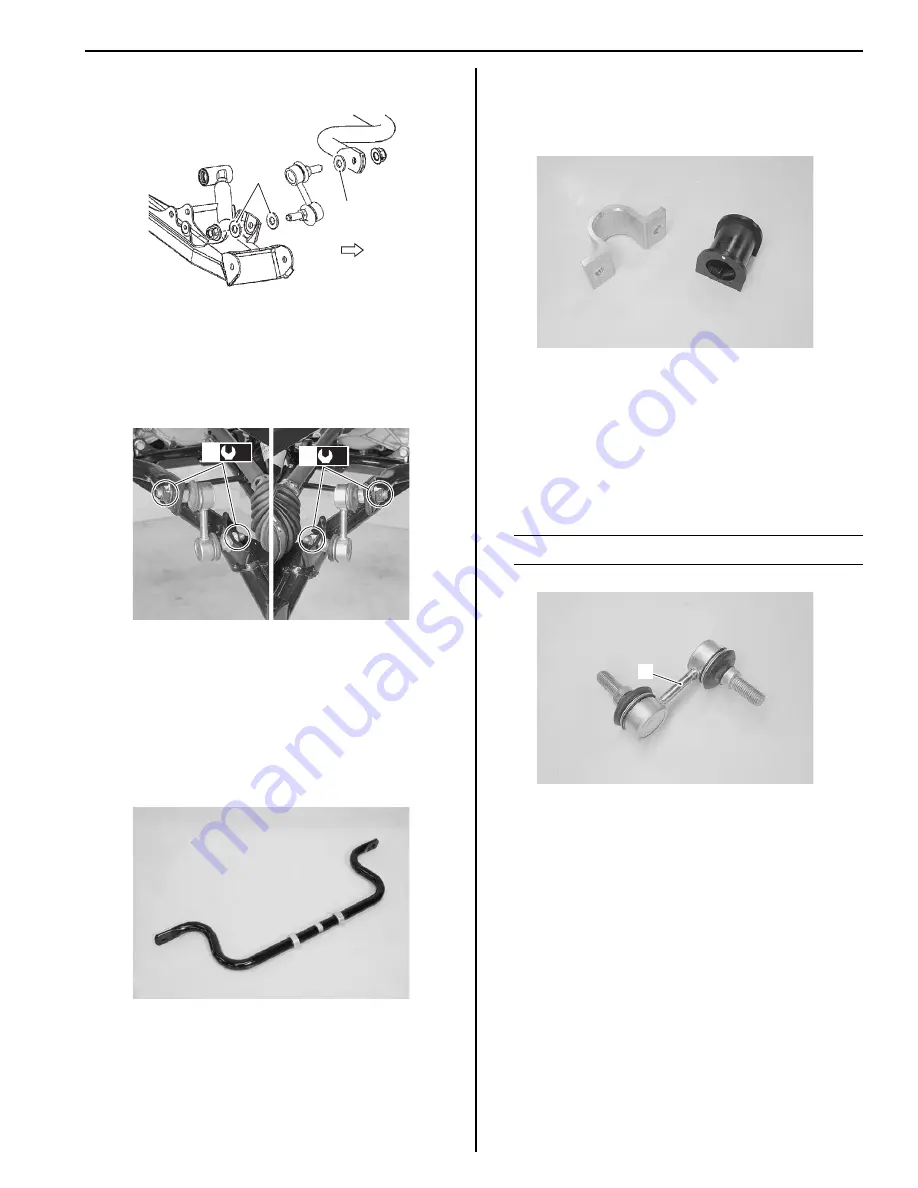
Rear Suspension: 2C-16
• Install the washers (1) as shown.
• Tighten the stabilizer joint nuts (2) to the specified
torque.
Tightening torque
Rear stabilizer joint nut (a): 60 N·m (6.0 kgf-m,
43.5 lbf-ft)
Stabilizer Parts Inspection
B931H22306016
Refer to “Rear Stabilizer Removal and Installation
(Page 2C-15)”.
Stabilizer Bar
Inspect for damage or deformation. If any defects are
found, replace the stabilizer bar with a new one.
Stabilizer Bushing / Plate
Inspect the bushing and plate for wear or damage. If any
defects are found, replace the bushing and/or plate with
a new one.
Stabilizer Joint
Inspect the stabilizer joint for wear or damage. If any
defects are found, replace the stabilizer joint with a new
one.
Inspect the stabilizer joint smooth movement. If there are
any abnormalities, replace the stabilizer joint with a new
one.
NOTE
Stabilizer joint (1) cannot be disassembled.
1
1
FWD
I931H1230059-02
(a)
2
(a)
2
I931H1230052-01
I931H1230053-01
I931H1230054-01
1
I931H1230055-01
Summary of Contents for 2009 LT-A500XP
Page 2: ......
Page 4: ......
Page 14: ...00 9 Precautions ...
Page 224: ...1E 3 Engine Lubrication System EXHAUST SIDE INTAKE SIDE I931H1150003 02 ...
Page 304: ...1K 4 Exhaust System ...
Page 346: ...2D 5 Wheels and Tires ...
Page 438: ...3D 26 Propeller Shafts ...
Page 482: ...4D 6 Parking Brake ...
Page 512: ...5A 28 Automatic Transmission ...
Page 624: ...Prepared by December 2008 Part No 99500 44080 03E Printed in U S A 624 ...