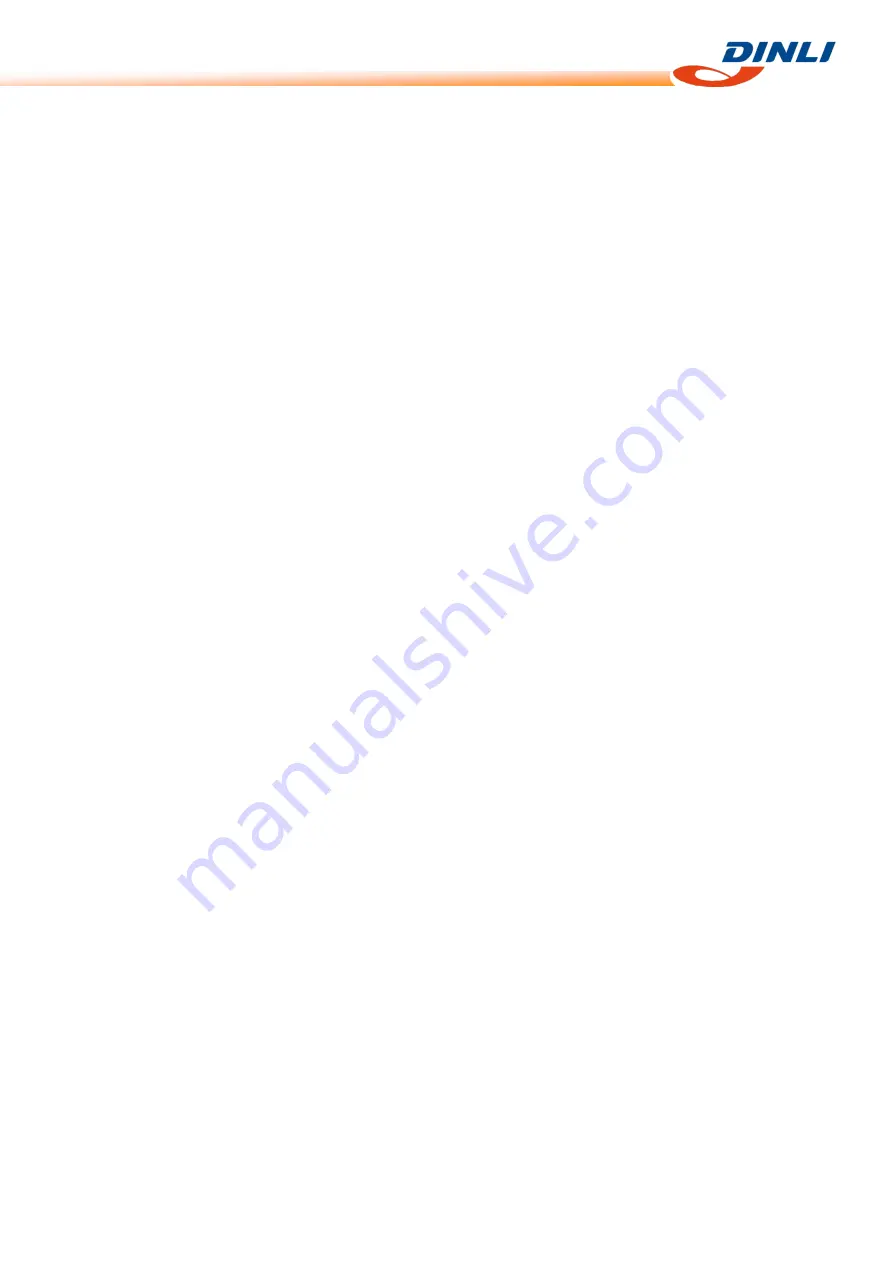
【
1-3
】
GENERAL INFORMATION
(6)
Force
Common
sense
should
dictate
how
much
force
is
necessary
in
assembly
and
disassembly.
If
a
part
seems
especially
difficult
to
remove
or
install,
stop
and
examine
what
may
be
causing
the
problem.
Whenever
tapping
is
necessary,
tap
lightly
using
a
wooden
or
plastic
‐
faced
mallet.
Use
an
impact
driver
for
screws
(particularly
for
the
removing
screws
held
by
non
‐
permanent
locking
agent)
in
order
to
avoid
damaging
the
screw
heads.
