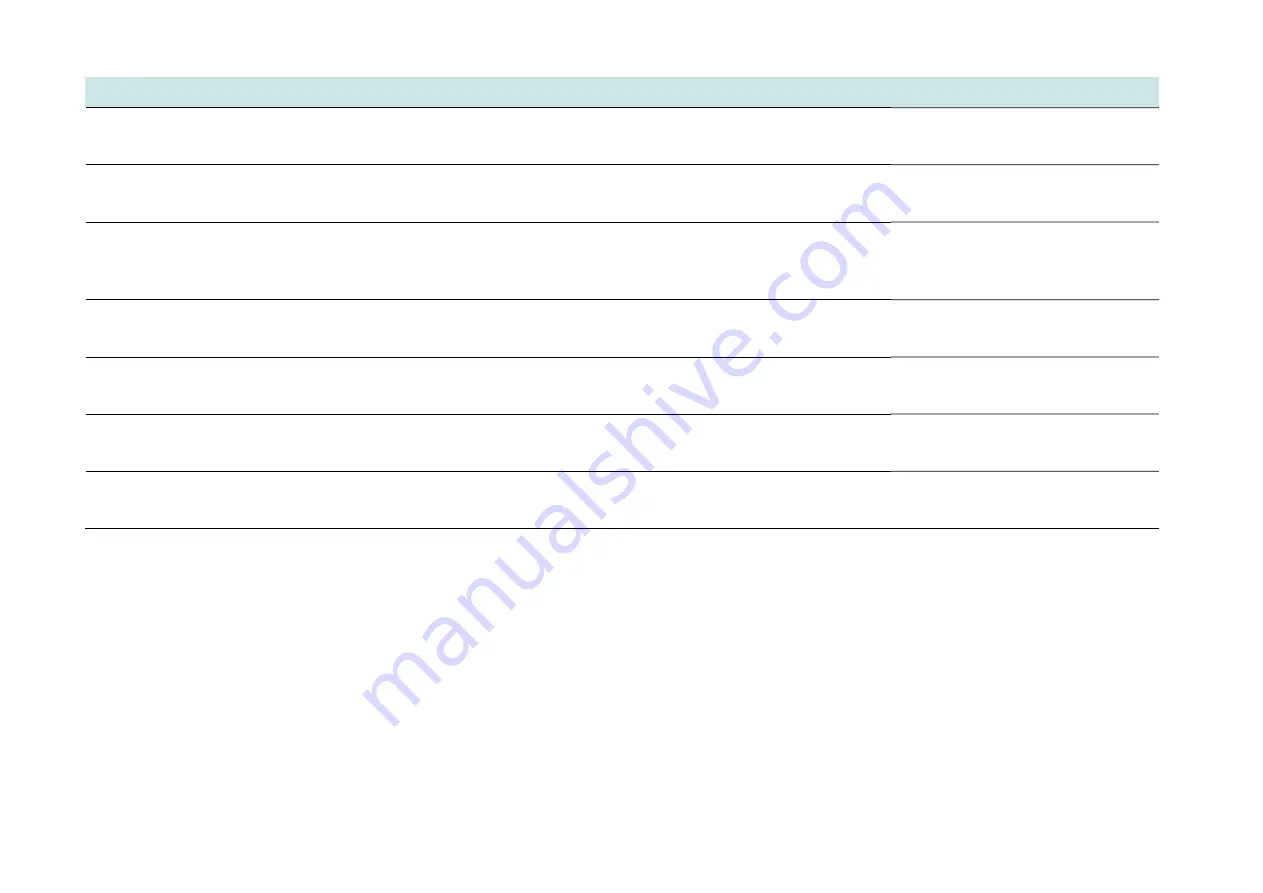
D-132
A p p e n d i x D : P r o g r a m m i n g
AC890PX AC Drive
Parameter Descriptions
JOGGING
PREF: 92.15
Default: FALSE
Range: FALSE / TRUE
Indicates that the Drive is in the JOG mode.
STOPPING
PREF: 92.16
Default: FALSE
Range: FALSE / TRUE
Indicates that the Drive is stopping.
OUTPUT CONTACTOR
PREF: 92.17
Default: FALSE
Range: FALSE / TRUE
Output to be used to drive an external contactor in the motor output. This contactor is normally closed unless a Trip condition has occurred or the
Drive goes into the re-configuration mode.
SWITCH ON ENABLE
PREF: 92.18
Default: FALSE
Range: FALSE / TRUE
Sometimes referred to as READY TO SWITCH ON, this parameter indicates that the Drive will accept a run command.
SWITCHED ON
PREF: 92.19
Default: FALSE
Range: FALSE / TRUE
Run accepted. Waiting for CONTACTOR CLOSED and any motor deflux delay to be completed
READY
PREF: 92.20
Default: FALSE
Range: FALSE / TRUE
Indicates that the Drive’s power stack is operable and the Drive will run if enabled.
SYSTEM RESET
PREF: 92.21
Default: FALSE
Range: FALSE / TRUE
TRUE for a single block diagram execution cycle after the Drive enters either RUN or JOG mode.
Summary of Contents for AC890PX Series
Page 8: ......
Page 12: ...1 4 C h a p t e r 1 G e t t i n g S t a r t e d AC890PX AC Drive...
Page 17: ...C h a p t e r 2 P r o d u c t O v e r v i e w 2 5 AC890PX AC Drive 890PX bottom wire entry...
Page 22: ...2 10 C h a p t e r 2 P r o d u c t O v e r v i e w AC890PX AC Drive...
Page 74: ...4 8 C h a p t e r 4 A s s o c i a t e d E q u i p m e n t AC890PX AC Drive...
Page 96: ...5 22 C h a p t e r 5 O p e r a t i n g t h e D r i v e AC890PX AC Drive...
Page 162: ...8 22 C h a p t e r 8 T r i p s F a u l t F i n d i n g AC890PX AC Drive...
Page 170: ...9 8 C h a p t e r 9 R o u t i n e M a i n t e n a n c e R e p a i r AC890PX AC Drive...
Page 286: ...D 84 A p p e n d i x D P r o g r a m m i n g AC890PX AC Drive Functional Description...