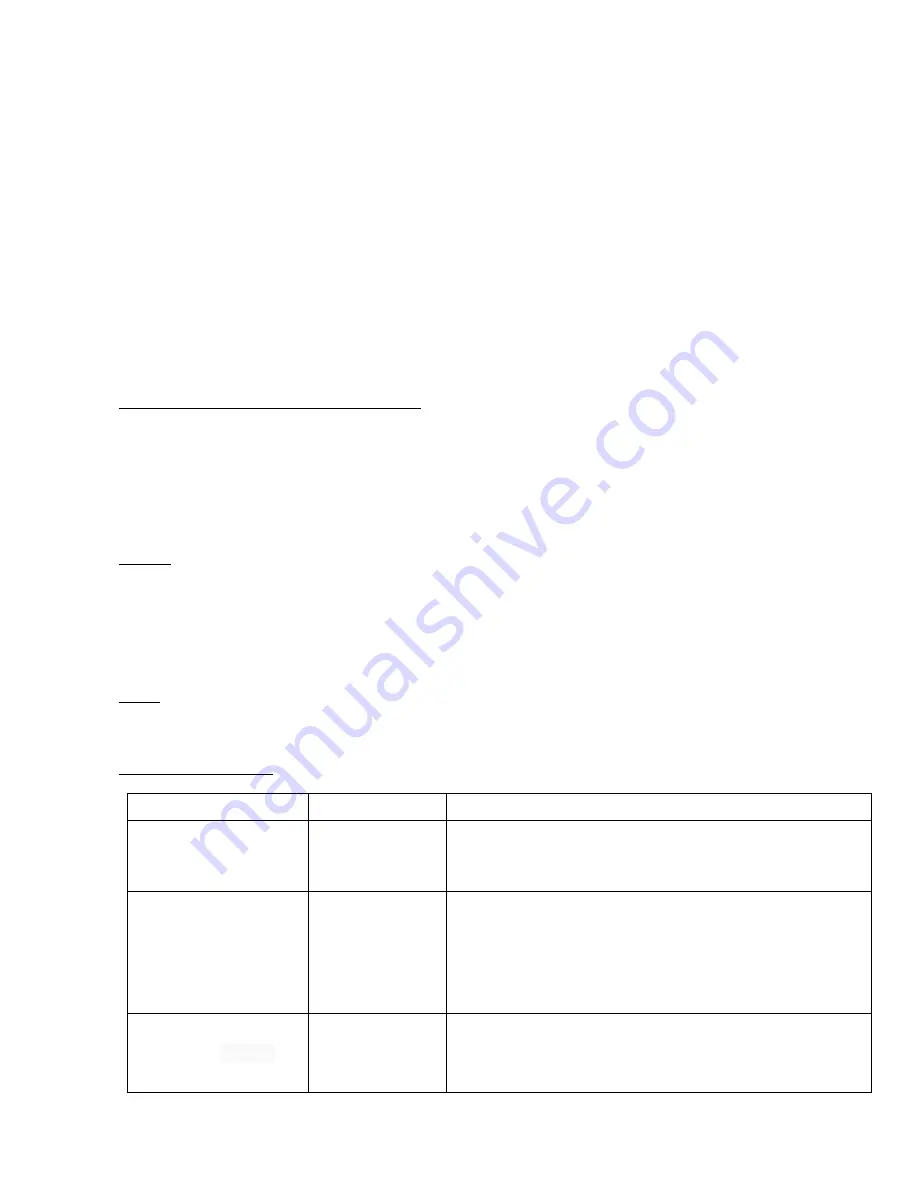
APPENDIX
– Safe-Off
162
Appendix
Brake Monitoring
To summarize the feature, the Brake Monitoring feature in the drive is used to monitor up to two brake
pick switches, and determine that their operation is as expected.
1. The drive can monitor up to two brake switches with logic inputs and a logic output can be
configured to annunciate a Brake Pick Fault
2.
In the event of a Brake Pick Fault, ‘Brake Pick Fault Enable’ will change from ‘Enable’ to
‘Active’ and the fault status will latch. The fault can only be reset by adjusting the Brake Pick
Fault Enable parameter back to Enable. This is to ensure it can only be reset by a competent
person. A power cycle will not reset this fault.
3. If a Brake Pick Fault occurs, and the user tries to disable the Brake Pick Fault Enable function,
it will revert back to Active
Enabling the Brake Monitoring feature
This feature is enabled by setting ‘Brake Pick Fault Enable’ in the C1 menu of the drive to ‘Enable’. An
output in the C3 menu (Logic output or Relay Output) should be configured to ‘Brake Pick Flt’ to be
monitored by the controller. Inputs should be configured in the C2 menu for however many Brake Pick
switches are available. Presently there are inputs for up to two brake pick switches. The switches
should be normally open, and wired into inpu
ts configured to ‘Mech Brake Pick 1’ and ‘Mech Brake
Pick 2’.
Outputs
This guide will assume the brake lift is controlled by the drive with a logic output for ‘Brake Pick’ or
‘Autobrake’, however the timings will still apply if no output is configured to those parameters.
An output will be configured to ‘Brake Pick Flt’ for the controller to monitor the status of the Brake Pick
Fault.
This feature will declare a ‘Brake Pick Flt’ output if the Brake Pick Inputs do not change as expected
within ‘Brake Pick Time’ after a Brake Pick/Autobrake output.
Inputs
Up to two logic inputs can be configured to monitor normally closed brake switches. One input should
be used for each switch.
Parameter Settings
The parameters for the Brake Monitoring function should be configured as follows:
Parameter Name
Setting
Function
Relay Coil 2* (C3)
Brake Pick
Or
Autobrake
This is the output configured to control the brake. Following
the change in this output, the drive will expect a change in
the ‘Mech Brake Pick’ Logic inputs.
Logic Output 4* (C3)
Brake Pick Flt
Provides feedback to the car controller of the status of the
Brake Pick Fault.
This fault persists through fault resets and power cycles, and
can only be reset by a competent person using the C1 menu.
The status of this output can be monitored in the D1 menu
under Logic Outputs as a 1 or 0 as with any other output.
Logic Input 7
† (C2)
Mech Brk Pick 1
Input for a normally open brake switch. The drive monitors
this input, and if it doesn’t switch as expected after a change
in Brake Pick/Autobrake output, it will declare ‘Brake Pick
Fault 1’
Содержание HPV 900 Series 2
Страница 4: ......
Страница 195: ...APPENDIX Dimensions Mounting Holes Weights 173 Figure 46 Frame 2 Dimensions Mounting Holes and Weight...
Страница 196: ...APPENDIX Dimensions Mounting Holes Weights 174 Figure 47 Frame 3 Dimensions Mounting Holes and Weight...
Страница 197: ...APPENDIX Dimensions Mounting Holes Weights 175 Figure 48 Frame 3 5 Dimensions Mounting Holes and Weight...
Страница 198: ...APPENDIX Dimensions Mounting Holes Weights 176 Figure 49 Frame 4 Dimensions Mounting Holes and Weight...
Страница 199: ...APPENDIX Dimensions Mounting Holes Weights 177 Figure 50 Frame 5 Dimensions Mounting Holes and Weight...
Страница 227: ...205 Z Z MARKER LOST 150 Zero Speed Level parameter 47 Zero Speed logic output 105 Zero Speed Time parameter 47...
Страница 228: ......
Страница 229: ......