(7)
Edges
Watch
for
sharp
edges,
as
they
could
cause
injury
through
careless
handing,
especially
during
major
engine
disassembly
and
assembly.
Use
a
clean
piece
of
thick
cloth
when
lifting
the
engine
or
turning
it
over.
(8)
High
‐
Flash
Point
Solvent
A
high
‐
Flash
point
solvent
is
recommended
to
reduce
fire
danger.
A
commercial
solvent
commonly
available
in
North
America
is
standard
solvent
(generic
name).
Always
follow
manufacturer
and
container
directions
regarding
the
use
of
any
solvent.
(9)
Gasket,
O
‐
Ring
Replace
a
gasket
or
an
O
‐
ring
with
a
new
part
when
disassembling.
Remove
any
foreign
matter
from
the
mating
surface
of
the
gasket
or
O
‐
ring
to
ensure
a
perfectly
smooth
surface
to
prevent
oil
or
compression
leaks.
(10)
Liquid
Gasket,
Locking
Agent
Clean
and
prepare
surfaces
where
liquid
gasket
or
non
‐
permanent
locking
agent
will
be
used.
Apply
them
sparingly.
Excessive
amount
may
block
engine
oil
passages
and
cause
serious
damage.
(11)
Press
When
using
a
press
or
driver
to
install
a
part
such
as
a
wheel
bearing,
apply
a
small
amount
of
oil
to
the
area
where
the
two
parts
come
in
contact
to
ensure
a
smooth
fit.
(12)
Ball
Bearing
and
Needle
Bearing
Do
not
remove
a
ball
bearing
or
a
needle
bearing
unless
it
is
absolutely
necessary.
Replace
any
ball
or
needle
bearings
that
were
removed
with
new
ones.
Install
bearings
with
the
manufacturer
and
size
marks
facing
out,
applying
pressure
evenly
with
a
suitable
driver.
Apply
force
only
to
the
end
of
the
race
that
contacts
the
press
fit
portion,
and
press
it
evenly
over
the
base
component.
(13)
Oil
Seal
and
Grease
Seal
Replace
any
oil
or
grease
seals
that
were
removed
with
new
ones,
as
removal
generally
damages
seals.
Oil
or
grease
seals
should
be
pressed
into
place
using
a
suitable
driver,
applying
a
force
uniformly
to
the
end
of
seal
until
the
face
of
the
seal
is
even
with
the
end
of
the
hole,
unless
instructed
otherwise.
When
pressing
in
an
oil
or
grease
seal,
which
has
manufacturer’s
marks,
press
it
in
with
the
marks
facing
out.
(14)
Cir
‐
clip,
Retaining
Ring,
and
Cotter
Pin
Содержание DL-702 2008
Страница 1: ...FOREWORD INDEX 0 0...
Страница 41: ...3 11 BRAKE...
Страница 180: ...6 70 ENGINE Install the starter motor...
Страница 201: ...7 21 COOLING AND LUBRICATION SYSTEM Engine Lubrication System Chart...
Страница 202: ...7 22 COOLING AND LUBRICATION SYSTEM Engine Lubrication System 1 2 3 1 2 3 1 2 3...
Страница 203: ...7 23 COOLING AND LUBRICATION SYSTEM 1 2 3...
Страница 205: ...7 2 ELECTRICAL SYSTEM Fuses 7 30 Main Fuse Removal 7 30 Fuse Inspection 7 30 Switches 7 31 Wiring Diagram 7 32...
Страница 235: ...7 32 ELECTRICAL SYSTEM Wiring Diagram...
Страница 236: ...7 33 ELECTRICAL SYSTEM Wiring Diagram...
Страница 237: ...7 34 7 34 ELECTRICAL SYSTEM ELECTRICAL SYSTEM...
Страница 238: ...7 35 ELECTRICAL SYSTEM NOTE...
Страница 240: ...9 2 PERIODIC MAINTENANCE...
Страница 246: ...9 8 PERIODIC MAINTENANCE Intake Side...
Страница 247: ...9 9 PERIODIC MAINTENANCE Exhaust Side Side...
Страница 270: ...9 32 PERIODIC MAINTENANCE 1 2 3 4 18 19 12 16 17 21 13 14 15 22 23 5 6 7 8 9 12 10 11 20...