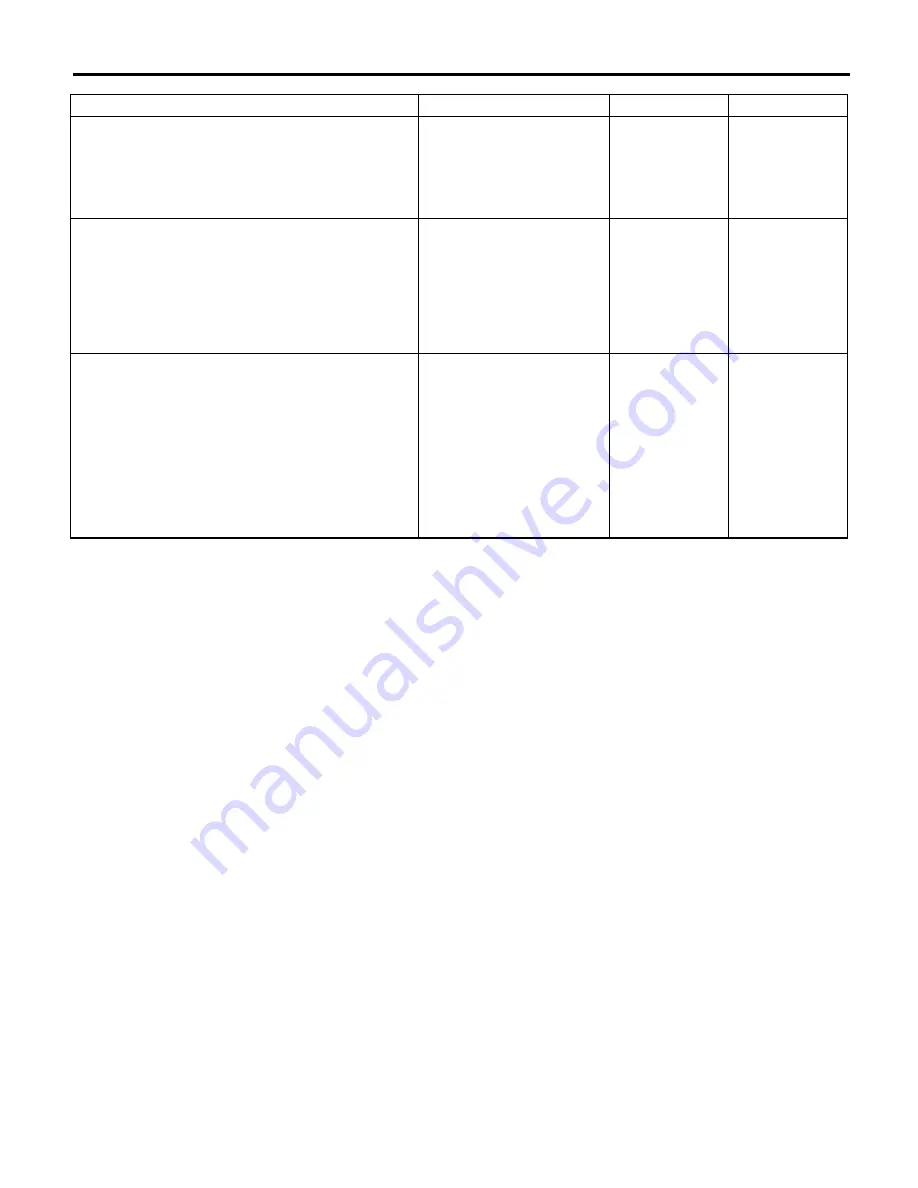
TPM(diag)-23
Tire Pressure Warning Light / Trouble Indicator Light Illumination Pattern
TIRE PRESSURE MONITORING SYSTEM (DIAGNOSTICS)
Step
Check
Yes
No
1
CHECK DTC.
Connect the Subaru Select Monitor, and read
the Diagnostic Trouble Code. <Ref. to
TPM(diag)-8, READ DIAGNOSTIC TROUBLE
CODE (DTC), OPERATION, Subaru Select
Monitor.>
Is a DTC displayed?
Perform the diag-
nosis according to
the DTC. <Ref. to
TPM(diag)-26, List
of Diagnostic Trou-
ble Code (DTC).>
Go to step
2
.
2
CHECK TRANSMITTER (ID).
