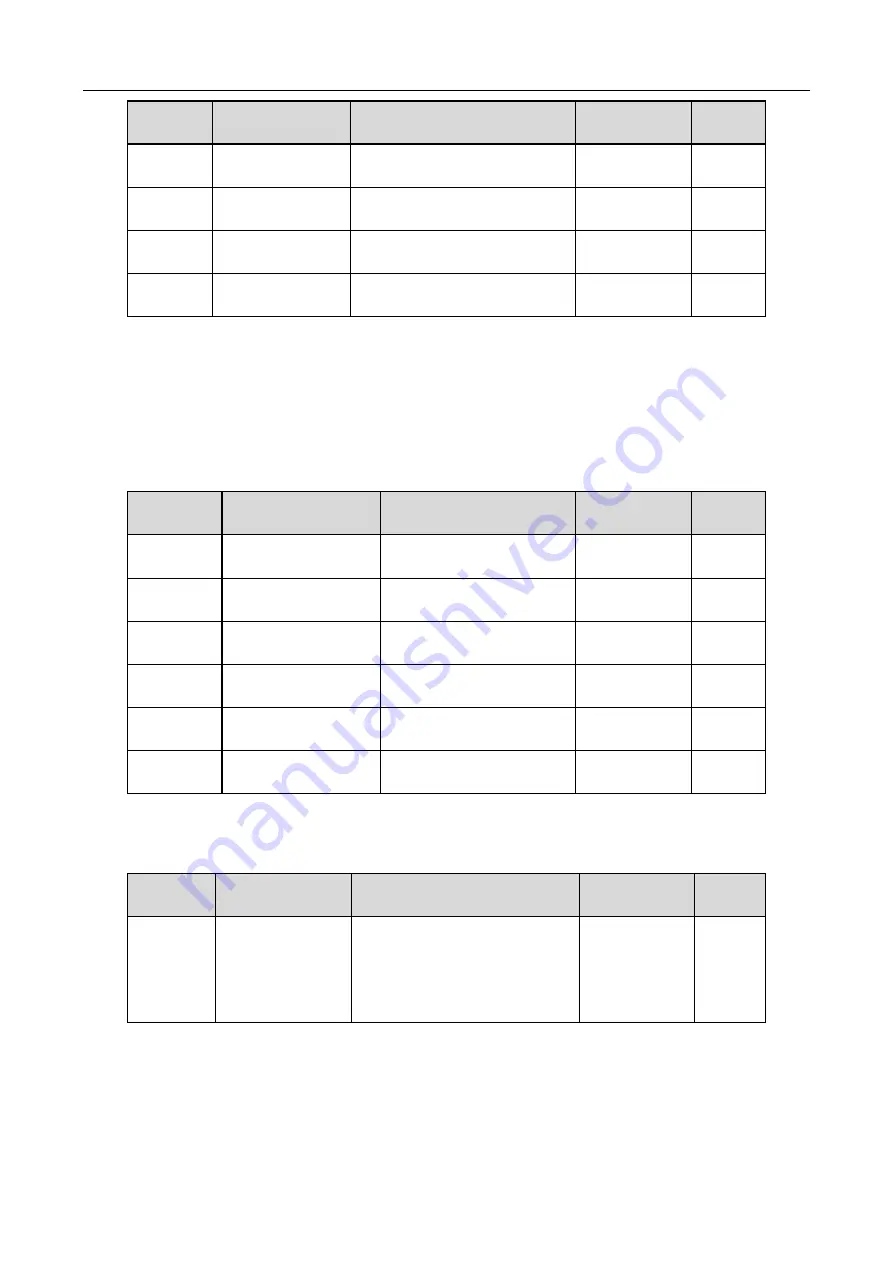
Goodrive3000 series medium voltage VFD
Goodrive3000 inverter
-71-
Function
code
Name
Description
Setting range
Default
P02.16
Rated frequency of
SM 1
0.01Hz
–P00.03 (Max. output
frequency)
0.01
–P00.03
50.00Hz
P02.17
Number of pole pairs
of SM 1
1
–50
1
–50
2
P02.18
Rated voltage of SM 1 0
–4000V
0
–4000
Model
depended
P02.19
Rated current of SM 1 0.8
–6000.0A
0.8
–6000.0
Model
depended
The function codes are used to set the parameters for the controlled SM.
To ensure the control performance, set P02.15
–P02.19 correctly according to the information on the nameplate of the SM.
The VFD provides the parameter autotuning function. Whether parameter autotuning can be performed properly depends
on the settings of the motor nameplate parameters.
In addition, you need to configure a motor according to the standard motor configuration of the VFD. If the power of the
motor is greatly different from that of the standard motor configuration, the control performance of the VFD degrades
significantly.
Function
code
Name
Description
Setting range
Default
P02.20
Stator resistance of SM 1 0.001
–65.535Ω
0.001
–65.535
Model
depended
P02.21
Direct-axis inductance of
SM 1
0.01
–655.35mH
0.01
–655.35
Model
depended
P02.22
Quadrature-axis
inductance of SM 1
0.01
–655.35mH
0.01
–655.35
Model
depended
P02.23
Counter-emf constant of
SM 1
0
–10000
0
–10000
300
P02.24
Initial pole position of SM
1
0x0000
–0xFFFF
0x0000
–0xFFFF
0x0000
P02.25
Identification current of
SM 1
0%
–50% (of the motor rated
current)
0
–50
10%
Note: Do not modify these parameters unless it is necessary.
After motor parameter autotuning is properly performed, the values of P02.20
–P02.25 are automatically updated. These
parameters are the benchmark parameters for high-performance vector control, directly affecting the control performance.
Function
code
Name
Description
Setting range
Default
P02.26
Overload protection
of motor 1
0: No protection
1: Common motor (with low-speed
compensation)
2: Frequency-variable motor (without
low-speed compensation)
0
–2
2
0: No protection
1: Common motor protection (with low-speed compensation). As the cooling effect of a common motor is degraded at low
speed running, the corresponding electronic thermal protection value needs to be adjusted properly, the low
compensation indicates lowering the overload protection threshold of the motor whose running frequency is lower than
30Hz.
2: Variable-frequency motor protection (without low speed compensation). Because the heat dissipation function for a