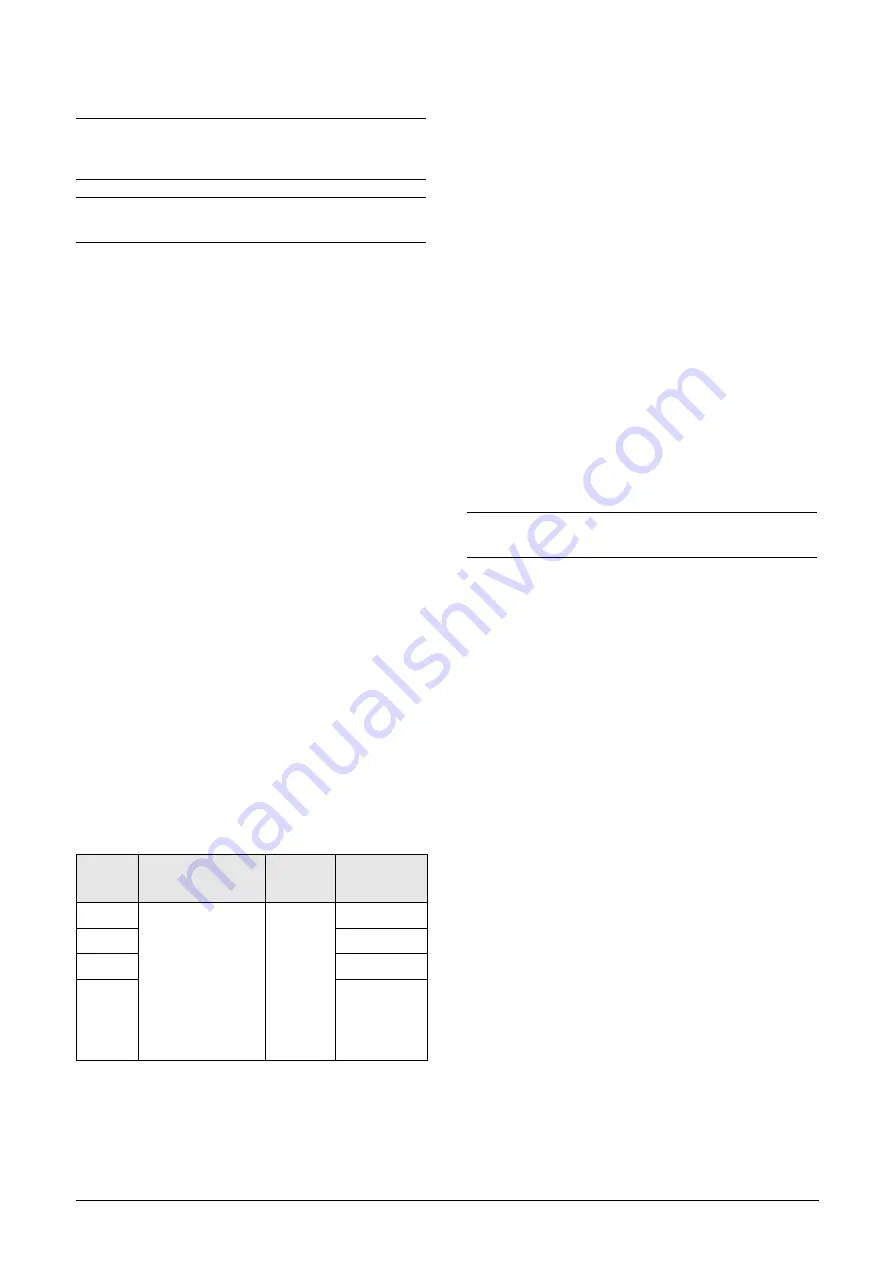
CG Drives & Automation, 01-5326-01r3b
C
Control Connections
45
4.5.2 Types of control signals
Always make a distinction between the different types of
signals. Because the different types of signals can adversely
affect each other, use a separate cable for each type. This is
often more practical because, for example, the cable from a
pressure sensor may be connected directly to the AC drive.
We can distinguish between the following types of control
signals:
Analogue inputs
Voltage or current signals, (0-10 V, 0/4-20 mA) normally
used as control signals for speed, torque and PID feedback
signals.
Analogue outputs
Voltage or current signals, (0-10 V, 0/4-20 mA) which
change slowly or only occasionally in value. In general, these
are control or measurement signals.
Digital
Voltage or current signals (0-10 V, 0-24 V, 0/4-20 mA)
which can have only two values (high or low) and only
occasionally change in value.
Data
Usually voltage signals (0-5 V, 0-10 V) which change rapidly
and at a high frequency, generally data signals such as
RS232, RS485, Profibus, etc.
Relay
Relay contacts (0-250 VAC) can switch highly inductive
loads (auxiliary relay, lamp, valve, brake, etc.).
Example:
The relay output from a AC drive which controls an
auxiliary relay can, at the moment of switching, form a
source of interference (emission) for a measurement signal
from, for example, a pressure sensor. Therefore it is advised
to separate wiring and screening to reduce disturbances.
4.5.3 Screening
For all signal cables the best results are obtained if the
screening is connected to both ends: the AC drive side and
at the source (e.g. PLC or computer). See Fig. 53
.
It is strongly recommended that the signal cables be allowed
to cross mains and motor cables at a 90
°
angle. Do not let
the signal cable go in parallel with the mains and motor
cable.
4.5.4 Single-ended or double-ended
connection?
In principle, the same measures applied to motor cables
must be applied to all control signal cables, in accordance
with the EMC-Directives.
For all signal cables as mentioned in section 4.5.2 the best
results are obtained if the screening is connected to both
ends. See Fig. 53
.
NOTE: The screening of control signal cables is
necessary to comply with the immunity levels given in
the EMC Directive (it reduces the noise level).
NOTE: Control cables must be separated from motor and
mains cables.
Signal
type
Maximum wire size
Tightening
torque
Cable type
Analogue Rigid cable:
0.14-2.5 mm
2
(AWG 26 - 14)
Flexible cable:
0.14-1.5 mm
2
(AWG 26 - 16)
Cable with ferrule:
0.25-1.5 mm
2
(AWG 24 - 16)
0.5 Nm
(4.4 LB-in)
Screened
Digital
Screened
Data
Screened
Relay
Not screened
NOTE: Each installation must be examined carefully
before applying the proper EMC measurements.
9(0R'ULYH 96, 9(0 U
Summary of Contents for VEMoDRIVE VSI 2.0 HD
Page 1: ...Frequency converter VEMoDRIVE VSI 2 0 HD Instruction manual 01 5326 01 04 2018...
Page 2: ......
Page 4: ......
Page 40: ...38 Installation CG Drives Automation 01 5326 01r3b 9 0R ULYH 96 9 0 U...
Page 52: ...50 Getting Started CG Drives Automation 01 5326 01r3b 9 0R ULYH 96 9 0 U...
Page 64: ...62 EMC and standards CG Drives Automation 01 5326 01r3b 9 0R ULYH 96 9 0 U...
Page 142: ...140 Functional Description CG Drives Automation 01 5326 01r3b 9 0R ULYH 96 9 0 U...
Page 198: ...196 CG Drives Automation 01 5326 01r3b 9 0R ULYH 96 9 0 U...
Page 232: ...230 Technical Data CG Drives Automation 01 5326 01r3b 9 0R ULYH 96 9 0 U...
Page 238: ...236 Menu List CG Drives Automation 01 5326 01r3b 9 0R ULYH 96 9 0 U...
Page 243: ...241 9 0R ULYH 96 9 0 U...