Display the transmitter ID of the tire pressure
monitor system.
Is the transmitter ID registered? Go to step
3
.
Register the trans-
mitter ID. <Ref. to
TPM(diag)-10,
REGISTER
TRANSMITTER
ID, OPERATION,
Subaru Select
Monitor.>
3
CHECK TRANSMITTER DATA OUTPUT.
1) Select data display of the tire pressure mon-
itoring.
2) Start the engine and check the tire pressure
warning light output.
Is the warning light output ON? Replace the tire
pressure monitor-
ing control module.
<Ref. to WT-13,
TIRE PRESSURE
MONITORING
CONTROL MOD-
ULE, REMOVAL,
Tire Pressure
Monitoring Sys-
tem.>
Replace the com-
bination meter.
<Ref. to IDI-16,
REMOVAL, Com-
bination Meter.>
Summary of Contents for 2009 IMPREZA
Page 18: ...PC 4 Precaution PRECAUTION...
Page 21: ...NT 4 Note NOTE Lift Rigid rack A Attachment NT 00241 A A Attachment NT 00242 A...
Page 23: ...NT 6 Note NOTE A Front B Rear 1 Front crossmember 2 Rear differential 1 2 A B NT 00210...
Page 66: ...PI 22 Pre delivery Inspection PRE DELIVERY INSPECTION...
Page 112: ...PM 48 A C Filter PERIODIC MAINTENANCE SERVICES...
Page 219: ...IN H4SO 10 Resonator Chamber INTAKE INDUCTION...
Page 324: ...ME H4SO 106 Engine Noise MECHANICAL...
Page 388: ...SP H4SO 6 Accelerator Pedal SPEED CONTROL SYSTEMS...
Page 395: ...IG H4SO 8 Spark Plug Cord IGNITION...
Page 418: ...SC H4SO 24 Battery STARTING CHARGING SYSTEMS...
Page 725: ...EN H4SO diag 308 General Diagnostic Table ENGINE DIAGNOSTICS...
Page 926: ...GD H4SO 202 Diagnostic Trouble Code DTC Detecting Criteria GENERAL DESCRIPTION...
Page 1181: ...EX H4DOTC 16 Muffler EXHAUST...
Page 1212: ...CO H4DOTC 32 Engine Cooling System Trouble in General COOLING...
Page 1221: ...IG H4DOTC 8 Ignition Coil IGNITION...
Page 1818: ...GD H4DOTC 230 Diagnostic Trouble Code DTC Detecting Criteria GENERAL DESCRIPTION...
Page 2154: ...5MT 82 General Diagnostic Table MANUAL TRANSMISSION AND DIFFERENTIAL...
Page 2227: ...RS 20 General Diagnostic Table REAR SUSPENSION...
Page 2364: ...DS 36 General Diagnostic Table DRIVE SHAFT SYSTEM...
Page 2615: ...BR 48 General Diagnostic Table BRAKE...
Page 2624: ...PB 10 General Diagnostic Table PARKING BRAKE...
Page 2681: ...PS 58 General Diagnostic Table POWER ASSISTED SYSTEM POWER STEERING...
Page 2730: ...AC 50 General Diagnostic Table HVAC SYSTEM HEATER VENTILATOR AND A C...
Page 2961: ...SB 22 Rear Seat Belt SEAT BELT SYSTEM...
Page 3035: ...COM 6 Horn Switch COMMUNICATION SYSTEM...
Page 3070: ...GW 36 Wiper Deicer System GLASS WINDOWS MIRRORS...
Page 3092: ...IDI 22 Clock INSTRUMENTATION DRIVER INFO...
Page 3158: ...SL 54 Immobilizer Antenna SECURITY AND LOCKS...
Page 3167: ...SR 10 Sunshade SUNROOF T TOP CONVERTIBLE TOP SUNROOF...
Page 3240: ...EI 74 Ornament EXTERIOR INTERIOR TRIM...
Page 3286: ...CC 12 Neutral Position Switch CRUISE CONTROL SYSTEM...
Page 3311: ...CC diag 26 Diagnostic Procedure with Cancel Code CRUISE CONTROL SYSTEM DIAGNOSTICS...
Page 3421: ...LAN diag 88 General Diagnostic Table LAN SYSTEM DIAGNOSTICS...
Page 3486: ...WI 67 Remote Engine Start System WIRING SYSTEM...