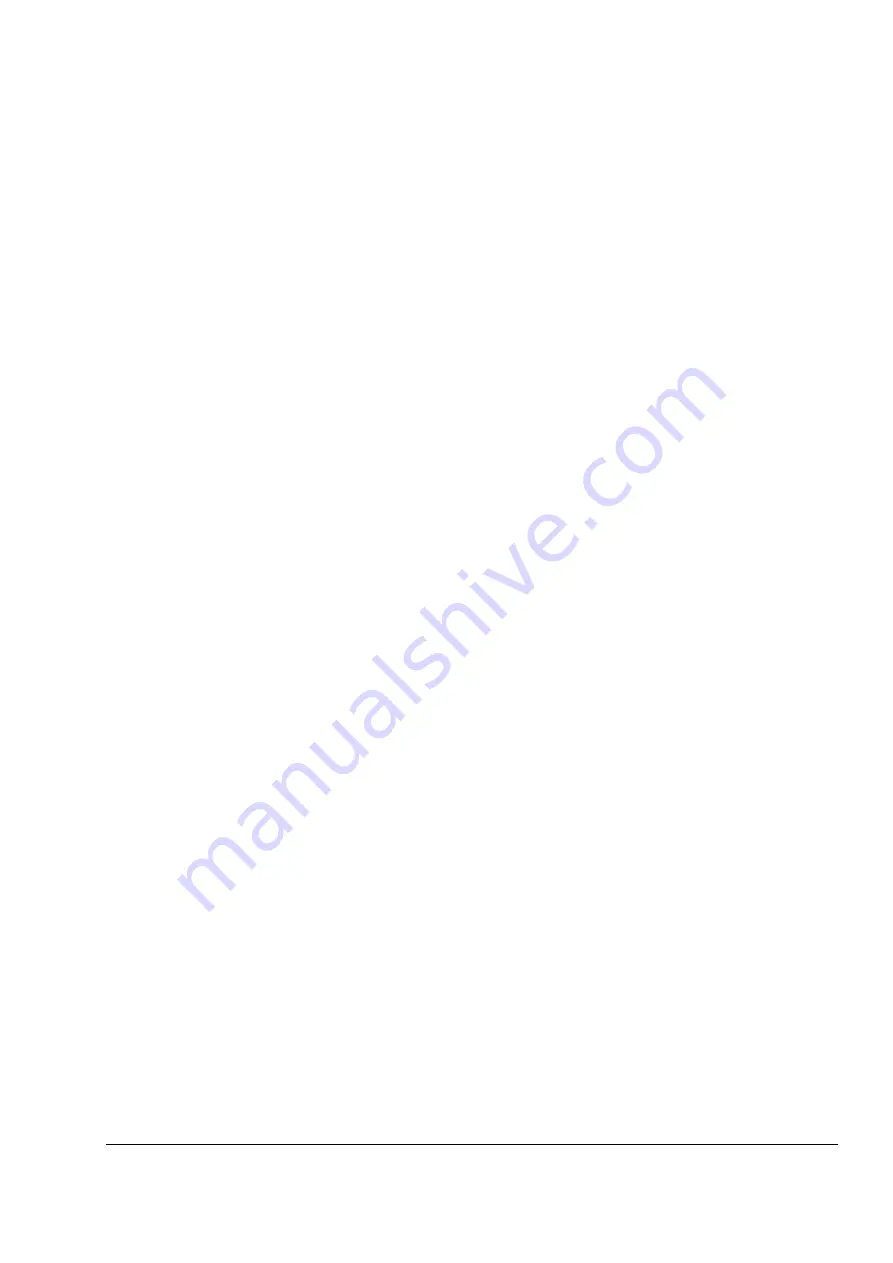
Drive control and features
71
Cyclic position correction
Cyclic position correction functions are used to change or correct the system
position continuously according to data measured by external probe signals, for
example, if there is play in the machinery. The cyclic position correction functions
always need an external probe (or probes) to operate. By means of a programmable
bit pointer, the probes can be configured to use digital inputs DI1 and DI2 of the
encoder interface with different triggering conditions (such as falling or rising edge)
or the digital inputs of the drive control board unit as trigger sources.
The cyclic position correction functions use the probe positions in the correction
calculations in two ways:
• as an actual position latch to correct the drive actual position (
)
• as a master reference latch to correct the drive synchron reference position (
).
To enable cyclic position correction, the following settings must be considered:
• Cyclic correction mode (
• Probe positions (
)
• Triggering conditions (
)
• Maximum allowed correction (
)
• Programmable bit pointer (
,
)
There are five different cyclic position correction functions available:
• CORR ACT POS: Drive actual position correction (Probe 1 used for actual
position latch).
• CORR MAST REF: Synchronised master drive reference correction (Probe 1
used for master position reference latch).
• CORR M/F DIST: Master and follower distance correction. The drive
synchronised master reference and actual position are both corrected (Probe 1
used for actual position latch and probe 2 for master position reference latch).
• 1 PROBE DIST: Drive actual position correction according to the distance
between two consecutive latches from one probe (Probe 1 used for actual
position latch).
• 2 PROBE DIST: Drive actual position correction according to the distance
between two latches (Probe 1 and probe 2 both used for actual position latch).
When enabled, cyclic correction waits until the triggering conditions of the probes
are fulfilled. The encoder positions are then latched (saved) into
and
. If there is deviation between probe position
and measured position, a correction is carried out. The deviation (shown by
) is added to synchronisation error
corrected using the position profile generator and dynamic limiter parameters. The
next correction can be started after the previous correction has been successfully
carried out.
If cyclic correction is configured to use two probes, the correction is done after both
latches have been received. If multiple latches are received from one probe, the last-
received latch is used in the correction calculation.
Содержание ACSM1 Series
Страница 1: ...ABB motion control drives Firmware manual ACSM1 motion control program ...
Страница 4: ......
Страница 34: ...Drive programming using PC tools 34 ...
Страница 86: ...Drive control and features 86 ...
Страница 265: ...Parameters and firmware blocks 265 1 100 us 100 µs 2 1 ms 1 ms 3 50 ms 50 ms ...
Страница 302: ...Parameter data 302 ...
Страница 422: ...Application program template 422 ...
Страница 430: ...Appendix A Fieldbus control 430 ...
Страница 500: ...Appendix D Application examples 500 ...
Страница 508: ...Appendix E Control chain and drive logic diagrams 508 ...
Страница 510: ...3AFE68848270 REV H EN 2015 06 26 Contact us www abb com drives www abb com drivespartners ...